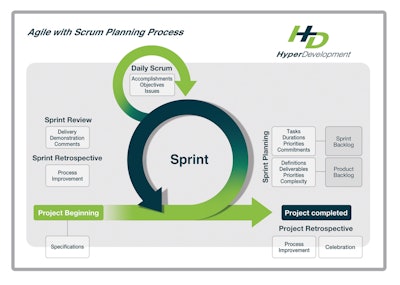
We have radar for the sky, sonar for the water, aerial photography for surface images, yet what do we have that lets us see into the ground? Imagine knowing precisely where to drill for the exact material you’re looking for amid hundreds of square miles of untapped resources under your feet.
If mining equipment owners and operators could essentially see into the ground and know exactly how dense the material was 400 or even 900 feet below the surface, they would know what drill bits to have on hand and when to switch them out without worrying about damaging the machine.
With the down economy and new equipment sales falling across the board, many OEMs are focusing on remanufacturing and repairing older equipment to keep customers coming back. MicroMentis’ platform allows OEMs to sell a machine equipped with a technology that can ensure safe, accurate and efficient digging, drilling and excavating boosting owner/operator confidence in the machine, and ultimately saving time, money and protecting the land from unnecessary damage.
It began as merely a vision of Daniel Rioux, president of MicroMentis Inc., Laval, Quebec, Canada, chief technical officer (CTO) and inventor of the MicroMentis technology platform, SWIPS (Surface Wave Intelligent Profiling System). In 1983 he was working for a company to identify why vibrations from a train were causing waves related to structural damage of buildings. “Working with the propagation of those waves, I equated it to surface waves in the ground and studied, at the time, the possibility of looking into the ground,” Rioux says. “I thought it would be a good technology to look into, but was limited to the geotechnical theory and faced some very challenging issues.”
In 2001 he met someone doing his PhD on the propagation of surface waves into solid media who immediately solved all of Rioux’s issues. From that moment on, the idea to look into the ground was patented, the hardware design was developed and patented, and the decision to build the new technology was made. “We went into the civil engineering field collecting and reinforcing data and published a scientific paper on the technology. Through that we were able to get proof of concept… so it became a question of supplying a hardware platform that was suitable for our customer’s applications,” Rioux says.
Gathering information
SWIPS integrates information from sources such as aerial photography, geospatial and engineering data and will visualize, analyze and model the physical and mechanical properties of solids fast and precisely in a non-intrusive manner.
“The first step is to acquire as much information that you already have on file, such as aerial photography, topographic maps, gravity anomalies or airborne survey such as magnetic. You can imbed that information into the MicroMentis SWIPS platform,” says Rioux. “Once you’ve combined the [spatial information] together, you can evaluate the substrate of the underground… The information only has to be in regards to georeference with standard units of measurement.”
Since the equipment used on site is bound by the ground material’s properties, such as density and location, the more information one has ahead of time allows for a more informed choice of the exact equipment needed to extract the specific materials. This sort of efficiency means less wasted time, fuel and money transporting unneeded equipment, fewer wasted resources and a safer environment for the equipment.
If it is a dense material, the site manager will know to use high quality steel parts during extraction, as well as the appropriate time to switch a drill head and how much torque to apply to avoid part damage. If the density were to go unknown, the equipment could be ruined; and if the operator chooses to proceed with extreme caution to prevent equipment damage, the performance of the equipment and efficiency can be sacrificed due to being over cautious.
Once the information is gathered and a strategy is formed and evaluated, it’s time to conduct the measurements using the SWIPS hardware: 16 Wireless Sensors, the User Interface and the Impact Generator. All components are self-installing, self-healing, self-communicating and self-calibrating — meaning they automatically find the correct operational setting.
The user interface screen will propose a grid for sensor placement based on previous analysis and data.
Wireless Sensors
The system’s sensors are self-powered for extended periods of operation through rechargeable batteries and are wirelessly connected. They feature a solid, durable and water-resistant structure housing with a flexible attachment module that allows the sensors to be placed virtually anywhere, for example, even on the wall or ceiling of an underground mine. They were designed to withstand a 1,500 g shock.
“The sensors contain a screen with an arrow that always points toward where the sensor should be installed based on the suggested grid mapped out earlier. [This makes the SWIPS system] very easy to use so people can be trained quickly on how to take measurements,” he says.
Because of its three-axis system and its Inertial Positioning System, the sensor’s exact coordinate location is known at all times. While the grid suggested by the operator interface is important, the sensors don’t need to be oriented in a specific position to be effective, reducing the margin of error. The sensors’ high bandwidth and extreme sensitivity allow them to quickly transfer large amounts of information back to the user interface for analysis by the equipment operator or worksite manager.
“Our sensors are in the range of 300 ng of sensitivity,” says Rioux. “No sensor on the market can cover our span of frequency (0 to 2.5 kHz). Your environment may be solid like rock, or it may be softer like top soil. It doesn’t matter, the same sensor can measure all of those varying levels of density.”
MicroMentis is currently finishing its sensors calibration test lab. “We had to develop and design the calibrations, as well. And then of course, how do you calibrate those? So, we have to rely on the National Research Council of Canada to calibrate the test bench.” The lab will be located in Laval, Quebec, Canada.
Impact Generator
The patented impact generator’s 6.5-in. LCD touch screen is smaller in size yet identical to that of the user interface (12 in.) for easy use. The device generates a surface wave, which has similar characteristics to an earthquake. “It’s like having a 300 kg weight dropped from 3 meters.”
The Impact Generator can also be remotely controlled. Its versatile attachment base, like the wireless sensors, allow it to be used on any type of solid surface. Also like the wireless sensors, the impact generator is georeferenced through embedded inertial positioning technologies.
With a press of a button, the impact generator charges, signals it is ready and sends the wave into the ground. Once the wave is generated and the results are sent to the user interface, the sensors closest to the impact generator are moved beyond the farthest sensors and another impact is sent. The system is repeated and waves are repeatedly sent after each sensor move until the desired area to be analyzed is covered.
The MicroMentis sensors pick up the wave as it moves through the ground material. This is different than seismic readers which measure the refraction of the wave as it rebounds off of a material or surface. “The data is acquired and if there is any sort of anomaly there are tools to help the user modify the wave automatically. Data can be checked in real-time on site using the user interface,” says Rioux.
Processing the data
“Once the data is collected, you transfer the data and proceed with the first data analysis, pre-modeling. We have algorithms that describe the behavior of the rock,” he says. The SWIPS technology profiles Vs (shear wave velocity), Density, and the Poisson Ratio (the relationship between collecting and spreading when you press on a material). SWIPS can then determine the mechanical properties of the solids such as the Modulus of Rigidity, the Modulus of Elasticity and Liquefaction index.
The properties and profiles are integrated with the previously gathered data and the system graphically details the information into an in depth picture of the physical and mechanical properties of the site in 2D.
“Now we have physical properties, so if you want to know how resistant or brittle the material is, you have all of the data. Besides that, we have the other mechanical data parameters. There is a relationship between those characteristics and a rock family-type which helps to establish the likelihood of a specific rock type.
“Adding a third dimension to the relationship graph we can see the properties as they are in the ground to determine drill holes and angles, so you only have to drill two holes to confirm the rock type.”
Drill Hole Wizard complimentary software by MicroMentis helps identify where to drill and at what angle in order to increase the drill hole yield. Tunnel digging machines can have these sensors mounted on the drill head (as pictured left). “You apply the head to the surface and you acquire what is ahead of you,” he says.
User Interface
The User Interface manages the entire SWIPS technology. It is because of the interface that the user can formulate a plan and orient the work by controlling the entire process of data acquisition in the field. It then consolidates and integrates all gathered information for meaningful analysis. The interface guarantees that all sub-components are fully functional and calibrated once the SWIPS technology is powered and linked.
Like the sensors, the user interface is wireless, portable, self-powered, robust and easy to operate, as well as is georeferenced through embedded GPS and inertial positioning technologies. It has a set of powerful processors, a dual-core and a processor capable of quickly calculating and mapping the input data.
Moving forward
“Mounted on a piece of equipment, you can have a control mechanism that, based on the 3D properties of the map, can alter the behavior of the equipment to change the feed rate, for example, automatically. Everything can be embedded into a piece of equipment,” says Rioux. People operating a backhoe can use the technology to avoid damaging the equipment on rocks while digging.
“Accuracy is based on the sensor spacing. Mining is a lot deeper, over 200 meters, but if you are within 30 meters like on a construction site, you can use shorter spacing and get a more accurate reading of buried structures,” he says.
“The SWIPS system lets you know the ground properties, so for specialists trying to develop strategies for what type of equipment to use, knowing ahead of time what you will be finding, where and to what depth, how solid (dense) the ground is, or whether or not there are some fractures in the ground” offers fast ROI, equipment protection and efficiency.
In another instance, a person who will be doing some drilling and blasting will be able to map out how best to fragment the rock. Having a better drilling and blast pattern and a better firing sequence will produce better rock fragmentation, which drives truck capacity, “so you can increase efficiency by 20-30% for truck capacity as well as for the loader,” Rioux says.
Currently there are no trucks equipped with the technology running in the field. “We are still in the development side, so now we are testing and finishing the calibration bench since we drastically increased the performance of our sensors.”
A person who acquires the device today will be able to upgrade the system later, keeping the system dynamic and current. “We are using state-of-the-art components, some of which are not even on the market at this time. We are working on the first release from the manufacturer and we’re putting that through very strict tests.”
“We’re just at the beginning of this science. It’s very young in the market and I think people will find new ways to address their needs through our technology,” Rioux concludes.