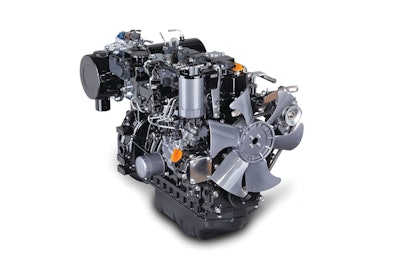
The process of spec’ing an engine has definitely changed with the advent of Tier 4 technology. Advanced technology comes with additional cost but can be quickly recovered by the customer through improved machine efficiency. To gain the most benefit from current technology, OEMs should work closely with the engine supplier to design an optimized solution. This dictates that the machine and engine communicate and make the best use of available power.
Many manufacturers, including FPT Industrial (company information, 10056369), Torino, Italy, have increased in power density – with the engines pumping out more power per cubic centimeter of displacement. “The Tier 4B/Stage IV emission regulations (already applied to engines with power output up to 56 kW), see an increase in power densities with engine capacity remaining roughly the same,” says Carlo Actis, Vice President Marketing and Product Management, FPT Industrial. “For engines giving out between 56 and 129 kW (to which Tier 4A applies until 12/2014), power density increase has been particularly substantial in the move from Tier 3 standards to today’s regulations.” This is due to the introduction of electronic injection systems and high performance air handling systems, which have resulted in lower emissions and the same or lower fuel consumption with more power.
Mike Alvin, Marketing Manager at Deutz Corp. (company information, 10055290), Norcross, GA, explains that increased power densities result from high pressure common rail fuel delivery systems and electronically controlled fuel injection coupled with turbocharging. For instance, the company’s 4.5-liter engines are being replaced by 3.6-liter engines offering the same performance. This reduces weight and leaves more room available for advanced cooling systems and engine aftertreatment systems which are required to meet current emissions requirements.
Perkins Engines Company Ltd. (company information, 10055932), Peterborough, United Kingdom, has followed a similar approach. “At Perkins we utilize a range of technologies to increase power density, from common rail high pressure fuel injection to a variety of aftertreatment solutions, which also support the required levels of transient response,” says Mike Cullen, 1200 Series Product Marketing Manager at Perkins.
Despite this trend toward greater power density, reliability and durability have not been compromised. “New technologies and their applications on the engine get thoroughly tested, not only on test benches but also in real life situations. This gives customers the longevity they expect while at the same time guaranteeing emissions limits compliance throughout the total lifespan of the engine,” says Actis
Increased power density can be directly traced back to advancements made to meet Tier 4 emissions requirements. “In engines of similar or same displacement, the main factors that contribute to an increase in specific power are: utilization of more complex-structure turbochargers, such as variable-geometry or dual-stage; an increase in peak cylinder pressure; and the use of an SCR-only aftertreatment system without any recycling of exhaust gas in cylinder, especially in engines with a displacement higher than four liters,” says Actis.
One of the latest turbocharging technologies is the variable geometry turbocharger (VGT). “VGTs allow for better performance when compared with waste gate (WG) or fixed geometry turbocharger (FGT) solutions,” says Actis. “VGTs are the best option when used in vehicles where there is a need for optimum transient response. However, because of their more complex structure and electronic management, as a product they are more expensive compared to the less complex FGT and WG unit.”
But even higher performance can be produced by solutions such as the dual stage or series turbochargers. “However, whether in on-road or off-road applications, one often chooses dual-stage turbochargers in engines that use EGR (instead of SCR-only solutions) to compensate for the amount of power lost by [EGR only],” notes Actis.
“Perkins 1200 and 850 Series engines utilize a suite of proven turbocharging technologies to increase power density across the range,” says Cullen. “Proven for the off-highway market, and featuring durable smart waste gate technology, our series turbocharging delivers a range of end-user benefits including improved specific fuel consumption, reliability, transient response and power density.”
This increase in power density creates opportunities. “With increased power and torque across the Perkins range at Tier 4 Interim/Stage IIIB and Tier 4 Final/Stage IV, OEMs have a number of options available to them, dependent upon their specific requirements,” says Cullen. “The Perkins 1200 Series delivers more power and 35% more torque compared to Tier 3 models, yet fuel consumption is better by 8%, allowing the end user to get more done, faster and with less fuel.”
One opportunity is to use a smaller engine. For instance Perkins' 7-liter, 6-cylinder engine is now capable of producing 300 hp. “The 6-cylinder offering gives OEMs—who may have previously chosen a larger engine—the choice of the same power from a smaller engine package,” says Cullen.
The same is true for the compact 850 Series. “A 3.4-liter unit can do the work of a much larger engine. This engine provides a 40% increase in power and up to 60% more torque available compared to Tier 3,” says Cullen. “With the trend for downsizing machines, Perkins 1200, 850 and 400 Series allow equipment manufacturers great flexibility, while still benefitting from increased power density and fuel economy.”
But engine sizing is really determined by the application. “Engine choice is very much driven by the sector and specific application,” says Cullen. “The flexibility and overlap in the powers across the Perkins engine range mean OEMs have a choice of engines that meet their specific application requirements.”
Many OEMs use the increased power density to boost power output rather than downsizing the engine. “In high horsepower off-road situations, where engine downsizing is not a trend, power density increase is answering the demand for improved vehicle efficiency, delivering more absolute power with the same capacity engine,” says Actis. “Off-road is driven more and more by the need to optimize the vehicle’s efficiency. The way an engine performs efficiently, compared to any other alternative, is not and cannot be exclusively linked to capacity.”
Balance available engine power with utilization
Some OEMs are working to balance available horsepower with the actual utilization. This can be a challenge when customers are used to certain-size machines being offered with a specified horsepower rating.
“Often, horsepower sells,” says Scott Siegel, Application Engineer at Yanmar America Corp. (company information, 10056323), Adairsville, GA. One machine will claim 25 hp and a competitive unit will advertise 29 hp. “It doesn’t matter if the machine never needs more than 20 hp, 29 must be better than 25.” Marketing often overrules actual demand. “Sometimes engine selection is truly based on putting a big number on the side of the machine.”
Load studies back up this claim. “When we do load studies, some applications never exceed 60%,” says Siegel. “Unfortunately some applications may spend most of their time under 20% rated power. With increased customer education of the systems, maybe we can change the direction of that trend. We could improve efficiency and reduce the total cost of ownership.”
Too much is not always better. “It is always more efficient to use the smallest engine that can provide the necessary power,” says Siegel. “There is less rotating mass, less drag.” Some OEMs will install a 100-hp engine when the equipment only draws 50 hp.
The move to Tier 4 makes it even more critical to size the engine appropriately. Higher engine loads produce more heat. “As long as you are keeping the exhaust temperature up, you have little or no need for active regeneration,” explains Siegel. “Some OEMs have been able to step down notably in power and have still been able to keep the performance up.”
Fuel consumption can also be impacted by a poor engine match. “Fuel consumption can be significantly impacted by the loading because of the required regeneration,” notes Siegel. “With the high load machines, you get all of the key efficiency benefits of the common rail injection, and they don’t require much additional fuel for regeneration. The customer has to be aware that if you oversize the engine, which is very common in our industry, it doesn’t burn hot enough and there has to be more regeneration, which can end up compromising fuel efficiency versus the old engines. The higher the load, the better the improvement is in fuel efficiency.”
It is a lot better to have an appropriately-sized engine using a good portion of its capacity. “You don’t want them severely under loaded,” says Siegel. “You don’t want them overloaded, but they are more efficient at a higher percentage load.”
You must really understand the engine load ratings. “In our published values, we have an intermittent power rating and a continuous-use power rating,” says Siegel. “We suggest that machines be sized so they don’t spend a lot of time over 90% load. That 10% is there for margin and occasional use when necessary. As long as you are staying under 90%, most of our engines outlast the machines.”
The electronic advantage
Electronic engines are game changers. “Everything from 25 hp to 75 hp has gone from mechanical pumps to common rail,” says Siegel. “That is a totally different ballgame going from a mechanical engine to a modern common rail engine.” The fuel injection systems on mechanical engines were rather simple. “Old injectors were just pop-off valves. They put in the same amount of fuel at the same time regardless of anything else.”
The modern common rail systems use injectors capable of multiple injections per cycle and they are precisely controlled by sensors and the ECU. “With the common rail fuel injection system you can set anything to be dependent on anything else, whether it is coolant temperature, air temperature, altitude, fuel temperature or loading, for example,” says Siegel.
You need to offset additional cost with higher performance. “You take a mechanical, non-electronic engine and then go to a common-rail, highly sensored engine, the expense goes up,” says Siegel. “But so does the information available. You are able to monitor everything, and everything is under control.
“The engine controller can communicate a tremendous amount of information to a machine controller,” says Siegel. “All of that data is accessible to the machine controller with just the two CAN wires.” This allows close integration between the machine and engine. “The engine controller and the machine controller can work together and deliver better performance, even with less power,” explains Siegel. “The machine controllers can see very small changes in engine load, so they react instantly if they need to apportion power between systems.”
It is really about total machine optimization. “With the increased level of complexity, which goes hand-in-hand with the introduction of new emissions regulations, it is not sufficient anymore to only manage the engine,” says Actis. “In the future we will see that further increases in overall productivity and system efficiency will be achieved through managing the complexity of all energy resources and energy demands of any commercial on- or off-road application.”
Future gains will really focus on a systems approach. “Although there is still some potential to make an internal combustion engine more efficient itself, the higher amount of efficiency increase is to be seen within the whole vehicle,” says Actis. “Simulation results show a significant decrease (>10%) in fuel consumption if the vehicle energy sources and the energy demands of a commercial on- and off-road vehicle are governed through predetermined datasets.
“Taking control of vehicle energy management through intelligent control systems, predicting load requests of the engine, managing not only the engine and its subsystems but all elements that can influence in some way the vehicle’s fluid consumption, will help to optimize the vehicle and answer the demand for high productivity and low total cost of ownership,” says Actis.