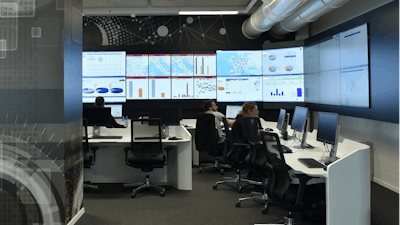
At its Tech Day 2018, FPT Industrial presented its vision of 4.0 Powertrain Technologies and, with the presence of international scientists and experts in the fields of innovation and digitalization, discussed with participants the technologies that are changing the world – one of them being the connected engine.
Leading in innovation, FPT Industrial showcased the Control Room, a dedicated location in Turin for data analysis to improve remote customer support for connected engines. Based on FPT Industrial’s telematics solution, a trained team controls and monitors data received from engines all over the world and, to deliver added value, promotes proactive maintenance and assistance.
In the past, fault management was carried out through component analysis only after an issue occurred. Today, connected engines enable remote monitoring and diagnosis, making equipment tracking easier and more effective whilst allowing engine maintenance to be better managed, thereby preventing possible issues. Dealers and OEMs can also provide faster service and support to their customers, reducing downtime for end users. In the Control Room, every detail is taken care of through a health monitoring service.
The FPT Industrial telematics kit is easily installable and collects data via the existing vehicular diagnostic ports, sending all information via GSM to a centralized cloud storage. The GSM connection allows users to receive and monitor engine parameters and alerts.
End users can access a mobile app with a user-friendly dashboard that shows key engine parameters, such as load, fluid levels and working hours, the machine’s GPS position and service reminders. Consequently, maintenance intervals can be scheduled and potential assistance needs can be detected early, optimizing uptime.
FPT Industrial has developed a web portal dedicated to fleet owners, dealers and OEMs, providing further information about the fleet. In addition to a comprehensive set of engine parameters, service reminders (both maintenance alerts and fault codes) and GPS positions are used by the portal to present a complete overview of each equipment’s mission and engine usage. OEMs, dealers and fleet owners can follow up specific requirements with tailored actions. Fleet monitoring enables advanced service and care, improving fleet management efficiency with a positive impact on overall Total Cost of Ownership (TCO).
The FPT Industrial telematics offering also guarantees that customers master the solution to take advantage of its full capabilities. Additionally, customers can rely on FPT Industrial Customer Care Service, open 24 hours a day, 365 days a year, supporting dealers, service points, OEMs and end-users worldwide.