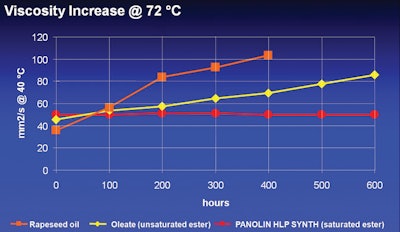
“Going green.” It’s not a trend. It’s a new way of doing business. Over the past several years, regulations have been passed globally requiring companies working on or near waterways to respect the wildlife who call their jobsite home. For manufacturers and operators of cranes, excavators and other mobile equipment, these restrictions are becoming increasingly important.
In terms of hydraulic systems, manufacturing has historically considered mineral oil to be a commodity. Fill the system, use the fluid, and throw it out. Rinse and repeat. Yet in an effort to meet regulations and gain contracts from green-minded clients, manufacturers are being forced to use biofluids that are significantly more expensive with little understanding about the differences in fluid types. Those differences mean everything when it comes to performance.
Standards for Biodegradability & Toxicity
To comply with environmental policies, biofluids need to meet standards for both biodegradability and toxicity. However, many fluid manufacturers have muddied these standards in such a way that biofluid users don’t always understand what they are buying.
Biodegradability can generally be broken down into two classifications – inherently biodegradable and readily biodegradable. All fluids are biodegradable (and so are you and I, as a matter of fact), meaning they break down within some undefined span of time. According to the U.S. Army Corps of Engineers, a hydraulic fluid is classified as readily biodegradable when 60% or more of the material is decomposed in 28 days.1 When selecting a biofluid for use in an environmentally sensitive application, you should select a fluid that is readily biodegradable.
Simply because a fluid is biodegradable does not also necessarily indicate that it is non-toxic. According to that same classification, a hydraulic fluid is considered non-toxic if a specific ratio of the hydraulic fluid to water is used and less than 50% of the test organisms die within 96 hours.1 Again, you will want to check the toxicity of a biofluid before selecting it for an application.
Biofluid Classifications
There are four major classifications of biofluids, each with their own distinctive characteristics and useful when given specific application requirements. It is imperative when selecting a biofluid that you understand the performance, temperature and longevity requirements of your system prior to making a selection.
- HEPG (Polyglycols): These fluids may be water or oil based. They are very popular in applications where fire resistance is required, but those which are water based should be used with caution as they may not offer the same lubricity as an oil-based product.
- HETG (Triglycerides): HETG’s are plant or animal based oils such as vegetable oil, rapeseed oil or sunflower oil. Many of these fluids do not perform well under high heat conditions, as the oil itself will begin to cook and therefore change its chemical composition. They do offer excellent biodegradability and rust prevention, but you must be cautious when using HETG fluids in high-heat applications.
- HEPR (Polyalphaoelfins): Only a very limited range of PAO base fluids are readily biodegradable. These formulating restrictions lead to limited shear stability of the hydraulic fluid, meaning the viscosity may be progressively lost as it is run through a system.
- HEES (Synthetic Esters): Synthetic esters have good biodegradability, but their performance can vary greatly dependent upon the ester type and base fluid used. Synthetic esters can be broken up into two categories – saturated esters and unsaturated esters.
Saturated vs. Unsaturated Synthetic Ester Fluids
It is unfortunate that many fluid manufacturers group unsaturated and saturated synthetic fluids together, just calling them ‘synthetic esters’ despite the major performance and longevity differences between the two types. The saturation of a fluid is based upon the chemical bonds within the fluid itself.
Oxidation, or ageing of a fluid, occurs when a fluid reacts with oxygen. The result of this oxidation is an extreme thickening and gumming of the fluid which can lead to catastrophic system failures. Unsaturated esters have many open bonds which will react with oxygen, causing the fluid to age rapidly. Saturated esters, however, have significantly fewer bonds and therefore do not oxidize rapidly and will last significantly longer in high-heat, intense applications. (See Graph 1)
The simplest way to determine whether a product is saturated or unsaturated is to ask the fluid manufacturer for the Iodine number. This number identifies the number of open bonds available, thus the higher the Iodine number, the greater the number of bonds that can interact and oxidize. Generally speaking, a saturated ester product has an Iodine number less than 15.
Putting your Fluids to the Test
The most common tests for the life of a fluid are the RPVOT (ASTM D2272 or Rotating Pressure Vessel Oxidation Test), the Cincinnati Milacron Test (ASTM D2070) or TOST (ASTM D943). In these tests, fluids are subjected to the worst conditions possible in an effort to force them to break down. These tests are used to monitor oils for losses in oxidation resistance and increases in acid levels. Many manufacturers and end-users regularly subject their systems to fluid testing to determine what steps need to be taken in regards to system maintenance. It is important to review the TAN (Total Acid Number) in your lab results, as this may provide you with some indication that your fluid is breaking down. (See Graph 2)
The TAN, or Total Acid Number, is a test which indicates the level of deterioration of a hydraulic fluid. A high or increasing TAN number indicates that your fluid is oxidizing or hydrolysis is taking place. Monitoring the TAN levels in a hydraulic system can provide an early indication of a potential problem, and allow preventative maintenance to be conducted on the system as needed, saving both time and money.
In terms of standard mineral oil, an increase in TAN is always a bad thing. However, with synthetic ester products this is not always the case. In synthetic lubricants there can be acidic components that do lead to corrosion, but there are also acids that act as corrosion inhibitors. In case of mineral oil based lubricants, the TAN should not exceed the value of 2mgKOH/g, but the TAN values of saturated synthetic alternatives may increase up to 5mgKOH/g without leading to any problems. These values may vary and should be verified with your fluid manufacturer.
Hydrolytic Stability
Hydrolytic stability is the ability of a fluid and its additives to resist this decomposition in the presence of water. For those OEM’s manufacturing equipment that will operate near waterways or with systems that may have continual issues with condensation in the reservoir, this topic is extremely important. Clients want a fluid that is stable and will not break down or alter its composition when a small amount of water is present in the system.2
A common misconception in the field is that some fluids can handle high levels of water before reacting, and therefore it is acceptable to leave high levels of water in a hydraulic system. Simply because a fluid claims a high level of stability when water is introduced does not indicate that the hydraulic system will function well with that level of water ingression. The amount of water content required before a high-quality saturated synthetic fluid, such as Panolin, will begin to react is so significant that it is very likely that the system will begin to see major issues due to the water itself before the hydrolysis takes place.
Providing a Solution
Panolin HLP Synth is a fully synthetic, high-performance, readily biodegradable, non-toxic hydraulic fluid made from saturated esters. It is combined with high-grade additives, is zinc-free and therefore also environmentally friendly. The Panolin product leaves no sheen when it is spilled on the water, but rather appears as light foam that is visible for easy cleanup. It is able to resist oxidation at high temperatures and high pressures, and prevents gumming and deposits within your hydraulic system. Panolin does not affect conventional sealing materials, and it provides excellent corrosion resistance and wear-protection.
Lifetime Fill Capabilities
Perhaps the most impressive aspect of the Panolin HLP Synth product is its lifetime-fill capability. Due to its base composition and saturated nature, Panolin does not breakdown over time. Thus, this fluid is able to last within a hydraulic system for extremely long periods of time without any oil-change requirement, decreasing downtime and maintenance costs. In the past, equipment operators would fill a machine with vegetable oil to perform one environmentally sensitive job, then drain it and refill it with mineral oil once the job was over. Those days are now over, with Panolin offering durability, biodegradability and non-toxicity all in one fluid. Test documentation shows that some clients have been using Panolin in their machines for over 130,000 hours without ever changing the fluid. (See Graph 3)
Panolin in Action
Panolin has been used extensively in Europe for decades in applications ranging from railroads, cranes and offshore platforms, and its popularity is growing rapidly in the United States where it is now available. Regulations for mobile equipment operators working in environmentally sensitive areas will only become stricter in the years to come. Many companies have already started using Panolin products in an effort to promote their ‘green’ image and gain contracts with clients because of their environmentally friendly systems. Manufacturers of off-highway equipment such as construction machinery, geophysical seismic vehicles, crane & rigging equipment, pile driving equipment, and even drilling rig fleets have all turned to Panolin for a biodegradable, non-toxic alternative to mineral oils that can also offer exceptionally long life in the most rigorous applications.
Not all fluids are created equal, and it is important to understand the differences when selecting your biofluid. If you have any questions related to your current biofluids, general biofluid selection, or would just like to put your biofluid to the test, please feel free to contact Panolin or Hydraquip and we will be happy to assist you.
This information was provided by Chauntelle Baughman of Hydraquip Distribution, Inc., Houston, Texas. For more information on Panolin products, please contact her at 713-680-1951 or email [email protected].
Sources:
1 "EM 1110-2-1424 (28 February 1999)." Publications, US Army Corps of Engineers. 28 Feb. 1999. Web. 24 June 2011. .
2 Ruch, Martin. "Panolin Atlantis - Panolin HLP Synth." Message to the author. 24 June 2011. E-mail.
3 Plasser & Theurer. "Lowering CO2 by Using the Right Oils." Rail Infrastructure: The Specialist Magazine for the Railway Infrastructure Industry Apr. 2011. Print.
4 Cardev. "Panolin Filled Machine Used for Underwater Excavation Close to Beach."Panolinfo, United Kingdom 12. Print.
5 Cardev. "Panolin Monitoring the Situation." Panolinfo, United Kingdom 25. Print.