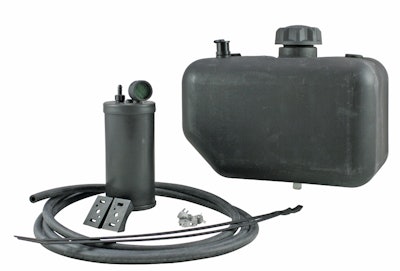
The California Air Resources Board (CARB) and the Environmental Protection Agency (EPA) have implemented regulations to reduce the level of evaporative gasoline emissions in the air. While this is currently only for gasoline fueled engines, there is future potential for the vapor emissions regulations to carry over into diesel-powered machines, as past regulatory trends indicate.
While metal fuel tanks have inherently low vapor emissions, to achieve benefits such as reduced weight, ease of integration and design flexibility, plastic molded fuel tanks can be used. Manufacturers such as Messe Orbitron Dunne Co. (MOD) of Ashtabula, OH, and Flambeau Fluid Systems, Baraboo, WI, have invested in testing and obtaining executive orders from CARB and certificates from the EPA for their tanks. The pre-certified product offerings save manufacturers time—upwards of 5 months saved for testing and certification—and money spent getting tank designs certified, reducing overall lead time.
“We did a lot of testing of different materials and processes and came up with a method to get a low permeation barrier on the tanks,” says Dan Hilfiker, Business Unit Manager – Fluid Systems, Flambeau. “We offer stock tanks that people can buy, do minor modifications to and move right into production with them already pre-certified through Flambeau.”
Flambeau did extensive testing to create a broad window of certification to encompass a wide range of fuel tanks—approximately three years worth of testing to accomplish the certification. MOD, too, had its proprietary tank design EPA certified. “If a customer has a tank of similar design that falls into our family of tanks, we can mold their design and use our certification,” says Mike Dorsey, Vice President of Manufacturing and Engineering at MOD. “We have to use our certification number on the tank, but it allows the customer to avoid going through the exhaustive and expensive EPA testing and certification.”
Caps and components that can be added to a tank design are also CARB and EPA compliant, to make working with a supplier a one stop process.
MOD specializes in custom rotation molded products including fuel tanks, but President Bob Dunne states that in the past two to three years, the market for off-the-shelf tanks has grown. “We have found that with the EPA standards coming in, designers are more likely to give up some of the niceties for compliance,” Dunne says. “In many cases, equipment designers are not able to consolidate tanks like they were in other product lines, and they’re turning to us to come up with a relatively common design that they can incorporate earlier into the design process.”
Materials in pieces and layers
An advantage plastic molded tanks see over metal tanks is the one-piece design. Metal tanks are only as good as their weakest weld, and design options are more limited than the flexible extrusion and shaping process of plastic. Rotationally molded single-piece tanks eliminate fasteners, joints, seals, solders and welds that can weaken complex assemblies.
MOD utilizes a three layer design currently with 23 gallon and 7 gallon standard options. The proprietary design includes two layers of polyethylene plastic separated by a barrier layer of ethylene vinyl alcohol (EVOH).
The cross-linked polyethylene material performs well in cold temperatures without cracking. The tanks are virtually stress-free, designed to distort in high temperatures without rupturing or catching fire, yet have a memory to return to their original shape. The tank’s integrity is assured in temperatures ranging from -20 to 175 F. MOD’s marine tank options are resistant to salt water, fresh water, acid and solvent deterioration.
Flambeau is in an evolutionary period with its material, currently utilizing a two-part process. The secondary process adds a fluorinated barrier to the tank. “We are working today on other developments of other materials and processes to make it more streamlined and less costly, with fewer steps involved,” explains Hilfiker. “We did the two step process to have something to introduce to the marketplace, and now that we have a solution we want to continue to improve upon it with new materials.”
The thickness of the tank is dependent on the size of the tank and can range, for Flambeau, anywhere from 3 to 6 mm in thickness. The tanks heavy construction is designed for conditions such as cold impact. “We do a lot of testing at Flambeau around impact testing,” says Hilfiker.
The use of plastic materials further helps with weight reduction efforts, and allows for more unique shapes at lower cost. Metal tanks are still available, and according to Hilfiker are on the rise again. “Metal tanks have had a resurgence because of the low permeation standards because metal has negligible permeation. But, they’re costly and more difficult to make, so you run into challenges where an OEM can’t get a certain product design they want because of the lack of design flexibility with metal.”
Companies like Flambeau and MOD are working to get the word out to OEMs that there are plastic tanks available that can meet the vapor regulations if the OEM wants an alternative solution to metal options.