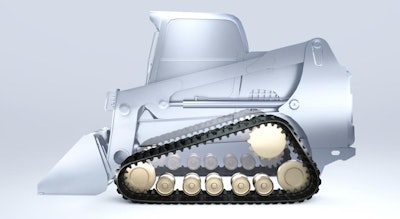
Varied applications and working conditions make it necessary for tire manufacturers within the construction industry to offer a wide range of solutions; expanding these product offerings was the theme for many during CONEXPO-CON/AGG 2017.
During the show, Trelleborg Wheel Systems, for instance, announced it is adding to its line of pneumatic tires in the North American market. Doing so enables the company to provide a full line of products for the off-road market, says Marc Margossian, Marketing Director for Trelleborg Wheel Systems in the Americas. “It gives customers more options from a company they already trust.”
Part of this pneumatic offering includes the Mitas range of construction tires, which became part of Trelleborg following the acquisition of CGS Holdings in June 2016. Margossian says,"Mitas has a strong presence in Europe through its agricultural range and has developed a good position within the construction market through some notable OEMs. In North America, Trelleborg has been a strong player in specialist construction niches through its solid OTR range and construction tracks; by adding the Mitas range we become a true single source supplier with a full range of proven, quality products."
Camso, formerly known as Camoplast Solideal, also exhibited its expanding line of tire and track products for the construction industry. Over the last 2 years, the company has undertaken an initiative to re-evaluate many of its legacy tires—including those for skid steers, telehandlers and its multi-purpose tire line—through a scrap tire analysis. Camso studied both its own tires and those of competitors to see why and how they fail; it found sidewall and puncture damage to be among the leading causes. It is using this information to develop its “Next Generation” tires, and plans to rebuild two-thirds of its compact construction tire lineup.
“When it comes to tires, you only have so much money to spend,” says Mike Dembe, Camso Product Management Director, North America and LATAM for Construction. He explains that a company may have the best tire in the world, but if it’s too expensive, no one is going to buy it, so it’s important to evaluate where to put the rubber and engineering to address failure points. “[The scrap tire analysis] really helped guide our hands to develop smarter tires, providing added performance and durability,” he says.
One of the tires developed based on the scrap tire analysis is the new MPT 753, a multi-purpose tire set to be launched in North America later in 2017. It is being launched in Europe first as it is designed for use on compact telehandlers, compact wheel loaders and mini-dumpers, all of which are more popular equipment types in that market. However, Dembe says Camso does see these smaller pieces of equipment starting to become more popular in North America, as well, which is why the tire will be available in both markets. The non-directional tread pattern on Camso's SKS 753 is one of many new design features to come about from the company's scrap tire analysis.Camso
A key feature of the MPT 753 is its non-directional tread which has a higher lug to void ratio so that there is more rubber to wear off, making the tire last longer on abrasive surfaces. Dembe says Camso used one of its most premium rubber compounds for the tire to further aid abrasion resistance and durability. Void guards on the tire—little patches measuring just a couple of millimeters—were included to provide tread impact resistance. “We wanted to do something without sacrificing tread depth,” explains Dembe. “We have these little void guard protection patches and what we found was a 10% better tread impact resistance, so 10% fewer flats. It’s just a tiny bit of rubber, but it’s using that rubber smartly.”
Another development based on the tire analysis is the impact guard and reverse sidewall concept. Camso’s previous sidewall design consisted of a tapered wedge shape; Dembe says this design has been completely reversed so that the thicker part of the tire is farther away from the shoulder and is now closer to the bead area. He says this does two things, one of which is to remove the “shelf” that previously existed and was the weak part of the tire. “Tires don’t like hard edges or angles [because] it’s something more to rub up against and actually cause structural damage,” Dembe says. “We removed that stress point and, in reversing the sidewall, there’s a wedge shape at the bottom.” This wedge pushes material and objects away from the tire before they can cause any damage. Due to the success of this design, Camso will be including it on all of its next generation tires.
“The most important trend BKT has seen in tires for the construction industry is using multiple design cues to increase operational efficiency on the job site,” says Gary Pompo, Manager Field Technical Services, BKT USA Inc. As such, the company integrates various technologies into its tire designs to meet these efficiency needs. Its new Earthmax SR 35 tire, for example, includes steel belts to resist snags and punctures, helping ensure the longevity of the tire’s lifespan. The tire also includes a cut-resistant compound to extend tire life.
Radials on the rise
According to Alliance Tires, use of radial tires has been increasing within the construction industry over the past 15 years, with a slight dip seen during the recession says Steve Vandegrift, Product Manager – Construction, OTR at Alliance Tires Americas. In addition, he notes the European construction equipment market has been almost entirely on radials since the early 2000s. The BKT Earthmax SR 35 tire includes steel belts to resist snags and punctures, helping ensure longevity.BKT USA Inc.
The increased flotation, improved traction and additional stability radial tires can provide relate directly to improved production, explains Pompo, which helps make them an attractive option for fleets. “While there is still demand for bias tires, veterans in the industry are feeling more comfortable with radials now, which is causing the increase in demand.”
Vandegrift says the move to radials was first driven by OEMs whose engineers appreciated the technology advancements occurring in the tire market. “They realized a more flexible sidewall, significantly larger footprint, and the capacity to increase the load on these radials,” he says. “Since then, the replacement market has been picking up as machinery owners see the benefits of radials or just replace the tires that were original to the machine. Either way, it’s creating increasing demand for construction radials.”
Among the many benefits radials offer is their larger, more evenly distributed footprint. This is due to the body plies being oriented at a 90-degree angle with the bead, creating a strong sidewall that is more flexible, says Vandegrift, whereas body plies on a traditional tire meet the bead bundle on a bias, or slant. The layers of overlapping fabric create a stiffer sidewall which lifts the edges of the tread so less of the footprint is in contact with the ground.
Vandegrift notes the wide footprint and fact the radial construction distributes torque more uniformly across the tire’s circumference produces more even tread wear and a longer tread life. “The larger, more uniform footprint of radials also provides better flotation and less rolling resistance, improving fuel economy,” he says.
Research data has shown radials can offer a 16% increase in fuel efficiency, up to 20% less rolling resistance and up to 13% higher machine productivity compared to bias-ply tires.
The flexibility of the sidewalls enable the tire to better conform to the terrain, enhancing ride quality for improved operator comfort. In addition, the sidewall acts as a suspension system which absorbs shock, further improving comfort, as well as reducing machine wear. “Many customers tell us that the time and money they spend maintaining the frames, suspensions and axles of their equipment have gone down after a switch to radials,” says Vandegrift.
He says the initial cost of radial construction tires is about 20% higher than an equivalent-sized bias ply tire, however, Alliance Tires has seen radials last twice as long on job sites “so the return on investment, figured by dividing the purchase cost by the service life, is outstanding."
While both Alliance Tires and BKT see increased use of radials, there are applications in which bias-ply tires are still the better option. The thicker sidewall of the bias tires is particularly suited for use in low-speed construction jobs where there is a high potential for sidewall punctures to occur.
“Radials are most appreciated by construction contractors who track the actual cost per hour of running their equipment—the money spent on tires per hour of operation, the amount of fuel consumed per hour on a contract, and the cost of downtime, which of course is less frequent with longer-lasting tires,” says Vandegrift.
He says radials are best suited for equipment which runs on the road, especially for long cycles, such as rock trucks and backhoe/loaders shuttled on the street. The radial’s flexible sidewall creates a broad, flat footprint for a comfortable ride on this surface type. Applications in which sidewall stability is paramount—such as machines working across slopes or telehandlers whose center of gravity shift as their load is raised or lowered—would benefit more from the stiffer sidewall of a bias-ply tire.
The transition to tracks
Dembe says Camso is also seeing a greater trend toward the use of tracks on construction equipment. Much like in the agricultural industry, machine operators are looking for improved traction, flotation, stability and durability, all of which he says tracks provide. “You’ve got a wider footprint, a full-length surface—for a larger footprint contact patch—that [equates] to reduced ground pressure, better pulling power and more torque,” he says. “This is where the whole industry is trending.”
“Across the construction industry, we’re seeing greater adoption and use of rubber tracks on loaders to facilitate projects at a variety of job sites,” adds Koji Nakayama, Vice President, Bridgestone Industrial Products Inc. The stability and traction they provide enables equipment to be used in applications it might not otherwise have been able, enhancing its versatility. Nakayama says it’s been easy for the industry to transition to rubber tracked equipment since it does not require a significantly different skillset to operate compared to traditional skid-steer loaders.
He adds that rubber tracks have a niche market within the construction industry. “We are seeing tracks used on loaders at one specific job site, rather than on vehicles that are moving between operations since tires provide the versatility and speed needed to move between jobs more easily.”
To meet the growing demand for track systems, Camso has developed a Conversion Track System (CTS) prototype which it exhibited during CONEXPO-CON/AGG. The CTS is a bolt-on track and undercarriage solution currently intended for use on telescopic handlers, compact wheel loaders, smaller full-size wheel loaders and mini dumpers.
The company says the CTS offers customers the benefit of being able to easily switch between tracks and tires as necessary. This enables more flexibility in their operations and eliminates the need to choose between only having a tire or tracked machine. Much like Camso’s agricultural version, the CTS is a permanent solution that can be left on a piece of equipment if desired.
Camso is working directly with OEMs to design the CTS precisely to specific machine platforms. A generic aftermarket version will also be available that will be designed as an “all makes” model to fit a variety of machine types. This version will also have an adapter plate that can be added or removed to ease installation on various pieces of equipment.
Bridgestone also introduced its Vortech rubber track system during the show. According to the company, the track was designed to help improve driver efficiency and workability in compact tracked loader applications. It achieves this through an optimized internal structure and tread pattern to lower the bending resistance which occurs when rubber tracks rotate to enable more fluid vehicle movement. The H-shaped tread pattern of Bridgestone's Vortech track provides 60% more biting edge around the tread lug, improving traction in various terrain.Bridgestone Corp.
The H-shaped tread pattern expands the edge of the tracks, providing 60% more biting edge around the tread lug compared to standard tread patterns. “This unique shape results in a consistent grip and improved traction across a variety of job sites,” says Nakayama. The tread pattern works in tandem with the track’s optimized embed placement, as well, to minimize vibration during machine operation and create a smoother, more comfortable ride.
Though there is no one-size-fits-all approach for the construction industry, tire manufacturers’ continued efforts to expand and evolve their tire—and track—offerings will ensure there is a solution to meet various customer application needs.