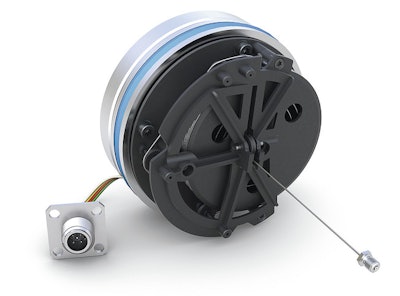
Rota Engineering’s position sensors for hydraulic cylinders now include field calibration, allowing end users to override the factory calibration and select any portion of the active stroke zone to output a full scale signal to achieve maximum resolution (learn more, 20842242).Rota Engineering Ltd.
And the sensors themselves are increasingly getting smarter in order to provide more information and capabilities. According to the IEEE—a technical professional organization dedicated to advancing technology for the benefit of humanity—1451.2 standard, these so-called smart sensors are ones “which provide functions beyond those for generating a correct representation of a sensed or controlled quality. This function typically simplifies the integration of the transducer into applications in a networked environment.”
Smart sensor technology has existed in one form or another since the early 1960s. Today, 90% of all sensors are considered “smart” in that they include some form of signal conditioning, said Roger Grace, President of Roger Grace Associates, at a recent Fluid Power Industrial Consortium (FPIC) seminar (see sidebar, below). This is according to a survey Grace conducted of industry professionals to gauge what most consider to be the definition of a smart sensor.
“To be smart, in my opinion, we need to integrate functionalities,” he said. “Smart is all about enhancing the ability of the sensor to do its job…. The degree to which it’s done is where the difference of opinion lies.”
In general, he said it’s about making a decision. With so much data available today due to the increased integration of sensors and other data collection componentry, a technology or system’s ability to communicate the information collected is key. “You can’t operate on data, you have to process the data, use various algorithms to get the information you need to be able to perform an action,” Grace said. “And that’s a key element of a smart sensor, to be able to provide you with a signal or information to make a decision, or make a decision on its [the sensor] own by use of a closed loop control system.”
The internet of things (IoT), Industry 4.0 and other market trends are all helping to increase the use of smart sensors. Grace said that based on analysis of several market research studies, the smart sensor market is anticipated to grow at a CAGR (compound annual growth rate) of 16-21% from 2015-2024.
Applications in fluid power
In February, Frost & Sullivan released a new report saying smart sensor-embedded hydraulic systems which are industrial internet of things (IIoT) enabled will be a key driver for the hydraulic equipment market. "Key mobile hydraulic equipment market participants…are venturing into smart platforms…embedding sensors in pumps, cylinders and even accessories such as hoses to enhance power density and control oil leakage from equipment," said Frost & Sullivan Industrial Automation and Process Research Analyst Kiravani Emani in a press release announcing the new report. "Electronic integration will continue to play a pivotal role in boosting demand for hydraulic products."
Because of the importance electronics will play in further enhancing the fluid power industry, several manufacturers have introduced technology specifically designed for integration into hydraulic components.
SIKO's SGH line of wire-actuated encoders easily integrate into hydraulic cylinders without the need to hollow bore the piston.SIKO GmbH
For instance, in December SIKO released its SGH50 position sensor for use in hydraulic and telescopic cylinders. A cable mechanism in the sensor allows measurements up to 5 m (16.4 ft.) and enables communication with machine systems via CANopen or SAE J1939 protocols. This capability allows engineers to build information collection into their fluid power systems which will aid overall machine operation. Read more about similar sensor technologies for fluid power applications in the article “New Sensor Designs Aid Creation of Smart Hydraulics.”
At Agritechnica 2017, Poclain Hydraulics Inc. introduced its PMe pump featuring a set of integrated sensors and embedded electronic control unit (ECU) known as the SmartDrive CT 30. The PMe is available with electro-proportional servo control with or without mechanical feedback, depending on the degree of accuracy requested. Using a factory pre-set calibration, the pump’s electronics are able to provide accurate pump control, helping to increase system efficiency. In addition, the pump can provide the sensors’ physical and electrical values—such as temperature, pressure and speed—via CANbus to a master ECU for further data collection and efficiency potential.
To support the growing Industry 4.0 trend, Parker Hannifin introduced its P8S CPS Series of smart sensors for pneumatic cylinders in February. The company says the sensors feature intelligent functionality such as the ability to acquire and locally process information and communicate with upper level controllers and/or local networks. Continuous transfer of position data makes pneumatic cylinders and drives more intelligent and versatile. Doing so can help solve various engineering challenges such as quality monitoring and process control (see sidebar below). When integrated onto a pnuematic cylinder, the P8S sensor provides continuous transfer of position data.Parker Hannifin
The ability of a sensor to communicate with a network is an integral part of ensuring it is a smart component. “Without networking, [you] don’t have an optimal product,” said Grace. This aids both data collection and analysis, and when necessary action to be taken either by the sensor itself or another part of the system or machine into which it's integrated.
From the survey he conducted of industry professionals, Grace determined there are four levels of sensor technology.
He said most sensors today include a sensor interface chip, and are the most popular sensor design concept. However, according to his survey, most respondents agreed the addition of a microcontroller, Level 3 sensors, is where component intelligence begins. “Because without the microcontroller you can’t make decisions,” he explained, which is the aspect the makes a sensor or system smart.
When integrating smart sensors or other electronics into a fluid power system—or any system for that matter—packaging is critical. These components typically have very sensitive parts which must be protected, especially in fluid power applications where there are high pressures and temperatures that could negatively impact the results of the data being collected.
For its SGH50 sensor, SIKO developed a special plastic to extend the sensor’s fluid temperature resistance from 85-105 C (185-221 F). In addition, the sensor is designed to withstand shocks 100 times the force of gravity. It’s able to do so in part because the flexible cable of the sensor completely absorbs vibrations. The hydraulic medium also helps to dampen any vibrations.
Gary Winzeler, VP Sales & Marketing at DunAn Sensing, spoke during the FPIC seminar about the company using its DURAsense packaging for the company’s new TP Series pressure and temperature sensors (see sidebar below). DURAsense—a term coined by DunAn Sensing—refers to the way the company packages its products so they provide accuracy, reliability and affordability. “If we lose any one of these points, we feel it’s not going to be a fulfilling product for the customer,” he said.
This technique was implemented through the packaging of the microelectromechancial systems (MEMS) technology in the sensor. He said that today most companies will use a stainless steel diaphragm and oil-fill to protect the MEMS, especially if it’s going to be used in harsh operating conditions. While this is a good technique and works to protect the product, there is some loss of accuracy and sensitivity. It also drives up the cost of the sensor. The Poclain PMe pump features a set of integrated sensors and embedded ECU.Poclain Hydraulics Inc.
Instead, DunAn utilized a rear-entry packaging strategy for media contact with the silicon sensor which eliminates the contact of bond wires and electrical signals to the media, enhancing reliability and operation in conductive environments.
In addition to protecting a device, packaging of multiple features or functionalities is also an important aspect when developing or implementing smart sensors. DunAn’s TP Series for instance, is considered a smart sensor because it includes both temperature and pressure sensing in a single device. Products such as this allow designers to increase the amount of information they can extract while reducing installation space and costs.
These types of smart sensors will be an integral part of developing more fully integrated systems. “People don’t want to create their own solutions, they want to go to somebody that has it all wrapped up,” said Grace. “Go[ing] to one source that knows the whole process and delivers the solution, that’s where the market is going.”
As the fluid power and other industries look to further enhance and differentiate their offerings, smart sensors will provide a means of creating more intelligent products and systems.