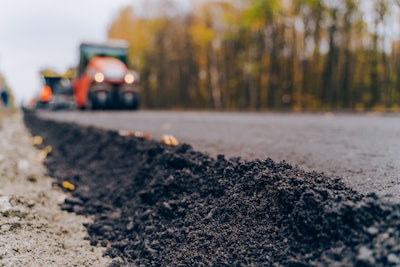
The off-highway sector is just beginning its journey toward decarbonization, with electric powertrains a major focus for smaller machines, while larger off-highway equipment is likely to leverage renewable or biofuels. While some of the industry’s smaller tools are well suited to electrification, there are numerous obstacles to overcome if it is to make significant progress, such as achieving production scale, advancing battery technologies, and installing charging infrastructure.
This article is based on a recent study by Roland Berger, and synthesizes off-highway industry views on decarbonization from across the globe, as well as identifies specific types of machinery and regions on which to focus sustainability efforts. Reducing emissions in the off-highway sector won’t be easy, but targeting these areas could yield the most impactful results.
Off-Highway Decarbonization: The Global Picture
While the drive toward e-mobility in on-highway transport has been underway for some time, the off-highway industry is just beginning its decarbonization journey. There are three main reasons for this shift in the off-highway sector.
First, key players across the off-highway value chain are now committing to improve environmental sustainability (Figure 1). From suppliers to OEMs to end-users, some of the industry’s biggest companies have pledged to significantly reduce emissions, or in some cases reach net zero by 2040 or 2050.
Figure 1. Key players across the off-highway value chain are now committing to improve environmental sustainabilityRoland Berger
Figure 2. Governments are introducing regulations at local and federal levels to limit pollution and greenhouse gas emissions from off-highway equipmentRoland Berger
Figure 3. Total cost of ownership benefits of off-highway electric equipmentRoland Berger
Agriculture equipment, on the contrary, with its high range and charging requirements, poses more challenges for electrification. Nevertheless, early models of electric tractors with 75 horsepower motors and operating times of up to four hours have been developed. These tractors can fulfill many routine farming tasks, with a fast charge at lunchtime enabling a full day of use.
With regard to mining, electric trucks can deliver substantial benefits to underground mining operations, but for open-cast mining the benefits are harder to realize, given the larger scale of vehicles. This requires either large onboard batteries and charging infrastructure or pantographic systems and trolley infrastructure, both of which can be costly. Despite the challenges, mining operators are exploring ways to optimize fully electric dump truck operations for both cost and sustainability benefits.
Promising use cases notwithstanding, there are still numerous hurdles to mass adoption of electric off-highway equipment, particularly with batteries and charging infrastructure. Addressing these challenges and finding innovative solutions will be crucial for achieving significant decarbonization in the off-highway sector (Figure 4).
Figure 4. Off-highway equipment requires innovative solutions, which will be crucial for achieving significant decarbonizationRoland Berger
Survey Findings
To gain more insights into the decarbonization trends and challenges in the off-highway sector, Roland Berger conducted a global survey of OEMs, suppliers and distributors within the industry.
The survey results revealed that more than 70% of respondents believe sustainability and sustainable powertrains are highly relevant to their industry, and that more than 60% of them are spending at least 20% of their R&D budget on sustainability activities. In terms of powertrain technologies, the current focus is on battery electric, followed by renewable diesel and hydrogen technologies.
The survey also asked participants about the size of equipment they expect alternative powertrains to be used in. Two thirds said compact equipment is likely to be fitted with battery electric systems, with a third saying the same for medium equipment. For large equipment (20-plus tons’ operating weight), only 16% of industry participants believe it will be possible to achieve profitable operations.
Battery electric powertrains are seen favorably in terms of operability and reliability. From a TCO perspective, renewable diesel is seen as the clear front runner, followed by battery electric vehicles. Fuel cell and hydrogen combustion aren’t viewed as positively due to the high cost of hydrogen. There are also concerns with fuel cells’ specific cooling requirements as well as being able to perform under operating conditions with high vibration and heavy dust.
Cost is just one of several challenges in the energy transition. Participants see vehicle acquisition costs, the availability of public charging and refueling infrastructure, and system integration challenges as the top three concerns.
Beyond the challenges mentioned in the chart (Figure 5), industry participants also feel that fundamental changes in their business models are necessary to successfully transition to a decarbonized future. A lack of key skills within their organizations poses a further obstacle.
Figure 5. Trends and challenges in decarbonization in the off-highway sectorRoland Berger
Measuring Environmental Impact
The carbon footprint of construction equipment includes manufacturing, transportation, operation and end-of-life disposal. In the context of alternative energy, the primary objective is to reduce carbon emissions due to operation by replacing the traditional diesel engine with a lower- or zero-emission alternative as more than 90% of all Scope 3 emissions are determined by vehicle emissions. Alternative energy can also be used during manufacturing and transportation to reduce life cycle emissions.
To date, the industry has concentrated on the easiest wins — developing battery electric versions of the smallest machine types or tethered electric versions of machines where mobility is not required. There is, of course, value in moving any machine away from fossil fuels, but to successfully decarbonize, the off-highway industry must focus its efforts on the machines and markets that emit the most CO2.
To gain a clearer picture of carbon footprints, the study estimated the regional and global fleet sizes, installed engine power and annual utilization of 16 mainstream equipment types. Using this method we calculated the total installed power of global construction equipment to be 837 gigawatts across 9.88 million active machines, and the total annual power usage of the global construction equipment fleet to be 1,400 terawatt-hours. .
The study found that emerging markets (Figure 6), such as China, India and the rest of the world, account for 65% of the global fleet's installed engine power and 84% of its carbon emissions, due to their larger machine sizes and higher utilization rates.
Figure 6.Roland Berger
The study also identified the equipment types that have the most impact on carbon emissions in Europe (Figure 7). Crawler excavators and wheeled loaders, which are sold in large numbers and have medium to large engine sizes, account for 62% of the European fleet's installed engine power and annual energy usage. However, mini-excavators, which are expected to see highest penetration of zero emission vehicles, represent only 4%.
Figure 7. Equipment types that have the most impact on carbon emissions in EuropeRoland Berger
Conclusion
While not an absolute measure of carbon emissions, this study yields a clear conclusion: If the off-highway sector is to seriously reduce carbon emissions, it must focus on decarbonizing crawler excavators and wheeled loaders. Implementing changes in emerging markets will have a bigger impact than in developed markets.
This presents a number of hurdles. Wheeled loaders and medium and large excavators have much higher power requirements than compact machines, making them harder to convert to alternative energy. For battery-powered machines, this is due to the high initial cost of the batteries which, can be uneconomical; for hydrogen-powered machines, there can be a lack of hydrogen supply to meet requirements in addition to cost constraints. A credible alternative seems to lie in renewable diesel or renewable natural gas, however, adequate availability of these fuels needs to be ensured.
Furthermore, encouraging change in emerging markets may be harder than in developed countries. History shows that these countries tend to follow rather than lead on environmental legislation. There’s also a cost factor: Alternatively powered machines are currently more expensive than traditional diesel equipment, posing a further challenge to poorer countries. Lastly, construction equipment has a long lifespan. Without powerful incentives to scrap them, it will take decades to phase out diesel-powered machines unless cost-efficient retrofit solutions can be developed.
Wilfried Aulbur is senior partner at Roland Berger. Giovanni Schelfi is partner at Roland Berger.