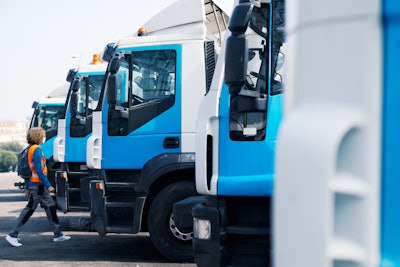
Using hydrogen as a fuel source is not a new concept. In some applications within industrial and processing plants, for example, hydrogen has been used for many years. More recently, hydrogen is gaining traction as a viable fuel solution within the transportation industry, given its many benefits. Yet, with a lot of the standards development work still in progress, there remains some ambiguity around what certifications will be required for hydrogen components and how original equipment manufacturers (OEMs) should design their systems to ensure they are safe, leak-free and efficient.
As more transportation OEMs evaluate a move to hydrogen, knowing the keys to success and what to avoid is crucial. This article focuses on the critical considerations to help ensure your system is designed properly and stays leak-free.
A Brief Background on Hydrogen Fuel Systems
At one time not so long ago, hydrogen was viewed as the way of the future and was expected to dominate many sectors within the transportation industry. That’s because hydrogen offers several benefits over other alternatives. First and foremost, it is a clean, carbon-free fuel whose only by-product is water when used in a fuel cell. In addition, it is highly efficient and can extend vehicle range due to its ability to be compressed at high pressure. But the challenges of working with hydrogen—including leak-free storage, high costs and lack of infrastructure—have previously restricted its growth.
Fast forward to today and we are seeing some positive trends that are changing the landscape and providing a realistic path forward for hydrogen fuel cell vehicles. Suppliers have evolved to eliminate many of the technical constraints and are working to reduce the costs associated with hydrogen systems. In addition, policymakers and regulators are working to help incentivize the ramp-up of a sustainable refueling infrastructure to support the growth of hydrogen vehicles. With these trends, it’s a good time for OEMs to consider how hydrogen could be incorporated into existing products and operations.
Gas Versus Liquid Hydrogen
It's important to note that hydrogen can be stored on a vehicle as a gas or a liquid. For purposes of this article, we are focusing primarily on hydrogen in a gaseous form since a larger share of the market is already working with gaseous hydrogen and the hurdles to adoption are much smaller. While liquid hydrogen can provide a vehicle with a longer range and may prove to be the preferred hydrogen state in the future, it is currently more expensive and harder to handle.
Storage is also an important consideration. Both gaseous and liquid hydrogen require storage in specialized tanks. High-pressure tanks are required for gaseous hydrogen (350 bar to 700 bar for on-vehicle tanks and even higher for refueling station tanks). In contrast, the storage of hydrogen as a liquid requires managing cryogenic temperatures.
While the remainder of this article focuses on gaseous hydrogen, most of the following design considerations are consistent with either media type, and it’s important to make OEMs and end users work with components and suppliers that are aware of the applications differences and requirements.
Importance of Leak-Free Connections in Hydrogen Systems
The nature of the hydrogen molecule itself presents major challenges when specifying components. Hydrogen is small-molecule gas, which can allow it to escape through the narrowest crevices and cracks. Coupled with high-storage pressures, it’s easy to see why ensuring a leak-free seal when connecting components is critical to safety, efficiency, and overall cost of ownership.
Fuel leaks are never good but can be especially costly and dangerous when hydrogen is the fuel source, especially in enclosed areas where the leaked flammable gas can’t dissipate. While many advances in technology have made hydrogen safer to use, there are still many safety criteria to consider when choosing system components.
Therefore, it’s important to work with a supplier that understands the nature of hydrogen and how to design a system that’s safe and efficient. Not all manufacturers have experience working with hydrogen, so be sure to ask about a company’s track record using this volatile fuel source before choosing a supplier.
ORFS fittings, initially developed for the harsh agricultural and construction markets, have been successfully adopted in the alternative fuels market, including hydrogen.Parker Hannifin
Material Compatibility Concerns Limit Product Options
In today’s market, product selection for hydrogen system components can be quite limited. Many of the materials (both metals and elastomers) that would be used in more traditional hydraulic and pneumatic applications are either not compatible with hydrogen or lack the robustness to withstand the required storage pressures.
One of the first major concerns with hydrogen applications is something called hydrogen embrittlement, also known as hydrogen-assisted cracking or hydrogen-induced cracking. This is characterized by a reduction in the ductility of a metal due to absorbed hydrogen. Since hydrogen atoms are small, they are more likely to permeate through solid metals. Once absorbed, hydrogen lowers the stress required for cracks in the metal to initiate and propagate, resulting in embrittlement. Hydrogen embrittlement occurs most notably in steels, as well as in iron, nickel, titanium, cobalt, and their alloys. Even certain grades of stainless steel may not be appropriate for use with hydrogen.
When choosing a metal component for a hydrogen system, it’s important to not only check the grade of the metal, but also know how it is processed and treated (including things like surface finish) and how it will be used throughout the system. A particular grade of stainless steel, for example, may be safely used in areas of the system under low pressure but completely incompatible in those areas under higher pressures.
With regards to elastomers, permeability, temperature and compatibility concerns can also limit their use around hydrogen, especially when used in high-pressure applications. Again, working with a supplier that understands material compatibility and can recommend solutions that are appropriate for a hydrogen system is important.
Special Considerations in Component Design When Working with Hydrogen
While fitting selection seems like a straightforward process, when working with a more challenging media, like hydrogen, more implications exist and more factors must be considered. As previously discussed, material compatibility is the first and most critical consideration. However, there are several other important factors to examine, from assembly, maintenance, and specific application variables (like vibration and envelope space). Vibration, for example, which is prevalent in most modes of transportation, including on- and off-highway vehicles, trains and buses, can cause structural problems within a system and lead to leaks.
After the material compatibility needs have been met, it’s also important to consider various assembly limitations. Many transport vehicles have tight spaces and tight bends which make it difficult to run tube lines or use assembly processes that require greater clearances. When evaluating options, start by asking the following questions:
- How critical is repeatability in the tube fabrication process?
- Is torque a preferred method of assembly?
- How important is it to be able to maintain the system later in its life and replace system components, such as valves, filters and manifolds?
When it comes to fittings, the decision typically comes down to using a compression fitting or an O-ring face seal (ORFS) fitting. Compression fittings are an older technology and have been successfully used in many applications using hydrogen, typically in larger scale industrial settings like processing plants. ORFS fittings, initially developed for the harsh agricultural and construction markets, have been successfully adopted in the alternative fuels market (such as compressed natural gas, liquified natural gas or hydrogen) during the past few decades because of several unique design features that make them especially attractive in the transportation industry.
By introducing an elastomeric seal into the fitting design, ORFS fittings are more robust and leak-free at higher pressures, have improved performance in high-vibration applications, and can be easily maintained due to the replaceable O-rings. From an assembly perspective, an ORFS has many advantages.
First, the geometry of the ORFS fitting allows for a zero-clearance fit, which makes plumbing and installing in tight spaces a simpler process. Second, these fittings can be assembled using torque, which allows for repeatability across various technicians, as well as process consistency whether original makeup or part of a replacement. Lastly, the flat face of the connection means that over torqueing (and potentially damaging the tube line) is virtually impossible because the fittings can withstand up to 200% rated torque values. All this adds up to lower costs at time of installation and easier maintenance and, most importantly, fewer potential leak paths across the tube connections.
Today, a variety of ORFS fittings are available, each with its own attributes. However, not all are created equal, and not all are suitable for hydrogen use. Parker’s Seal-Lok O-Ring Face Seal fitting, for example, features a unique design that provides leak-free connections in applications with high pressures, high vibration and impulse environments and is also suitable for use with hydrogen. Its hydrogen-rated elastomeric seal eliminates the need for metal-to-metal sealing, and its zero-clearance fit facilitates plumbing. It is also resistant to over torque and damage from over tightening, and its flat face allows for the unlimited ability to remake tube assemblies. In addition, its innovative captive O-ring groove creates a dove-tail lip which helps with seal retention by helping to keep the seal in place during shipping and assembly.
As important as the fittings are, they are not the only components that deserve special consideration when using hydrogen. Material compatibility and product features must be considered when choosing valves, regulators and filters. Thinking about the entire system and how the components fit together is important. It’s equally important to choose a supplier that offers a full suite of hydrogen-certified products (pre- and post-regulator) that can simplify the design process, provide additional value to the end user and ensure the safe conveyance of hydrogen fuel.
Conclusion
Any component can become the weak link in a fuel system and create leaks, especially when using a small molecule media like hydrogen. So, be sure to carefully evaluate every component in the hydrogen system for compatibility and confirm that it can handle the pressures the components will experience throughout the system.
Using a systems approach, with trusted suppliers that understand the challenges and needs of hydrogen systems, can ensure that OEMs specify hydrogen-approved components and that they are right-sized for their area of the fuel system. This way the right components for the application are chosen and placed where they are needed to design a leak-free hydrogen system.
Cody Yarletts is a business development manager with Parker, and Nathan Green is an applications engineer with Parker.