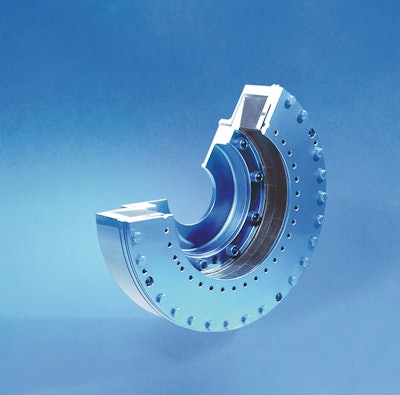
There are a lot of safety issues for an operator to watch for: falling objects, fire, debris, holes and dozens more. But how do you protect an operator from something he can't see?
Noise, vibration and harshness (NVH) is a serious health issue facing operators, but bigger ear plugs and thicker seat cushions aren't going to solve it alone. When deciding how to conquer the NVH forces, it may be best to know what the sources of noise, vibration and harshness are.
Vehicle noise can derive from a variety of places — engine, muffler, fan, hydraulic system, accessories such as gears, chains and other vibrating components — and each system has a multitude of noise reducing solutions.
Perception of noise directly influences a customer's acceptance of a product. "The overall noise level of our products is the parameter that is documented in product literature, but it's the customer's perception of sound quality that is the true measure of perceived product quality," says Mike Beyer, technical specialist - NVH, Eaton Corp., Eden Prairie, MN.
Noise is a wave
Noise: According to NVHmaterials.com, both structural borne and airborne noise have two unique ways of treatment. Structure borne noise is solved through means of damping (no, not dampening, there's no need to get anything wet) and isolation. Airborne noise can be blocked by barriers (walls, thick glass) or reduced by absorbers, such as foam insulators.
Vibration: Whole body vibration (WBV) deals with the transmission of vibration into the human body and the effects that vibration can have on an operator in the short- and long-term.
Shock vibration is a more jarring and unpredictable vibration that may occur while driving over a rut or hole causing an immediate effect or injury in the short-term to the operator.
Harshness: The human perception of noise, or vibration, or a combination of the two, that cannot be measured directly in engineering units. Each person has his or her own opinion about harshness, although there are common threads to our likes and dislikes which influence our preferences for one product over another.
Hydraulic system
Eaton's Fluid Conveyance Noise, Vibration and Harshness Technology lab (Eaton FC NVH), Maumee, OH, is an integrated and custom solution to fully optimize noise and vibration reduction within any hydraulic system where the transfer of fluids is present.
The use of Eaton's FC NVH solution can be applied in applications which range from power steering lines, to hydraulic pumps, to active ride systems. Eaton has provided fluid conveyance solutions for two decades for automotive applications and is now applying similar techniques for heavy-duty applications.
Variations in fluid flow, or pressure ripples, are created by the pump. The ripples create energy fluctuations which pass through the fluid to the structural components and into the air as noise. "Whether it's fluid-borne or airborne, noise is still a wave," says Chris Schadewald, engineering director, Fluid Conveyance Div., Eaton Fluid Power - Hydraulics Business.
Eaton FC NVH utilizes a custom hose assembly that specifically targets the fluid borne noise to reduce overall noise levels without over attenuation. A special tuner cable is designed to match the specific dynamics of each machine.
Specially designed tuning cables allow energy from the pressure ripple to escape at the wave's peak, reducing the amount of energy transferred to the system, thus lowering the amount of airborne noise released. Eaton's software analyzes hydraulic system characteristics to optimize the noise reduction.
Eaton's FC NVH lab allows Kurt Steinberger, lead engineer - NVH, Eaton Fluid Power - Hydraulic Business, to test systems or machines on site and utilize Maumee's fluid conveyance prototyping capabilities, as well as its materials test lab, to diagnose the noise problem, design and create a unique system solution in one location.
"Due to the fact that there is no one-size-fits-all solution, the challenge is to work within the OEM's design parameters as it relates to product envelope size and system pressure," says Steinberger. The Eaton FC NVH team needs to work within the OEM's design parameters. Not only can Eaton provide the NVH solution to the customer, but the solution might also result in additional benefits which could include an increase in production throughput and a reduction in components and overall machine weight.
Eaton's capabilities allow the NVH technology team to find more proactive solutions to give OEMs a more off-the-shelf solution. Right now each solution is custom made, but with more research, common elements will emerge.
Complementing Eaton's FC NVH capabilities are an in-house hemi-anechoic chamber in Eden Prairie, MN, and proprietary software. These tools enable Eaton to diagnose overall sources of NVH, model the system and run simulations to find the optimal solutions, and present the results and options to the customer.
By reducing noise in the hydraulic system at its source, Eaton can offer benefits including operator safety/fatigue reduction, a competitive advantage in the market, and the elimination of alternative noise suppression devices such as a resonator, attenuator or accumulator, which lowers part numbers, assembly time and cost.
Engine system
"As a result of higher injection pressures needed to control the particulate matter for Tier 4, there is an increased noise source from the injection pump itself," says Robin Woodward, operations manager, Global Engine Development U.K., Perkins Engines Co. Ltd., Peterborough, U.K.
"The higher the amount of pressure you have, the bigger reactive loads you have and the more noise can be transmitted out from the pump into the gear train and engine structure. That's something that you need to manage."
To tackle engine noise, Perkins does things like balancing internal loads to the pump to optimize the overall design. It also pays a lot of attention to the gear train, controlling some of those reactive forces by reducing the backlash in the gears, and testing different gear configurations. "Those things are very affective at reducing front end noise," Woodward says.
"Then there are the manufacturing control issues that go along with that. When you're running a low tolerance gear train system, you have to be able to repeat that in a series production environment."
Perkins does work on sound attenuation materials, for example, laminate materials are evaluated for their ability to reduce resonance of components such as front end covers.
The company also has three semi-anechoic chambers (shown on the cover and lead image). "We'll evaluate the airborne noise in there and the effects of all of the development changes that we made on the design as it exists," he explains. "We measure the bare engine noise, then rank which particular areas of the engine are producing the highest levels of noise. We'll then look at the design to see what we need to do to improve noise levels, if necessary."
"What we tend not to do, unless as a last resort, is to add shielding on the engine to reduce the noise. It's an expensive way to do it, which we avoid if at all possible. It's ultimately about understanding how internal forces are transmitted to the surfaces"
The major part of noise testing for Tier 4 isn't started yet, but Perkins is looking at the increased injection pressures and predicting the pump design as a source of increased noise. "Mitigating design features have been included in the engine design wherever possible."
Perkins has also taken on more responsibility for sound in after-treatment devices. "In the past, we would give our customers a bare exhaust sound and they would use that information to design the muffler," he says. "You get quite a bit of sound attenuation through a DPF. Perkins has to work closely with the end-user and the machine supplier to understand whether that's going to be acceptable or if it needs tuning to have acceptable noise levels during machine operation."
John Bair, executive director at the Center for Advanced Vehicle Design and Simulation at Western Michigan University, Kalamazoo, MI, explains other sources of noise when dealing with an engine, specifically on-highway trucks. "Engine firing integrity is obviously important to low noise and vibration levels. Any anomaly in fuel flow, injection, timing, etc. can be a problem. Engine mounting integrity is also paramount. Worn or damaged mounts can allow contact between engine, frame, cab or hood and create noise and vibration problems."
Driveline couplings
Reciprocating systems such as compressors, pumps and engines produce systemic vibratory torques. Additionally, rigidly connected components in a driveline will have natural resonance frequencies which will be excited at certain speeds. These engine and natural vibrations stress the driveline system, shortening component life due to wear and fatigue.
With emissions regulations demanding increased fuel economy, lighter more powerful engines have surfaced. With fewer cylinders and an increased power density, torsional vibrations become more severe due to lower rotational intertias and greater torque fluctuations.
The Highly Flexible Coupling from Voith Turbo Inc., York, PA, reduces harmful torsional vibrations in drivelines by moving the harmful resonance vibrations out of the operating speed range using a variety of stiffness levels of rubber or silicon, isolating torsional vibrations (engine from gearbox) and damping vibration amplitudes.
One example offered by Doug Sharrot, product group manager - highly flexible couplings, Voith Turbo Inc., shows a 6 dB reduction in the driveline at idle with the coupling installed.
"Torsional vibration stresses were almost six times the rated driving torque of the application before the coupling was installed," says Sharrot. "Had the system been operated without the coupling for any length of time, it could have experienced early shaft, bearing or gear tooth failures."
Foam insulators
An aftertreatment solution to NVH (protecting the operator from noise already released to the air) is a sound deadening or absorbing material. Standard plastics, foams and facing materials in cab interiors are being replaced by integrated composites that provide increased structural, acoustical and aesthetic value.
Underhood acoustical and heat issues created by Tier 3 and Tier 4 engines demand more technologically advanced materials to deal with these hotter and louder engines in tighter environments.
Federal Foam Technologies (FFT), New Richmond, WI, provides baseline testing, development and design services, and data-driven solutions. Its Sonus® materials are designed to withstand heat and deaden sound under the machine's hood and in the cab.
Sonus Sorb and Sonus Foam provide absorption to control pass-by (environmental) and operator ear noise issues. Sonus Flex offers a barrier between the cab and engine to reduce cab noise and provide vibration damping. Finally, the Sonus Temp materials combine absorption with enhanced heat-resistant characteristics for a more controlled environment.
FFT interior trim components combine Sonus Foam, Sonus Sorb and Sonus Tex materials to absorb sound that enters into the cab, while Sonus Flex barriers block external noise. FFT also offers porous moldable substrates that provide sound absorption, structural integrity and design flexibility.
Sound enclosures and blankets
Firwin Corp., North York, Ontario, Canada, supplies special sound insulation products and complex hot environment insulation solutions (temperatures up to 2,000 F) for installation on manifolds, turbo chargers, exhaust piping, silencers and purifiers. The products are made from foam composites, rock-wool panels and fiberglass with sound membranes, designed to limit equipment noise to acceptable levels.
Firwin supplies acoustic rock-wool panel liners for engine compartments and engine rooms, and mass loaded acoustic vinyl combined with foam decouplers/absorbers specially designed for engine enclosure liners and piping.
Where sound enclosures are not practical due to space considerations, special sound attenuation blankets can be manufactured. A combination of fiberglass mat for the higher frequency bands and membrane for lower frequency bands are used.
Standard blankets use 12 lb./cu.ft. of fiberglass insulation encased in a silicone impregnated fiberglass outer cover. To improve sound attenuation, especially in the higher Hertz range, loaded membranes are combined with the glass matt. Normally 2-in. thick blankets are used. Depending on the application and specific site restrictions, an overall noise reduction of up to 8-10 dB has been achieved.
Cab collaboration
While working with an OEM to design a cab, Randy Reinke, president, and Jim Schmitt, director of engineering and regulatory compliance, Custom Products of Litchfield Inc., Litchfield, MN, have a list of things to consider to reduce NVH.
Rubber isolated cab mounts absorb vibration, thus reducing noise. Curved or angled surfaces change the angle of incidence of a reflected sound wave, which will tend to diminish the strength of the sound wave (reduce noise), which is why a curved or angled windshield and window glass will deflect outside engine noise better than a flat panel on the cab.
Higher density, higher mass glazing will tend to deflect sound waves rather than allow the sound wave to pass through, or be actuated by the sound pressure and potentially amplify the unwanted sound. Glass mounting alternatives can improve or diminish acoustic performance.
Any source of noise should be kept as far away from the operator as possible, such as locating the engine exhaust systems away from cab, especially the windshield area. Machine design determines distance limits, so alternative engineering controls are applied to minimize the sound pressure level that is transmitted to the operator's area.
Minimizing mechanical controls that enter the cab such as levers, handles, and other controls that vibrate and generate noise is another common way to reduce in-cab noise. "Sometimes these controls protrude through slots to accommodate their travel. These gaps are difficult to close and not only will allow noise to enter, but dirt and dust as well," explains Schmitt.
Bair agrees, "Noise generated within the cab due to rattles of panels, knobs and shift levers are more important than they ever have been in driver comfort."
"The bottom line," says Schmitt, "is that generally the best acoustic performance is achieved when there is a collaborative effort between the machine designer and the cab designer."