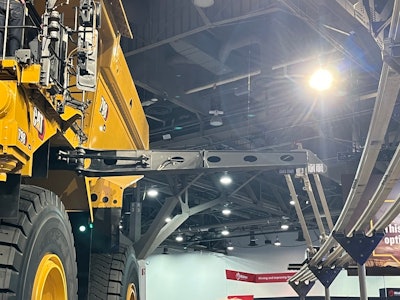
MINExpo 2024 in Las Vegas concluded Thursday with the meetings and group discussions emphasizing how companies can improve uptime and safety and operations while keeping downtime low. It’s a tall order for companies working in the mining industry because of the particular challenges they face. Productivity and demand are high and the profit margins are low because of the high costs associated with the materials used.
It's a challenge, but it’s one companies are confident they can address.
For Tom Chambers, vice president of ZF Group’s business unit, it comes down to giving their customers the best information they can.
“With predictive modeling and analytics, we build that into the relationships we have,” he said. “When you talk about uptime, the business cycle is really urgently pushing the supply chain and keeping it strong.”
They lived up to their mantra during the COVID-19 pandemic and kept operations going as an essential supplier.
Christoph Kainzbauer, head of industrial drives and managing director for ZF Group, said, “We are quite proud we never shut down. We kept on going and supplied the mining industry with what they needed. It was difficult, but we made it.”
Sometimes that’s the best thing to do. When the pressure is on and the path ahead looks difficult, pushing through is the best solution.
Provide dynamic energy for better movement
Caterpillar’s enormous booth in the central hall highlighted many innovations and some of the latest vehicles. One of the more interesting features, however, was a little hard to notice because it was seemingly off to the side, but that was part of the feature. Their dynamic energy transfer (DET) is a fully-developed system designed to transfer energy to diesel-electric and battery-electric large mining trucks while they are working around a mine site. It can also charge a machine’s batteries while operating with increased speed on grade, improving operational efficiency and machine uptime.
Thad Litkenhus, director of product management for Caterpillar, explained how placing the rail system on the side of the vehicle rather than on top provided extra benefits.
“How do you keep the truck moving and producing constantly? Stopping and refueling is downtime,” he said, adding the DET provides the truck energy while it moves. He also added the rail system is designed to be mobile and flexible and they can install a kilometer on a site in a matter of days and it can be shaped in curves rather than a straight line.
“It’s about providing electric autonomy and automation,” he said. “We certainly see the future to solving problems in a higher-value way.”
Providing real-time data to the OEM
Turning data into actionable information is critical in any industry, but in mining, where the difference can be millions. Glenn Kerkhoff, global industry principal for mining, metals and metals at AVEVA, explained his company’s process.
“At AVEVA, we’re about integrating mining with process. What we’re doing is collecting time-series data from machines into the industrial cloud,” he said.
Their industrial software platform, AVEVA Connect, is a unified industrial software platform that is designed to optimize operations and production. It is scalable and designed to provide the user insights.
Kerkhoff said they’re trying to improve three things for users: Reliability, utilization and productivity. Connect’s insights are designed to improve optimization by taking disparate sets of information and bring them together. From there, artificial intelligence (AI) and machine learning (ML) can help provide high-level analytics for the reliability engineer and give them the tools they need to make the correct insights.
Too often, Kerkhoff said, companies at looking at siloed data and getting a narrow view of a situation without understanding the bigger picture. He cited an example of a single truck not performing to requirements. While it’s possible something in the truck or the driver might be the reason why, more context is often needed to get the bigger picture.
Using predictive analytics also can improve productivity and squeeze out every last drop they can and make overall operations better and have them work in harmony.
Elokon’s ELOshield provides communications using ultra-wide band (UWB) with antennas and sends a noise and vibration signal to alert others in the area.Chris Vavra
Protecting drivers in and out of the truck
Elokon’s ELOshield provides communications using ultra-wide band (UWB) with antennas to communicate with drivers inside the trucks if someone is too close to the vehicle or if there’s a potential obstruction. It sends a noise and vibration signal to alert others and can even force vehicles to slow down if they’re within the danger zone. The range can be as far as 80 feet and alerting workers faster, according to Justin Barker, a regional sales manager for Elokon Group, make all the difference.
“Camera-based systems often can’t see around corners. So having that extra 4 to 5 seconds is critical and stopping something bad from happening.”
They also have a fleet management system, ELOfleet, which can provide information on a fleet of trucks and give insights on performance, which can be useful for a scenario where many trucks or vehicles are needing to run together in harmony.