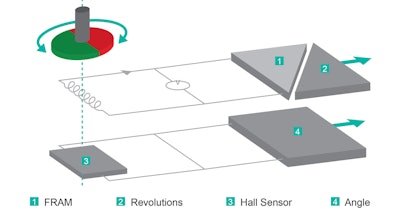
We always hear of how technologies advance, but rarely do we hear of an internal company structure advancing along with them. The FRABA Group (company information, 10114478), Heerlen, The Netherlands, made a daring decision back in 2004 to completely deconstruct its business model based on craftsmanship design and rebuild it in an industrialized fashion.
A craftsman process begins when an order is placed. A customer's specific requests are created, manufactured and the unique product is added to the existing product line. In terms of risk, a craftsmanship company model is a zero; it's a flexible system, but can also be inefficient. "A company should want to design an entire product portfolio strategically for a market, but with the craftsmanship model, a portfolio never develops because each project is taken on individually," says Christian Leeser, CEO of FRABA.
Another issue with the craftsmanship model is production. The craftsman is the intelligence behind the optimal production process. "We used to be a craftsman-centric company," says Leeser. "If we didn't have a specific part, our manufacturing team could find something similar in our inventory and modify it for the project. But, all of the unique production steps weren't documented for public use for future projects that may be able to benefit from the solution. The knowledge is in the craftsman's head and not known throughout the company, essentially lost to others that could leverage it working on similar projects."
With an industrial approach, a company must think in terms of strategic segments of its product offerings and what a particular market needs. "It's a much more complex process to end up with the types of products you want to design, and there is more risk involved. There are no orders to support your product line development, and the off-road industry is inherently low-volume. That's why many companies work in the craftsmanship model on an order-by-order customized design process. But, if you get it right, industrialized plants can be much more efficient," says Leeser.
Industrialized model in practice
With tens of thousands of encoder configurations available, the company knew it had to move away from the widely used model- or family-grouping structure of product lines. "The reason I think many in the industry utilize models to group their product offerings is a way to unify several similar products," says Leeser. "A single document can be for several products with similar features, and paperwork is a bit more simplified than trying to support documentation for each individual configuration of a product. This was the best way to document thousands of types of items with the paper-based system. You can't write 50,000 different product sheets, it's not economical, so companies group them."
Because of that, FRABA decided to move to a system that takes full advantage of computer technology. The company's product finder technology, an online searchable product database (product information, 10962925), helps to communicate all of its product configuration options. "Our product lines were designed from about 600 modules—parameters such as communication interface, shaft diameter, level of accuracy and level of resolution. We ensure the computer only shows the combined modules that make sense through a matrix that matches functional modules. By using the matrix, we end up with well over 50,000 encoder options along with all of the product information, spec sheets, pricing and manufacturing instructions for those configurations," says Leeser.
The same system that organizes the product finder also allows orders to be placed and has product assembly instructions tied directly to each configuration. A worker can scan a project, get the required parts from the warehouse, retrieve the manufacturing and assembly process instructions and begin to assemble the encoder order—whether skilled or unskilled. "Each module has instructions attached to it, so when a configured encoder is ordered, each piece of information for each module is available. That means we can literally set up shop anywhere in the world that has manufacturing space and product inventory," Leeser says.
"We are capable of lower cost production because we have unskilled labor, can produce anywhere and scale production easily because all we need to do to increase production volume is have the work stations and inventory. In the craftsman days, we had around 10 artisans, people trained in electrical engineering with an additional three years of experience producing encoders," says Leeser. "Imagine having only 10 main producers and your business is growing. It's very difficult to keep up with demand with a specialized labor force, especially if [the] bulk of your artisans are in Germany, for example, and you want to grow your business in the U.S."
The basic concept of FRABA's products is to use components that are designed for other high volume industries. For example, most of the company's Hall sensors are designed for the automotive industry. Accuracy and resolution requirements for automotive are lower than what FRABA needs, so they are tuned up in house, taking the standard 10-bits of accuracy and combining it with algorithms and processing power to 12 to 13-bits of accuracy.
"This is our design philosophy, which is contrary to what many sensor manufacturers do," Leeser says. For a long time, the golden rule of designing a sensor was to have a clear signal to properly handle the amount of information. "Our philosophy is different because we need to take out more information from bad signals and end up with the same accuracy. You don't need as clear of a signal if you have the processing power and intelligence to calculate from it."
From optical to magnetic
FRABA also recently launched its new line of magnetic encoders under its POSITAL brand, the IXARC encoders (product information, 11213443 and 11238942), to eventually replace the company's optical encoder product line. Depending on the model, IXARC encoders have resolutions of up to 16 bits per revolution and accuracy of 12 bits. They are equipped with a wide range of communication interfaces so they can be a cost-efficient alternative to existing optical systems.
With the exception of integrated servo motor feedback systems and a few other applications, there are no longer many compelling arguments to use shaft mounted optical encoders since their magnetic models offer the same functionality with advantages such as improved durability and a smaller footprint.
Magnetic technology can be much more tolerant of moisture, dust, grease and oil. Optical technology needs extreme precision; any dust or elemental obstructions can cause problems. Even if the optical encoder is shielded within a sealed housing, condensation from the air within the housing can still be problematic, so optical encoders commonly have issues in environments with sudden temperature fluctuations between hot and cold. Magnetic encoder performance is not affected by such elements. The IXARC encoders specifically are sealed to a IP69K rating.
"It has opened up some potential opportunities where optics don't work, such as machines that operate in hot and cold alternating climates," says Leeser. The applications and vehicles will be the same as optic encoders, but the range of environments that the machine can operate within will expand with magnetic technology. "With the mobile machine industry, you never know in which environment the machine will operate because it is always changing." The wider temperature range allows OEMs to potentially standardize the sensor on equipment instead of using regionally dependent sensor technology for extreme cold or hot areas.
"We used to be 100% optical. In 2007, we announced our intention to go to magnetic technology. We already had a magnetic product line before the IXARC encoder line, just not as powerful or as accurate as the new line. With the IXARC line, we extend that line to fully replace optics," Leeser says. "My feeling is that by the end of next year for every optical product, we'll have a magnetic product."
"We will continue to support the optic product line because we cannot make that decision for our customers. The magnetic sensors are drop-in replacements for the optic sensors, but often customers want tested and validated parts. Many times an OEM has just completed a design that includes optic sensors and that makes them hesitant to start the process all over again, to go through vehicle testing for component verification on the machine. That's why it will take a few innovation cycles before magnetic encoders are fully implemented and replace optics."
Inside the magnetic encoder
For linear actuators driven by electric motors, it typically takes a multiple turns of the motor to span the full linear range. This means that you need to know both the position of the shaft of the motor within one turn and the number of complete turns. In terms of absolute systems, the number of turns must include those that happen when there is no power to the machine. "You need to have power to run the electronics that store the information of the counter, or you need extra mechanical parts, so where does that power come from? You could use a battery, but batteries can be unpredictable," says Leeser.
If something has movement, there is power, and the energy of the movement can be induced. The energy harvesting technology within FRABA's magnetic encoder products consists of a wire with a special alloy treatment so all of the magnetic fields are pointed in one direction. As it crosses a threshold, the magnet flips over, and for that short period of time enough energy is generated to wake up the electronics and store the information. "The magnetic sensor detects the angular position of the shaft by measuring the direction of the magnetic field. The number of revolutions is recorded with a counter circuit powered by [an] energy harvesting system based on the Wiegand effect," says Leeser. "This absolute system records the position with one revolution, as well as the number of revolutions, even when external power has been interrupted." Signal processing is carried out by a 32 bit microcontroller.
"We were the first licensee of the multi-turn magnetics technology, and we were the first company with a product out harnessing it," says Leeser. FRABA isn't the only company that will be using the technology, but the company believes that its investment in its business structure will allow it to readily address market needs and meet customer demand better than its competitors. "It's high risk and high investment but also high reward," Leeser says.