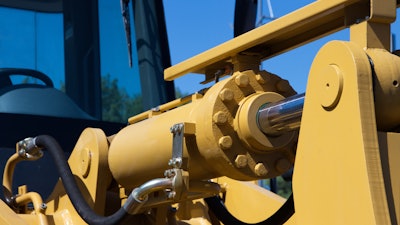
This is both a simple and deceptively dense question for production managers and maintenance personnel. Without any operating or performance data, the answer to this question remains straightforward; they’re either working or they’re not. But we know that there is a large chasm of performance between “working” and “not working.”
Historically, we would pull out a piece of paper or go to a spreadsheet and run efficiency calculations to determine how much work and how much waste we’re seeing. Consider then also the drive for better efficiencies across not only our pumps, but also our overall equipment effectiveness across entire fluid power systems that we know work and waste is everywhere. To date, this has placed a hefty time tax on how much effort we spend chasing down this information. We now understand how deceptively dense the “how are your pumps?” question truly is.
With the advent of the Digital Age and the Industrial Internet of Things (IIoT), can we answer the pump question more confidently than ever? Can we introduce a new way to master fluid power efficiency and “erase the waste?” The easy answer is yes.
Mastering fluid power efficiency in the age of IIoT requires alignment in believing that efficiencies are amplified by the sum of their parts – every time new insights and information are layered upon existing information, the picture of efficiency gains higher resolution. The real value of IIoT, however, is in how quickly, safely, and predictably we can obtain that information, and then how we use it! We can reliably use that data to build real-time efficiency models that are constantly running in the background. If we tie that back to work and waste from a time management standpoint, glancing at a dashboard to see a real-time efficiency metric is about as efficient as it gets.
Peak efficiency is gained by not just knowing the performance characteristics of one component, but how that component works in an entire fluid power ecosystem. While seeing a standalone case pressure reading in real-time from a pump can be helpful, when that is layered with a real-time flow reading, the information has more context. Should you then also have real-time fluid characteristics being monitored like contamination, your overall insights gain more credibility. Layer on real-time filtration monitoring and you have a digital fluid power efficiency hub at your fingertips. I’ll walk through each of these pieces of the ecosystem in more detail.
Pump Efficiency Monitoring Using Industrial IoT
Traditionally, if you wanted to see how a pump is working or not, you would grab a bucket, a hose and a stopwatch. This was one way to check flow rates and overall efficiency. There is an opportunity to get beyond that world and have a more harmonious, connected interface. Imagine now that instead of just a traditional pump, you have a smart pump or a smart device connected to a pump. That smart device is generating information for you in real time about that pump, down to the pump's volumetric efficiency (VE). The manufacturer recommends that at any given time, you should be at an 85% VE or higher coming out of the case drain but suddenly, one of your pumps starts to trend at a 78% VE out of a case drain. So now, you're operating at seven points below what the manufacturer recommends. With today's IIoT, you're going to get an alarm or a notification about that.
Now that you understand that it's operating below efficiency, you've got to start thinking about some decisions that you need to make. Are you still satisfied with the level of production? You can start to change production decisions in real time. But you have this piece of information here now, and what do you do with it?
What's really important to take away from this is how you use the data. You could start asking many questions about your oil condition and take action to clean and filter the oil. Then you can start making operational decisions for your production. You can then look across the entire manufacturing plant or plants to see if this same product is having the same 78% VE — determine if it’s plant-wide or fleet wide. Now you've gone from an asset specific, to a systemic look at the pump and its fluid quality. You can use this data globally if you have fleets or plants all over the world, instead of individuals in each plant monitoring and gathering and sharing data. This can be used to now make company-wide decisions. All this started from a singular piece of efficiency data at this point. And then we ultimately get to the very top of the pyramid, which gets us to an interesting piece of monetization as well. Because inside the organization may not be the only people that care or want to see that data. What if it's actually the pump itself? Shouldn't the OEM of that pump know that it's just not quite working as it should be in the application environment that it's in?
Association of Equipment Manufacturers
What we see with the IoT is the more that we generate that information back to the OEMs, they can continue to engineer out why this stuff fails in the first place. Because engineers can’t get out into the field and understand how equipment works in the highly varied environments of traditional off-highway or factory floor level machines, generating post installation information back to them allows them to make the smarter design decisions around how their products work.
Establishing Real Filtration Efficiency
Hydraulic filtration preventative maintenance is usually based on a schedule or based on the pop-up indicators that tell you a filter is nearing the end of its life — that as the element continues to collect dirt and water particles, it gets less and less effective and then it ceases to be effective before you need to go into bypass. In this case, the filters could have been used past their effectiveness, thus reducing efficiency. Or, all filters are simply changed out on a schedule, so you're going to have filters that probably didn't need to be replaced and you’re wasting money.
What if your filter was actually able to tell you at the exact moment, or maybe 10 or 5% before it reached peak efficiency? If you use smart filtration, you will be replacing the filter at the right time, every time. This has generated at least 33% cost savings for organizations that are deploying system-wide filtration management with the IoT.
What Is Lubrication Efficiency?
Up next is lubrication, is your fluid working for you as well as it should? There are always opportunities to gain more information around your fluid health. You may take a fluid sample or a color patch test and send it to a lab, and a report is generated. Testing and labs are important pieces of the lubrication management puzzle. But the problem is you can't just look at one piece of that fluid. The baseline for hydraulic fluid is that it should be clean, cool and dry.
You can keep contaminants out, keep water out, and keep your fluid at the right temperature. But depending on what industry you're in, you may need to understand more about your additive packages, metal ingress, fluid oxidation, etc. Here, viscosity index is not the only answer. It’s important to consider all factors when trying to achieve lubrication efficiency.
This is why the narrative starts to change when you have more efficient data coming in and you have a bigger, better, broader picture on how to manage your equipment, fleet, factory, floor, whatever it may be. Backing out to this narrative allows you to question your system reliability, preventative maintenance plans, lubrication management, vibration monitoring and even the commodities you use. Stack those on top of each other and you start to get more and more insightful information. Jeremy Drury has deployed successful, connected fluid-power and IIoT solutions into the global marketplace.Association of Equipment Manufacturers
*This article was written by Jeremy Drury on behalf of the Association of Equipment Manufacturers (AEM).
Jeremy Drury is "Connecting Prediction to Production" with the Industrial Internet of Things (IIoT). With his ability to connect vision and strategy to field-level operations, he has deployed successful, connected fluid-power and IIoT solutions into the global marketplace, and has been a featured keynote speaker at the National Fluid Power Association's Annual Conferences, as well as the Reliable Plant Conference, Machinery Lubrication Conference, Sensors Expo, Sensors Midwest, and TechSolve's annual production/solution showcase.
Drury presented the education session Mastering Fluid Power Efficiency with IoT at IFPE 2020, held in conjunction with AEM-produced CONEXPO-CON/AGG 2020.