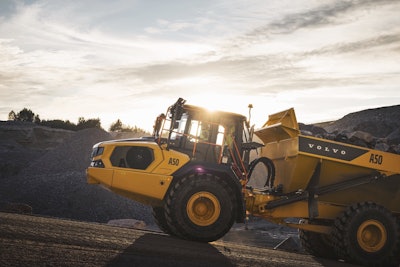
Volvo Construction Equipment's (Volvo CE) lineup of articulated haulers include significant updates to the 28- to 61-ton articulated dump trucks and a new size class with the 50-ton A50. Designed to meet customers’ evolving needs, this launch marks the latest makeover of a Volvo CE product line, following the introduction of the company’s new-generation excavators in 2024. Updates include improved fuel efficiency, a redesigned cab with a host of new features, enhanced safety, simpler maintenance and more, making them suitable for demanding projects in quarrying, mining, construction and more.
“Articulated haulers handle some of the toughest tasks in the most challenging terrain,” said Tyler Smith, product manager — articulated haulers in a press release. “We took customer feedback and completely redesigned what was already the world's best articulated hauler lineup. These new Volvo haul trucks are built to be the workhorses customers need to get their toughest jobs done on time and on budget.”
The A50 delivers 10% more productivity and 8% greater fuel efficiency compared to the previous generation’s A45G FS. It also features improved full-suspension technology for faster travel speed and a smoother ride.
It also boasts faster cycle times and efficiency over its competitors and fills a need in the market with its 50-ton capacity, innovative technology, unmatched power and modern design.
An electronic system and a new Volvo-developed transmission help reduce fuel usage across the product range. The series also is designed so the haulers can be adapted for future drivetrain technologies.
The Volvo drivetrain with Terrain Memory ensures fuel efficiency without compromising power, thanks to its ability to identify and remember slippery road segments. Automatic drive, 100% differential locks and all-terrain bogie, and hydro-mechanical steering work together to provide traction, stability and precise control.
Volvo Dynamic Drive offers predictive gear selection that adapts to operating conditions, and a downhill speed control function relies on Volvo’s industry-leading braking systems to further enhance efficiency, safety and comfort.
Additionally, the frame and body design provide market-leading tipping clearance and material flow when dumping, minimizing the need for support equipment on the jobsite. Further improvements include an optional overhung tailgate with longer arms for a quicker and wider opening when dumping.
The redesigned cab includes a larger floor area, new hanging pedals and steering wheel, a heated or cooled storage box for food and drink, an adjustable seat, Bluetooth connectivity, USB ports for charging devices, ergonomic levers and switch layouts, and better noise reduction.
A lower hood profile, reconfigured and larger window panels, additional LED lighting and wider windshield wiper coverage result in a field of vision that exceeds industry standards. Optional front and rear cameras and a standard entrance camera — all of which are managed via the Volvo Co-Pilot — further enhance visibility.
Entering and exiting the hauler cab is simpler and safer with a repositioned door, railings on both sides and focused lighting on the stairs and platform.
A startup button is now found at ground level, illuminating the stairs and booting up controls. Once in the cab, the operator turns the key to fully start the machine. At the end of the day, the switch does not need to be turned off — the key alone takes care of shutdown.
Volvo’s updated articulated dump truck range also is engineered for durability with reinforced axles that are capable of withstanding heavier loads and higher torque. Safety is also prioritized with new harness anchor points in the cab that meet OSHA and WorkSafeBC regulations.
Smarter solutions for intuitive operation
Already considered many operators’ haul trucks of choice, Volvo’s updated models make it even easier for them to stay in-the-know with two in-cab screens that display essential information.
The updated interactive Volvo Co-Pilot display offers easy control of functions like media, camera settings, climate control and machine status. A dynamic instrument cluster positioned in front of the steering wheel provides important vehicle data at a glance.
Technology like Haul Assist with on-board weighing takes productivity to another level by providing real-time payload data to prevent overloading and minimize carry back, which also reduces fuel consumption and machine wear.
Traffic flow, vehicle performance and on-site logistics can be improved with the use of digital tools like Connected Map, Performance Indicator and Site Optimization. The ActiveCare Direct™ telematics system supports machine uptime and reduces repair costs.
These updated haulers are future-ready thanks to a new software architecture that allows customers to incorporate future upgrades and smart solutions, ensuring their equipment stays current with cutting-edge technology.