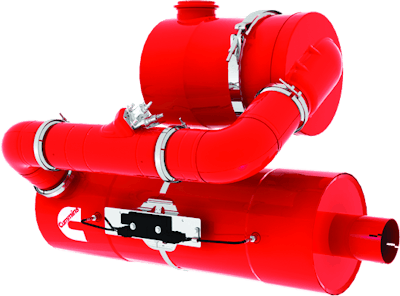
Engine efficiency is defined as the ratio of useful work done to the heat provided, which translates into fuel burned. This boils down to how much work can be completed per gallon of fuel consumed. Typically diesel engines have provided efficiencies between 40 and 50% at speeds up to 1,800 rpm. But the latest technologies including advanced fuel injection algorithms, improvements in internal combustion efficiency and electronic integration into the machines, translate into increased efficiency. Many of these advancements have been driven by EPA-mandated emissions regulations.
The march toward increased power densities - more power output per cubic inch displacement - is not new, but the latest designs are pushing the boundaries, resulting in even more efficient engines. This makes it necessary to carefully evaluate engine options before making a selection. You may be able to save weight, cost and increase operating efficiency by downsizing the engine. For example, in many truck applications there has been a trend from 15-liter toward 13-liter engines.
This is also occurring in the off-road realm. "Over the last few years, many OEMs have started to install more compact yet powerful engines into their applications," says Nick Stephenson, Product Marketing Manager at Perkins Engines Co. Ltd. "To ensure we meet the applicable emissions standards while providing our customers with the best performance and fuel economy possible, we've worked hard to increase the power density of our engine range – to deliver the same excellent performance through more compact engines. This has enabled customers to benefit from improved fuel economy with no sacrifice to productivity or performance, and often with very little change to their existing machine installations."
This trend is no accident. "Increasing power density is a key design objective for us," says Stephenson. "We use a wide suite of technologies to deliver the best possible performance from our engines, which varies by power range. At the heart of this, durability, reliability, performance, productivity and cost of ownership are all at the top of our list."
To be successful, the smaller engine needs to be more efficient and produce the same results as the larger displacement unit being replaced. "Increasing power density is what enables downsizing," says Paul Post, Manager PV&V and Engine Applications, John Deere Power Systems. "Engines are more efficient at a higher power density; therefore, downsizing results in higher engine efficiency." Another trend increasing engine efficiency is producing the engine speed at which useful torque is produced. "Downspeeding reduces engine friction losses, also resulting in higher engine efficiency."
The key benefits of downsizing are less fuel burned and the resultant reduction in greenhouse gasses. "Essentially, when we achieve the same performance using a smaller-displacement engine, there will be fuel consumption and exhaust emissions benefits," says Stephenson. "The same is generally true with engine speed – but it's more important to consider how a customer is going to use the engine in their particular range of machines, as the requirements can vary. That's why we work with customers during our engine design phase to make sure we can offer improved performance without sacrificing other key benefits, and really optimize our engines to suit machine needs. Rated speed and engine displacement only provide part of the story."
A trend toward smaller and slowerDownsizing and downspeeding are getting a lot of attention. "Downsizing and downspeeding offer opportunities to improve overall packaging, fuel economy and cost," says Post.
There are many potential benefits to customers. "Downspeeding and downsizing result in less fuel burned as well as lower DEF consumption," says Mario Sanchez, Technical Sales Support Director, Cummins Inc. "Because increased fuel economy is synonymous with fewer greenhouse gas emissions, downsped and downsized engines do emit fewer GHGs."
Nowhere is efficiency more important than in the trucking markets where even a very slight gain in fuel economy can yield a tremendous advantage in operating costs. Downsizing and downspeeding have become popular in trucking markets as OEMs and owners strive for the best possible combination of performance, fuel economy and reliability.
"Downsizing in the trucking markets can be seen in two different ways," says Cummins. First, engine manufacturers are working to right size their product offerings. "In Cummins' case, this is evident in the mid-range product range where the ISB6.7 and ISL9 are able to cover the same horsepower range (200 to 380 hp for North American medium-duty trucks) that was previously covered by the ISB6.7, ISC8.3 and ISL9," says Sanchez.
"The second way downsizing has manifested itself in the trucking market is a movement towards smaller displacement engines, typically a 12- to 13-liter engine versus a 15-liter engine" says Sanchez. Often changes to the vehicle also change power requirements. "Improvements to vehicle efficiency, such as reducing aerodynamic drag and rolling resistance and using lighter materials are reducing the mean power required to sustain target speed or average trip time."
Keep in mind that downsizing is not appropriate for every application and there can be trade-offs associated with increased power densities. "This type of downsizing requires careful consideration to ensure that tradeoffs that may be required are acceptable," notes Sanchez.
"Larger displacement engines, like Cummins' ISX15, operate at a lower power density than smaller displacement diesels at the same rated power, offering increased reliability and durability," says Sanchez. "While 12- to 13-liter engines are stretched to their mechanical and thermal limits, larger displacement 15-liter engines have increased capacity and margin relative to cylinder pressure capability and mechanical thermal limits.
"Additionally, lower power density may enable a simpler engine platform or may provide the flexibility to optimize the engine and sub-systems to achieve the best blend of desired performance, fuel economy and emissions characteristics," notes Sanchez. Larger displacement engines offer improved driveability and higher resale value. "A smaller displacement engine may offer a smaller package and a lower weight."
The case for downspeedingThere are a couple of ways to achieve a lower engine speed depending upon the application. "Downspeeding, in the trucking market, refers to gearing the drivetrain to harvest the peak torque diesels provide at lower rpms, allowing the engines to spend more time operating in the load and speed where they yield lower BSFC, thus providing better fuel economy while maintaining safe, driver-pleasing performance," says Sanchez. "As a rule, a 100 rpm reduction equates to a 1% improvement in fuel economy.
"In 2013 Cummins made improvements to its engines, including combustion optimization and refined interaction with the aftertreatment system, that allowed development of engine performance curves (ratings) with improved low-end torque, allowing the engines to reach peak torque at 1,000 rpm (versus 1,200 rpm on the previous models)," notes Sanchez. "These changes enable downspeeding and the associated fuel economy gains."
Many engines are also developing peak torque at lower engine speeds. "Downspeeding of the engine reduces frictional losses, providing an opportunity for overall improved efficiency," says Darrin Treptow, Manager External Engine Applications, John Deere Power Systems. "In addition, vehicles and machines are able to minimize drivetrain parasitic losses by reducing the speed. Downspeeding of the engine and corresponding drivetrain are optimized together to provide the required vehicle performance. In some cases, optimization of the air/fuel systems enables improved lower speed performance."
"It starts with the right size to support increased compression ratios without sacrificing reliability and durability," says Sanchez. "For its heavy-duty on-highway engines, Cummins has optimized combustion and refined engine interaction with aftertreatment systems in order to allow the development of engine ratings that deliver peak torque at 1,100 rpm—100 rpm sooner than previous models.
"Delivering peak torque at lower rpm results in fuel economy gains thanks to reduced friction and increased efficiency of engine breathing and aftertreatment at lower volume flows," says Sanchez. "Our 2013 ISX15 is able to achieve up to 2% better fuel economy and our SmartAdvantage powertrain offers an additional 1% for Cummins 2013 engine models.
"In the off-highway markets, delivering a lower engine speed may suit a specific application in terms of fuel efficiency or achieving noise reduction targets," says Sanchez. "Sophisticated electronic controls associated with Tier 4 allow utilization of torque shaping techniques to reach desired characteristics without impacting machine performance."
But there are potential downsides to downspeeding in certain applications. "Higher operating speeds often result in a wider range of operation for variable speed off-highway equipment," notes Treptow. "In many cases an extended diesel engine speed range can simplify equipment operation. More specifically, a wider speed range can mean less frequent gear changes and overall more flexibility for different applications and operations in any off-road applications."
Off-road downsizingTier 4 has been a key driver to downsizing in the off-road market.
"In the off-road equipment markets, Cummins worked to right size its engine offerings at Tier 4 Interim allowing significant fuel economy improvements and reducing installation space claims, both important benefits as customers became accustomed to aftertreatment technologies," says Sanchez. "For example, the 9-liter Cummins QSL9 engine replaced the 11-liter QSM11 engine used at Tier 3 in several large forklift and reach stacker installations. While power output, engine response and durability remained the same, fuel efficiency increased by about 10%. This was made possible with the use of a variable geometry turbocharger and more capable high pressure common rail (HPCR) fuel system on the QSL9 engine.
"So, for off-road equipment, given appropriate technology and considering application, using a lower displacement engine is possible at the power band overlap area, where the top end of a smaller displacement overlaps with the lower end of a larger displacement engine," says Sanchez. "For Tier 4 Final Cummins expects its four-cylinder QSB4.5 to replace some six-cylinder installations as the power output of the QSB4.5 has increased to 173 hp." The new QSG12 also offers the opportunity to replace some larger displacement heavy-duty engines as it provides a high power density and reaches a top output of 512 hp.
Emission regulations transition points are also driving a trend to downsizing. "Some engine manufacturers have utilized two emissions cut-off points: 49 to 50 hp and 173 to 174 hp to rebalance their product offerings in terms of ratings, occasionally making the cut-off point the maximum hard stop for a specific engine platform," says Sanchez. "This can bring benefits in terms of space claim and reducing cooling demands on the equipment. In fact, using the emissions cut-off points to structure ratings is another example of Tier 4 right sizing. Some applications may be more horsepower than torque focused, OEMs would take that into consideration when making their choice of engine."
Downsizing has happened at some key emission standard cut-off points, for example 75 hp. "Our 850 Series offering ranges from 60 to 120 hp, but below 75 hp the engine does not require selective catalytic reduction (SCR) and diesel exhaust fluid (DEF) system components," says Stephenson. "To meet or exceed our customers' expectations at this power range, we've developed specific torque and power curves to deliver improved driveability and productivity at 74 hp. Our ability to provide a range of options below and above 75 hp allows us to tailor our offering to the customers' needs and specific application, ensuring they have the right solution, whatever their requirements."
Hybridization of equipment can further drive the trend toward downsizing. "Hybridization technology offers more opportunities for vehicles and applications to use downsized engines, as electrification can supplement power requirements," says Post. "Using constant-speed engines in some applications presents opportunities to further optimize engine performance to match the application's system requirements, which in conjunction with the inherent efficiencies of hybrid powertrains, provides increased vehicle efficiency."
"Hybrid installations clearly offer an opportunity for using lower displacement engines, though this must be considered in terms of the application," notes Sanchez. "While using a four-cylinder engine in place of a six-cylinder engine may be feasible in a piece of equipment that has lower load factors like an excavator, the same may not apply to a wheel loader which typically works with higher load factors. In these circumstances, retaining the same size engine would be beneficial though fuel efficiency and lower CO2 emissions would still be achieved."
"Hybridization is one of the many options engine and machine manufacturers are actively exploring," says Stephenson. "In many cases this technology allows an electric motor to offset power losses when selecting a lower-displacement engine. In all cases, we work with our customers to determine the optimum solution for their machine work-cycle needs, which might include a hybrid engine, or start-stop technology, or something else entirely."
Collaborating with the customer to integrate systems that deliver the optimum benefit has become a key focus. "For the past five years we have run Technology Integration Workshops to get customers involved early in the design process, which is an essential approach to ensure we're delivering the best-possible product," says Stephenson.
Machine optimization
There is currently a movement toward total machine optimization.
"We understand that the engine is an important part of maximizing efficiency – but it's not the only part," says Stephenson. "Machine optimization, through improved hydraulics or other design changes, plays a big role too, as does operator training and a host of other factors. These non-engine factors can have as much as a 30% impact on fuel consumption, and part of our work with OEMs is to help understand how our engines fit into the bigger picture.
"We work with each of our customers to deliver the performance they need for their specific work cycles," says Stephenson. "Engine speed is part of this, and we work closely with OEMs to determine the best approach for their individual situation. Often, we can use our engines' electronic control to fine-tune the engine performance and power curves, giving customers the optimum blend of power and fuel economy that will suit their specific needs.
"This work goes much further than just thinking about 'rated speed' as we have to consider the whole work cycle of a machine, where a wide range of optimized engine speeds are required," says Stephenson. "Improved combustion techniques and a range of tailored technologies help us achieve this – which vary depending on engine power."
"Power requirements in the vehicle are determined by vehicle needs," says Treptow. "Vehicle designers and applications are optimizing their powertrain efficiencies to minimize flywheel power while delivering the same performance. Improving drivetrain efficiencies and vehicle controls optimizes engine flywheel power."
The results of what can be achieved in terms of diesel engine efficiency are a moving target. "We continue to invest in research and development of fuel–efficient technologies," says Treptow. "We continue to optimize combustion improvements, friction reduction and engine breathing, with an aspirational goal of 50% brake thermal efficiency."
"The trend to increase power densities will continue," predicts Post. "Technology advancements in materials, fuel/air systems, control strategies and overall optimization of the various systems are key factors in increasing power densities."