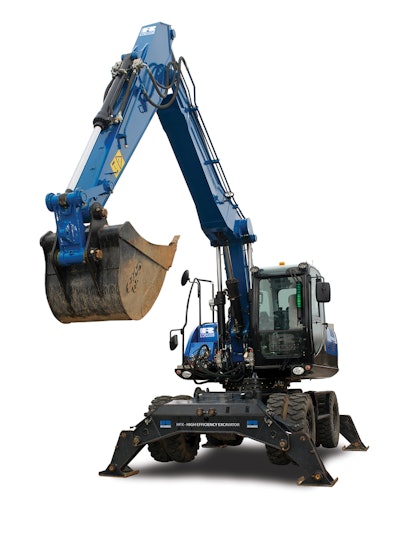
A scarceness of natural resources, growth of the population and ever tightening emissions regulations are driving manufacturers to search for unique solutions in the powertrain sector. But any solution needs to factor in the end-user cost. “Any way to save operation costs for the end user is going to be a preferred product,” says Joe McManus, Chief Engineer, Engine Products Group, Ricardo Inc. (company information, 10056030), Van Buren Township, MI.
There has been a shift in the market toward a consumer pull market. “Users are demanding access to low-cost fuels, so manufacturers need to supply them solutions,” says McManus.
Many solutions currently being explored to create more efficient powertrains include hybridization, electrification of various components, engine downsizing and downspeeding. “Engine downsizing is primarily enabled through design advancements and being able to increase peak cylinder pressure,” says McManus.
Automotive technologies are migrating into the commercial arena. “On the air handling side variable valve actuation has been common in the automotive sectors and it is making more progress into the heavy-duty sector to provide a more thorough and comprehensive way of air handling into the engine cylinder.” Precise fuel injection equipment is also a major enabler to reduce emissions and increase engine efficiency. “There is a trend to much higher injection pressure levels to get better combustion performance. That is enabled through more advanced control systems, such as closed-loop control of the combustion system itself.”
The questions regarding diesel engine aftertreatment have largely been settled. “On the aftertreatment side the general trend to apply SCR has been adopted globally,” says McManus.
Don’t overlook natural gas
Natural gas has been gaining momentum in the heavy-duty engine sector. “It has been demonstrated that natural gas is here to stay,” says McManus. “All different sectors from the rail industry to the heavy-trucking fleets and light-duty vehicles are all looking for ways to adopt and exploit the use of natural gas.”
Despite recent natural gas discoveries, the number of overall natural gas vehicles is falling behind the rest of the world’s appetite for natural gas vehicles. “We are becoming a natural gas exporter rather than importer. The energy production companies have recognized this as well as engine manufacturers across the whole supply chain, and mechanisms are being put in place to improve this,” says McManus. “The price differential between natural gas and diesel is making it such that it is a fuel that needs to be considered and efforts put into the development of the engines so it can become a primary transportation fuel.”
Natural gas could become a game changer. “Similar to what happened in the 1940s and 1950s when diesel fuel won out the race between gasoline and diesel fuel for heavy-duty transportation, there are some industry experts who say that natural gas is a similar interruptive fuel,” says McManus. “The diesel engine is not going to be completely replaced, but proper application and proper engineering to the natural gas engines will enable them to be very competitive options to an end user.”
Economic drivers behind natural gas for the transportation sector are well established. “Class 8 trucks consume a tremendous amount of fuel,” says McManus. “There is a price differential between natural gas and diesel that is going to maintain itself for quite some time. Even if you are not able to displace 100% of the diesel fuel going into the engine, there is still a very advantageous economic payback for the end user.”
He adds, “The other reason for adopting natural gas in this sector is the advantages that it has for reducing some of the greenhouse gas output, primarily CO2. Methane has a very advantageous carbon to hydrogen ratio, which equates to having less CO2. So as Europe and the United States develop CO2 legislation, enabling fleets to have a more advantageous carbon signature and finding solutions that enable that are going to be sought after.”
But natural gas is still a fossil fuel. “It does need to be pointed out that the natural gas emissions signature also does have a methane slip component and methane is a greenhouse gas that has a higher weighting factor than CO2,” says McManus. “Likewise, N2O is also a greenhouse gas and is a product of natural gas combustion. However, proper design and implementation will mitigate that either through catalysts or through proper combustion management.”
Aftertreatment is going to be a key component to enabling any system, whether it be diesel or natural gas. “The three-way catalyst technology is well established,” says McManus. There is also a methane oxidation catalyst (MOC). “Methane is not very reactive so we have to change the formulation and create a system to clean up those hydrocarbons.”
Off-highway options
In the off-highway arena there has been movement in electrification and hybridization of equipment.
“With few exceptions, decisions in the off-highway market are driven by costs,” says Dr. Scott Anderson, Chief Engineer, Controls and Algorithms at Ricardo Inc. “The machines typically see heavy load cycles and are operated many hours per year. For machine operators to be compelled to buy a hybridized or electrified version of a product, it must positively impact their life-cycle cost.” So the three basic aspects of life-cycle cost must be considered with respect to hybrids – the impact of the system on acquisition cost, the beneficial impact on operating cost and the useful life.
You may reduce the cost of the hybrid systems by identifying simple systems that can be easily integrated into the powertrain and vehicle architecture, and then apply hybridization where there is a potential for offsetting the hybrid component cost with reduction to other system costs – specifically the emissions systems or base engine cost. “Then identify opportunities to share components across products to improve the production component volumes and get the component cost down,” says Anderson.
But this can prove challenging in the off-highway sector where there are relatively low production volumes. “And the wide range of machine power levels make finding opportunities to use common hybrid components on multiple vehicles difficult,” says Anderson. “That makes the business case for both the OEMs and the component suppliers quite challenging.”
He adds, “Responding to this challenge will require insightful product planning along with support of robust models and analysis tools. For example, vehicle simulation tools can predict performance and fuel benefits of a hybrid machine relevant drive cycles. They can also help the OEMs understand the tradeoffs between ratings on the hybrid components and the benefit that they provide. By looking at multiple vehicle applications and applying appropriate cost models, OEMs may be able to identify the sweet spots for hybrid component sizes.”
When you consider the case for on-highway hybrids the first thing that probably comes to mind is energy recovery. “For off-highway those opportunities exist, but they are more limited,” says Anderson. For example, you can recover the potential energy when dropping the boom or slewing an excavator.
But the more important application of hybrid technology is the ability to peak load shave and handle transient engine loads, which allows you to size the engine for a steady-state base load. “One option is to run the engine at an even higher engine power level and extract more from the machine for better productivity,” says Anderson. “That also increases the engine load and leads to better fuel efficiency.”
Another option is to use a lower engine rating to get the same job done. “That can be particularly important for applications near U.S. emissions break points as an enabler for a less costly emissions solution near displacement break points in an engine manufacturer’s portfolio,” says Anderson. “Finding opportunities near Tier 4 displacement break points may allow products to be developed that produce the performance of conventional products rated above the break point but using a hybrid with a smaller engine that fits below the break point. That will help reduce cost and offset the hybrid system cost.”
Don’t expect hybrids to become mainstream overnight. “Off-highway OEMs are moving cautiously on hybrids, even where great technical solutions exist,” says Anderson. “The business case must be sensible. Because customers in this market expect high reliability, hybrid systems require extended validation before OEMs risk putting them into production.”
Today there are a few hybridized vehicles available. “The first production hybrid applications have deployed predominately electrical technology,” says Anderson. These include the Hitachi hybrid excavator, the Caterpillar D7E dozer and the John Deere 644K wheel loader.
That does not mean hydraulic hybridization does not deserve closer examination. “Because many off-highway machines already have high-pressure hydraulic systems on board, it is natural to consider the use of other technology for hybridization, such as hydraulic energy storage,” notes Anderson. “Applications that have high power, but not particularly high energy storage requirements, are typically in the sweet spot for hydraulic hybrid options.”
One major consideration when considering a hybrid technology is the useful life of the machine. “The effects of hybrid operating costs are amplified as the useful life of the system is extended,” says Anderson. “It is important to identify an application in which the vehicle is retained for long periods of time.”
You can also drive life-cycle costs by minimizing the initial cost of the technology. “For that reason, Ricardo feels there are applications for which flywheel system technology will be an ideal solution,” says Anderson. “We recently demonstrated a flywheel system on an excavator. The Ricardo demonstrator featured a hermetically sealed carbon fiber rotor driven through a magnetic gear for high efficiency. Using the magnetic gear drive allows us to remove the rotating seals and reduce the losses in the flywheel. It also eliminates the need for a vacuum management system.”
Ricardo expects the flywheel system to be considerably less expensive than the electric hybrid systems. “We should be targeting payback in less than two years,” says Anderson. “The flywheel avoids the significant battery replacement costs that may be needed in some electric hybrids. Because Ricardo believes the flywheel will deliver the best payback in some off-highway applications, we are continuing the development of production intent hardware.”
Total cost of ownership in truck market
Ricardo has developed an intensive tool to compare all aspects of what alternative technologies cost in the truck markets. “We analyzed the total cost of ownership for the segment. The model looked at both the vehicle operating expenses and vehicle capital expense,” says Ruth Latham, Associate in Strategic Consulting at Ricardo Inc. Technologies included diesel, natural gas, electric, hybrid-electric and hybrid-electric with natural gas.
Most of the technologies were fairly close in total cost of ownership with the exception of electric vehicles. “When you graph it out there is not a huge range in the total cost of ownership with the exception of the cost for electric vehicles because the capital expenditure is so high,” says Latham. “Electric vehicles have the lowest operating expenses, but they have significantly high capital expenses.”
The payback period for introducing new technologies ranges from one to 23 years. The technology that provides the best payback is heavily influenced by the duty cycle.
For Class 3 to 6 delivery vehicles, the lowest cost of ownership was natural gas even though the capital expense of the vehicle is higher. “This would likely be followed by a hybrid natural gas vehicle if one was available right now,” says Latham.
The results change with a work truck application. In this case the plug-in hybrid offers the lowest cost of ownership. “For a work truck the PTO operation strongly drives the value of plug-in hybrids,” says Latham. “We sized the battery so that the PTO operation for one shift was covered by the battery. The operating costs of the PTO can be reduced significantly from $5,000 on a diesel down to $357 on electricity. PTO capacity is based on the battery pack. Because of the long life people tend to own these vehicles for, even though the capital expenditure is fairly high, it in no way overwhelms the savings toward the operating expenses.”
For Class 8 on-highway trucks the lowest cost of ownership is still the traditional diesel engine. But it should be noted that duty cycle is incredibly important in this calculation.
Other factors that went into the calculations were fueling infrastructure and maintenance. “There are some maintenance features that are very different with new technology vehicles,” says Latham. “For instance, hybrid electric vehicles and electric vehicles with regenerative braking systems have significantly reduced brake replacements. That has a big impact on maintenance costs for high mileage duty cycles.”
Natural gas trucks have shorter oil change intervals recommended by the manufacturers. “You have to change your oil more often with a natural gas vehicle than a diesel vehicle,” says Latham. “On a hybrid electric vehicle battery size is important. Depending upon how long the vehicle is owned and how many cycles it goes through there is the risk on an electric vehicle that the battery pack itself will have to be replaced. For a large battery, that can have a significant impact on the maintenance costs.”
The model developed by Ricardo uses complex algorithms and considers many variables. It looks at six powertrain technology configurations as a baseline and 22 powertrain configurations. “The model is fairly extensive in which you can exchange anything from duty cycle to the cost of infrastructure to the oil change interval of the vehicle to the cost for maintenance,” says Latham.
You must understand the impact of technology on ownership costs. “The total cost of ownership can be reduced by 14% or increased by as much as 80% depending upon which technology, infrastructure and fuel you are looking at,” says Latham. “A Class 3 truck with natural gas and a work truck with plug-in hybrid natural gas have about a one-year payback period. A Class 3 electric vehicle has about a 23-year payback period driven significantly by capital expenditure. That is not including the incentives they have in New York and Chicago for electric vehicles.”