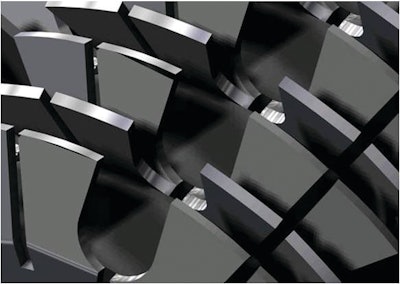
Proper filtration ensures the longevity of a vehicle and its components. Most vehicles today include a 10 micron filter, which is able to catch particulates in the range of 10 microns and larger.
To ensure particles smaller than 10 microns don’t make it into a vehicle’s fluid system, Magnom Corp., Warwick, U.K., has developed a range of magnetic filtration products which can capture the smallest of contaminants. Testing of Magnom’s magnetic filter has shown the core is able to remove particles 0.07 microns in size as well as up to 97% of particles in a single pass through the filter’s core.
The problem
According to Magnom, 80% to 90% of components used in the world’s vehicles are manufactured from carbon steel. When a vehicle is being used for the first time, it goes through what is known as a start-up or break-in period, during which vehicle components will often work against one another for the first time. As these steel components work together, several pieces of steel begin flaking off. These steel, or ferrous contaminants will then collect and circulate within fluid systems.
Most vehicles have their oil and filters changed after this break-in period to reduce the amount of ferrous contaminants. Unfortunately, most of the break-in contaminants are too small, generally between 1 and 10 microns, to be captured by traditional filters and will therefore continue building up and circulating through fluid systems during the vehicles’ lifespan.
Magnom’s magnetic core filter is designed to trap the ferrous contaminants and keep them out of fluid systems.
It’s all in the core
While many aviation hydraulics systems already utilize a form of magnetic filtration, the company says current magnetic filters can actually cause more problems. In order for the magnetic filter to work properly, the contaminants have to be very close to the magnetic source. Over time, the contaminants build up on the magnet, which eventually will be unable to hold onto them, so they wind up back in the vehicle’s fluid systems. And, because the contaminants have been exposed to a magnetic field, they stay clumped together.
This is why a single component in a system will suddenly fail, even though it seemed to be in perfect working condition. Only once the failed component is inspected will engineers find the carbon steel contaminants. The hard steel often becomes embedded into softer wear metals used at the opening of the component where fluid is introduced.
The solution can be found within the filter’s magnetic core. Magnom placed two carbon steel plates around the magnet to intensify its flux field. Steel enables the magnetic flux field to be 15 times more efficient than using just a magnet. Using the steel also focuses the magnetic field into the fluid flow to trap the ferrous contaminants. With the increased holding capacity of the magnetic core, contaminants will not wash back into the hydraulic or lubrication system.
Fluid flow channels cut directly into the steel plates provide a cross sectional area for fluid to easily pass through. The total area is designed to be 15% larger than the cross sectional flow area of feed pipes or hoses delivering fluid into the filter’s magnetic core. Large flow areas in the magnetic core ensure a minimal pressure drop, even when full of contaminant, allowing the filter to be placed anywhere in a hydraulic system—even in a full fluid flow area, such as in front of a variable displacement pump.
Magnom first developed its magnetic core filter in partnership with the Formula 1 Racing industry. However, most recently the company worked with Caterpillar Inc., Peoria, IL, to place the filters in Caterpillar equipment.
For three years Magnom worked with Whayne Supply, a large Caterpillar dealer, to develop a custom magnetic filter. During the testing phase Whayne Supply was already able to see the potential for a reduction in operating costs, as well as unscheduled downtimes.