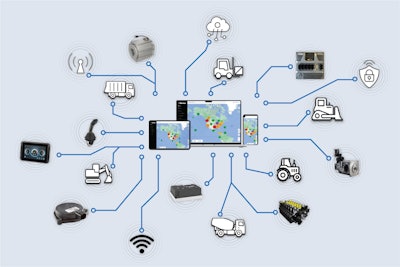
One of the biggest buzz words tossed around in the manufacturing world today is the Internet of Things, better known as IoT. Stated simply, IoT is a network of interconnected devices that exchange data with other IoT devices and over the internet or other communication networks. Companies of all sizes are looking at ways to leverage connected technologies and identify ways to use them to increase profitability and productivity.
The reality is that IoT is not a new term. It was originally coined in 1999 but didn’t reach mainstream awareness until 2014. Even then it took some time for companies to truly understand its potential and how to put it to work for their own operations. In the past five years, the use of IoT has accelerated tremendously. Yet, its current use is still small compared to what is projected over the next five years. According to Spherical Insights, the global IoT market size is projected to grow from $347 billion in 2023 to $3,267.4 billion by 2033, exhibiting a CAGR of 25.13% during the projected period.
While the IoT term is now common, its concepts are rooted in network management principles, which accurately describe the phenomenon as the ability to gather data amongst products that are connected and able to exchange information. The type and amount of information that can be gathered has increased exponentially with the growth in electrified systems and components with embedded microprocessors and sensors.
Since electrified systems and components with microprocessors naturally gather data, their popularity has shifted IoT trends. Not so long ago, IoT for vehicles was primarily for telematics. Manufacturers used this tool to identify the status of various assets, including their current location and operational state.
In contrast, today’s connected assets have a variety of products that can provide enhanced diagnostics, sensor data and performance data and trends over the vehicle’s controller area network (CAN) bus, providing a detailed level of understanding of the machine. As a result, we now have more connected products’ data at our disposal, including pumps, valves and inverters, to name a few. A benefit of this is that it allows us to gather data to tune a system to peak performance. For example, the ability to gather inverter data, which controls the motor and pump of an ePTO system, allows greater analysis to optimize the duty cycle and performance of this electrified subsystem.
A newer area of opportunity made possible using more connected electrified products is in the area of sustainability. In an effort to conform with the latest mandates, qualify for the newest carbon credits, and attract customers who prioritize green initiatives, companies are benefiting from the ability to reliably document how much fuel and energy they are saving and/or how much they are reducing CO2 emissions through their electrified systems. According to the Environmental Protection Agency (EPA), electrification in the transportation sector has the potential to reduce GHG emissions by up to 1 gigatonne in 2050.
Through IoT and the use of connected products, it’s possible to get reports that confirm performance attributes, as well as improve a team’s ability to troubleshoot assets remotely, saving time and money. According to McKinsey, predictive maintenance using IoT data can reduce maintenance costs by 10% to 40%.
A New Wireless Generation of Products
Wireless technology powered by cellular and Wi-Fi has opened up a whole new world of opportunities in remote diagnostics and updates using over-the-air (OTA) technology. Prior to OTA technology, machines could only be diagnosed, updated or fixed with a technician right next to them. Now, there is no need to physically connect products to each other or to people, effectively reducing the number of tech visits required and shortening diagnostic time. A cellular connection is the ultimate solution because the machines can be anywhere in the world.
A word of caution is, however, worth noting when using wireless technologies relative to potential breaches or malfunctions. According to cybersecurity best practices, OTA updates should always be done in safe, secure areas and only when the vehicle or machine is stopped or locked to avoid it being engaged and causing injury and only by personnel credentialed to do so.
Barriers to IoT Adoption
Despite all the advantages of having connected products, many companies have yet to fully leverage a comprehensive IoT program. There are multiple reasons for this, with cost concerns and lack of an understanding of value topping the list.
While it’s true that these newer technologies result in upfront investments, the savings they generate in reduced labor and technician travel time, as well as in enhanced machine performance and uptime, typically offset these added costs within the first few months. If critical components in the system are connected, it may be possible to fix problems and optimize performance with a simple software update that does not require an in-person visit. Not only does this reduce labor time but also ensures an operation gets backed up and running in record time. According to Microsoft, IoT can deliver a return on investment (ROI) of 30% to 200% in less than two years for most organizations.
Another cost-saving example is a machine or vehicle that keeps failing and causing unnecessary downtime. By analyzing data from connected products, it could be possible to diagnose and fix the problem sooner and increase productivity. For example, some companies are already researching various AI-powered technologies that could further assist in predicting failures to minimize downtime.
Diagnostics have gotten more sophisticated because today’s electric machines are more complex. In addition, industries of all types and sizes are losing their seasoned workforces in record numbers, and these veterans are being replaced by younger, more inexperienced workers. The additional data provided by connected products helps get these newer workers up to speed faster by providing them with more tools and information.
Choosing the Right Connected Products for Your Application
Today, there are more connected products available than ever before. Controllers, sensors, pumps, valves engines and inverters all have the capability of being connected. So how do you know which connected products are right for your needs? Start with this quick checklist:
- Identify the critical components in your system
- Confirm the components can send the needed signals over the CAN bus connection
- Confirm the IoT Gateway can connect, gather and send the critical signals to the IoT portal for analysis
Choosing Tools for Remote Access & Customization Options
With connected products and an IoT gateway, it’s possible to get a machine and fleet data to an IoT portal where it can be aggregated and analyzed remotely. It’s also possible to customize your data program to communicate the most vital information you need to improve your profitability and productivity. Reports can be created that analyze the performance of a fleet of assets. For example, armed with this detailed information, you can accurately see battery levels, engine hours, service time and work hours electrified, which enable you to see which operators have the best outcomes and subsequently understand best practices that should be put in practices across the team. Enhanced diagnostics and performance data also allows you to identify trends and minimize downtime in advance.
With custom fleet summary reports and operation health reports, you can also track asset location, fuel levels, voltage, operator status, engine RPMs and temperatures in real time in both local time, as well as the asset’s time zone.
Detailed, custom reports can provide valuable insights into how your assets are being used. As a result, you may learn that you could increase profitability with the addition of another machine. Or you may learn that some assets are being under-utilized and could be transferred to another area for better utilization.
Conclusion
The global mobile IoT market is expected to see billions of dollars in growth by 2033, partially due to growing electrification trends. What was once a technology used exclusively for simple diagnostics has grown to be so much more. If you’re not taking full advantage of this latest technology, you could be left behind.
Today, it’s all about doing everything faster, smarter and cheaper. Connected products, while slightly more expensive than nonconnected components, will increase over time, especially as microprocessors and CAN interface costs are likely to come down. As connected components evolve and remote IoT insights become more valuable, improving asset performance, reducing total cost of ownership and improving uptime will be the outcome.
Anne Marie Johlie is the head of IoT and Smart Connected Products Center of Excellence for the Motion Systems Group at Parker Hannifin.
Rupa Bhagwat is a product manager of IoT and Smart Connected Products Center of Excellence for the Motion Systems Group at Parker Hannifin.