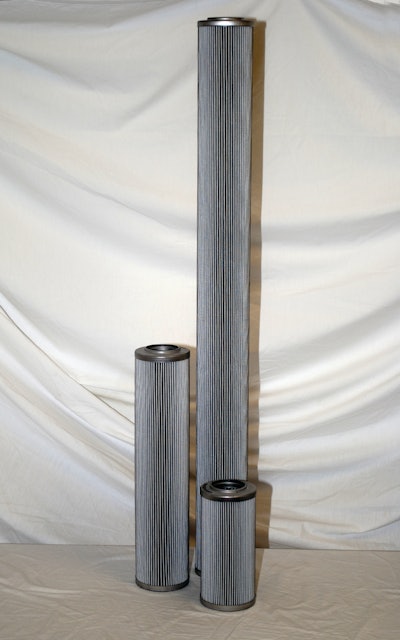
A properly designed fuel filter prevents water or particles that may be in fuel from entering a vehicle’s fuel system and engine. Small pieces of dirt or dust that don’t get filtered out of the fuel can get stuck in the openings of injectors, causing decreased engine performance or system malfunctions. Ted Loftis, Director of Engineering at Cummins Filtration (10071588), Louisville, KY, says clean fuel enables an engine to consistently operate at its designed efficiency, emissions and economy targets during its lifetime.
Fuel cleanliness has become increasingly more important within recent years due in part to the implementation of Tier 4 engines. Because these engines work at higher pressures and have smaller injector openings, even the smallest amount of water or particulate can cause the engine to underperform. According to Karl Thomas, Product Manager for Fuel Filtration at Schroeder Industries (10056059), Leetsdale, PA, fuel for Tier 4 engines has to be 100 times cleaner than the fuel used in Tier 3 engines. Where Tier 3 diesel engines can operate with between 1,300 and 2,500 particles greater than 4 microns in the fuel, Tier 4 engines can only have between 20 and 40 particles greater than 4 microns entering the engine. “The cleaner the fuel, the more efficient it will burn,” says Thomas. “And the better it burns, the better the engine performs.” New fuel cleanliness standards are now being implemented to guide filter design in order to meet the needs of Tier 4 engines (see sidebar, pg. xx).
Water and particulate removal
Now, along with having to capture an increased amount of particulate due to smaller injector openings, fuel filters must also be able to prevent subvisible particulate from entering the engine. Fuel filters need to remove particulate in the 1 to 5 micron range—about the size of a red blood cell—whereas 20 years ago particulate removal was in the 50 micron range (the human eye can see 40 microns and above). “We need to make sure the particulate removal is happening before it hits the pump or injector because it’s been shown that even sub 10 micron particles can wear on a high injection fuel pump…and clog [openings] of the injectors,” says Tom Muzik, Global Engineering Manager at Parker Velcon Filtration Division (Parker Velcon, 10224743), Colorado Springs, CO.
To capture larger amounts of microscopic particulate, fuel filter manufacturers have been working to develop new types of filtration media. While traditionally fuel filters have used cellulose and cellulose-blended media to remove solid particulate, this media type is no longer able to meet the contaminant removal needs of newer engines. “Inert inorganic bonded fixed pore fibers are needed to capture finer particulate, plus maintain a reasonable element life,” says Tim Mills, Product Manager at Kaydon Filtration (10854439), LaGrange, GA.
In early 2013, Cummins Filtration introduced its latest filtration media, NanoNet (learn more, 10851626 and 10667433), which uses smaller fibers to enhance a filter’s ability to capture subvisible particulates. “Smaller fibers provide higher efficiency to capture smaller particles while providing a greater [holding] capacity for contaminants,” says Neha Takawale, Global Product Manager at Cummins Filtration. Takawale further explains that the NanoNet fuel filters have 7 to 13 times greater retention of harmful particles within the filtration media during engine vibration and fuel surge. This high retention rate ensures particles don’t slip through the filter or get knocked loose and make their way into the fuel, engine or other vehicle systems.
With engines working at higher pressures—15,000 psi and above—removing water from fuel is essential to maintaining the performance of an engine. While just 20 years ago engines were able to burn water that entered the fuel system, now even the smallest amount of water can cause an injector tip to blow and the engine to need overhauling, says Dan Bigelow, Chief Operating Officer at Separ Filter (10056076), Fort Lauderdale, FL. “We’re at an interesting point where it is more important today to have quality filtration on the equipment to protect the engine than we ever have before,” says Bigelow.
For water removal, many filter manufacturers will use an absorbent technology to literally absorb water from the fuel. Once the absorbent can no longer absorb and hold water, the filter must be replaced. The Aquacon diesel filters (learn more, 10813422) from Parker Velcon use an absorbent technology called Super Absorbing Polymer, which is in the same family of chemical products as diapers. “It actually chemically bonds the water to a polymer and it’s no longer water at that point,” says Muzik.
In conjunction with more absorbent filtration media, water separators and coalescers can be used to further enhance water and particulate removal. The SWK-2000 Series of fuel water separators (learn more, 1088602) from Separ Filter, for example, use five stages of filtration to separate water and the majority of particles prior to the fuel passing through the filter media. Coalescers, on the other hand, continually remove water by gathering droplets of water from the fuel and dropping them into a sump. Unlike an absorbent which requires users to replace the filter once it is no longer able to absorb and hold water, coalescers have a sump that needs to be drained on a periodic basis. “Effectively, customers can have continuous operation of [a] filter system without having to change elements due to water,” says Schroeder Industries’ Thomas.
Changes in fuel
Though fuel quality has improved within recent years, there are still many places around the globe where fuel quality is questionable. According to Cummins’ Loftis, 50% of the world’s fuel supply does not meet current ISO fuel cleanliness standards. “In many of our field experiences [we] have seen fuel samples 30 times dirtier than the ISO 18/16/13 specified by the fuel injection equipment manufacturers,” adds Barry Verdgan, Research Fellow at Cummins Filtration. ISO 18/16/13 states no more than between 1,300 to 2,500 particles greater than 4 micron can be present in the fuel.
Some fuel suppliers have also been known to dilute their diesel fuel with water in order to trick customers into thinking they’ve received more fuel than they actually have. Because of practices like this, Muzik notes the importance of filtering fuel before it even enters a vehicle (see sidebar, pg. xx) in addition to using on-board fuel filtration systems.
Along with poor fuel quality, filter manufacturers have also had to contend with the introduction of biofuels and ultra low sulfur diesel (ULSD). Biofuel is challenging because it is hygroscopic, which means it attracts water into the fuel. “It’s actually like a magnet and it pulls water [in] from the atmosphere and surroundings,” says Bigelow. In addition, Mills of Kaydon Filtration says as biodiesel grades increase, so does the aggressiveness of those fluids, requiring different metallurgy and filter media binders to be used in the fuel filters. Bigelow says Separ Filters had to change the type of materials its o-rings, seals and other components used in the filtration systems were made from to ensure compatibility with up to B100 biodiesel.
Poor quality biofuels can also be an issue, notes Muzik. If a biofuel is not refined properly, a bi-product called glycerin will become present in the fuel. Glycerin is basically the same thing as soap and it will coat fuel filters as well as potentially deactivate coalescers, inhibiting their ability to remove water from the fuel. Muzik says this was more of an issue in the past “and [people] are being more diligent in specifying the quality of the biofuel they’re putting into their engines.”
With ULSD, water removal is also a challenge because the chemistry of the fuel changed from the previous low sulfur version of diesel. ULSD contains 15 parts per million (ppm) of sulfur, whereas low sulfur diesel contains 500 ppm. Thomas of Schroeder Industries says the change in fuel chemistry “changed the surface tension of [the] diesel and made it harder to get water out of the fuel.”
Challenges with ULSD can also arise from the additives used in them. Verdgan says some blends use additives which can precipitate out as soaps when metal ions are present, causing injector sticking and in extreme cases plugged filters.
OEM collaboration
Working together with an OEM or engine manufacturer on the design and integration of a fuel filtration system is beneficial to all parties involved. Muzik says each engine manufacturer specifies the quality of fuel being delivered to the engine at a certain volume, making collaboration early on in the design process vital to ensuring the correct filter is used to meet the manufacturer’s individual filtration needs. Early engagement allows filter manufacturers to develop filtration systems that meet and exceed the requirements of OEMs, adds Cummins’ Takawale. “It allows us to design systems that fit the engine design, operating environment and application specific requirements,” she says. Specifying the right filter for an engine helps maintain fuel injector performance as well as enables the engine to meet its fuel economy and emissions targets.
Many OEMs have their own stringent tests for performance in certain types of applications or real-world conditions. “Working with the OEMs upfront, we develop more real-world tests to design [a] product that meets these conditions,” says Takawale. Upfront collaboration with an OEM also allows filter manufacturers to indicate auxiliary components such as fuel pumps, housings for the filter, coalescers and other components that will create an entire system that meets the OEM’s fuel filtration needs. In addition, collaborating on a filtration system design ensures it will be configured correctly to fit within the space parameters of the vehicle.
OEM collaborations also enable filter manufacturers to further customize their designs for specific application needs such as adding a heater to the filter for colder climates or developing custom sensors for service notifications. Bigelow says partnering with OEMs allows Separ Filter to connect sensors, such as water sensors, to the engine control unit (ECU) in order to alert vehicle operators of the presence of water in the fuel. “We will customize our sensors to output directly what [OEMs] need,” he says. “It’s a win-win to strive beyond simply a supplier relationship.”
As engine technologies continue to progress, many engine manufacturers foresee injection pressures doubling again, causing injector openings to decrease in size even more. This will further emphasize the need to have cleaner fuels running through a vehicle. Muzik says fuel filtration is only going to grow in importance over the coming years to ensure engines run smoothly and efficiently. “[Engine manufacturers are] not going to get their technology for a more efficient diesel engine without filtration,” says Muzik. “It’s going to be an integral part of the process.”