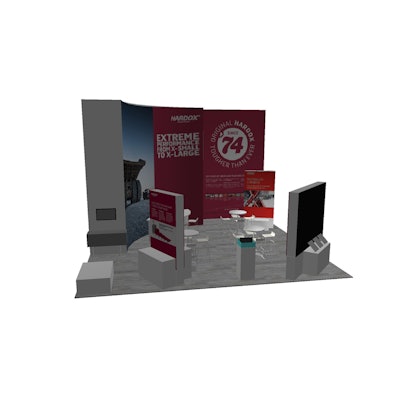
Hardox has literally set the standard for wear plate all over the world with its unparalleled combination of hardness and toughness. Visitors to CONEXPO-CON/AGG 2014 were able to see video of impact tests clearly demonstrating the huge savings in weight and gains in strength and wear resistance resulting from using Hardox. Using mild steel as a reference another display will show how the various grades of Hardox wear plate increase service life of wear areas. Samples of SSAB’s impressive – and unmatched – range of types, grades, widths and thicknesses of high-strength steels were also on display, as well as details of the company’s Hardox Wearparts program and unparalleled customer support.
Thickness used to be a limitation, but now SSAB offers wear plate in thicknesses from 22 gauge (0.7 mm) to 6-1/4 in. (160 mm). This – combined with new dimensions and its ability to double as structural steel – allows even greater creativity and opens up new possibilities. The booth will show the range of plate thicknesses offered as plate up to 10.9 in. (3.35 m) wide and 47.5 ft. (14.5m) long.
Also on display was SSAB’s unparalleled product portfolio: Hardox wear plate, Weldox structural steel for heavy and demanding applications, Domex structural steel for sustainable and lightweight solutions, Toolox pre-hardened engineering and tool steel, and overlay plate, pins and pipes.
The impact test video showed a drop test carried out with Hardox 450 5-millimeter thick (0.197 in.), S355 5-millimeter thick (0.197 in.), and S355 12-millimeter thick (0.472) wear plates. The 474 lb. (215 kg) torpedo was dropped from 9.2 ft. (2.8 m). The results: a weight savings of 59% when using Hardox 450 5-millimeter instead of S355 12-millimeter with plastic deformation of 17 mm for Hardox and 18 mm for the S355 plate. When comparing the Hardox 450 (5 mm) with the S355 (5 mm), there is a 50% reduction in plastic deformation (dent depth 17 mm versus 35 mm). The actual test plates are on display as an impressive display of Hardox properties.
Visitors could also see the Hardox wear stairs. Using mild steel as a reference and granite as the material handled, this display showed how the different Hardox grades achieve ever-greater wear resistance and service life. With Hardox 400, for example, wear life increases by 1.6 times, Hardox 500 by 3.4 times, Hardox 600 by 9.4 times and Hardox Extreme by 12 times. This is demonstrated by showing the decrease in thickness needed to achieve the same wear life – resulting in the ‘wear stairs.’
SSAB’s proprietary WearCalc software can be used to optimize materials with regard to cost, wear, performance and weight.
However the wide range of wear plate grades, widths and thicknesses offered by SSAB would not bring the benefits of longer service life and higher payload to end-users if manufacturers were not able to form, cut and join the plates in their workshops. The balance between hardness, toughness and workability – regardless of grade or thickness – is the key to the remarkable success of Hardox.
Customer support has played a key role in SSAB’s success. SSAB has a long tradition of providing assistance in design, wear, workshop techniques and production efficiency, as well as customer-specific innovation support. SSAB goes beyond offering technical support but also collaborates with customers to develop innovative products through its Knowledge Service Center. Support is always tailored to the customer and the solution so it’s not surprising that more than 75% of SSAB’s customers work with SSAB on development projects.
Members of the Hardox Wearparts program – who manufacture and install wear parts using the ideal steel for the job – will exhibit industry-specific wear part and overlay solutions.
SSAB will also be celebrating not only 40 years of manufacturing Hardox wear plate, now firmly established as the global benchmark for wear-resistant steel plate, but also that Hardox is now produced in the USA following the completion of a new quenching line at SSAB’s steel plant in Mobile, AL. Built as part of a $300 million project, it is the world’s most modern quenching line and raises SSAB’s U.S. quenched and tempered plate capacity by 220,000 metric tonnes per year.