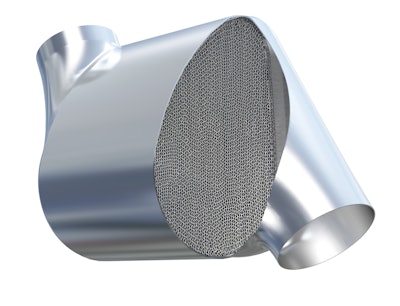
Power transmission belts, catalytic converters, vibration control elements and hoses for enhanced safety and reliability during daily field operations, more efficient use and therefore lower consumption and emissions: Continental offers agricultural machine manufacturers comprehensive one-stop custom solutions in engines. This opens up a range of benefits – from purchasing to development through to series production. For instance, it is significantly easier to match components to each other. Customers benefit from that by involving Continental in the development process from the very start to make optimal use of the engine compartment.
Rigorous lightweight construction Conti Excelsus
For harvesting and sowing machines in particular, lightweight construction is becoming increasingly important. Lower vehicle weight is important, for example, for field operations in order to reduce the pressure on the soil and thus to minimize soil compaction. The weight is also relevant when it comes to approval for road use, especially for large machines. In addition, greater payloads are possible if the weight of the machine itself is reduced. Thanks to its lightweight construction, the Conti Excelsus, for instance, delivers a significant weight advantage over the PTFE pipes enclosed in a stainless-steel braid used up till now. Polyamide cooling water lines also contribute to weight savings. In addition, they enable assembly-friendly processes with tight bending radii.
Continental has also developed lightweight engine mount prototypes made of glass-fiber-reinforced polyamide. The prototype bracket for a tractor engine mount is 40% lighter than the original steel component.
Near-engine catalytic converters: innovative folding technology enables space-saving designs
Near-engine catalytic converters heat up faster than those installed further from the engine. In addition, they can also often be produced at lower cost since they have a smaller volume and need correspondingly less precious metal. Despite the smaller volume, however, vehicle manufacturers still find themselves faced with the problem of the tight package space around the engine. In response to that, the non-circular or even asymmetrically shaped catalytic converters developed by Continental help make optimal use of the space between the engine block and various adjacent ancillary components.
The introduction of an innovative folding technology enables Continental to fold the metal foils onto each other inside the catalytic converter – instead of winding them as hitherto – such that completely new shapes can be produced, e.g. a kidney shape. Especially in applications in the off-highway sector, in which small numbers of an engine family are fitted in each of various vehicles, such as tractors and front loaders, an optimized, uniform catalytic converter design enables the vehicle manufacturers to save costs.
For extreme conditions
In the Unipower Tough Grip, Continental has a multi V-belt with a fabric cover in its range for off-highway applications. It reliably drives Unipower Tough Grip
Greater operational safety
Fuel lines with an electrically conductive inner lining have been fitted as standard in passenger cars for some time. Now this application – not least because of relevant requirements in the U.S. in particular – is also becoming increasingly attractive for industrial trucks. The conductive inner lining made of FPM (fluorocarbon rubber) prevents static buildup at high throughflow rates which, in the worst-case scenario, could result in sparking and spontaneous ignition of the vehicle. Continental’s highly flexible fuel lines are suitable for gasoline, diesel and biodiesel and can withstand continuous operating temperatures from -40-160 C. In addition, Continental also has a conductive polyamide solution available for this application.
Apart from flexible and dimensionally stable oil lines, Continental also has the Conti Excelsus externally reinforced hose in its range for high temperatures in agricultural machines. This feeds cooling water and lubricant to turbochargers and is used in their control systems, too It is also suitable for transporting air, for instance in exhaust systems, or as a fuel return line. Its special braid made of highly temperature- and chemical-resistant synthetic fabric makes the hose extremely flexible and enables it to be used in particularly tight, complex package spaces.
Effective vibration control
Hydraulic resistance increases the damping effect of vibration control elements. Continental uses this effect in bushings and mounts with an integrated fluid system. These hydro bushings can be used in agricultural machines as engine and cab mounts, for example. Continental’s hydro bushing withstands loads of 1,230-3,000 N and offers an impressively long service life. Unlike classic mounts, it can be rotated about its center axis, simplifying maintenance work on the vehicles as a result.