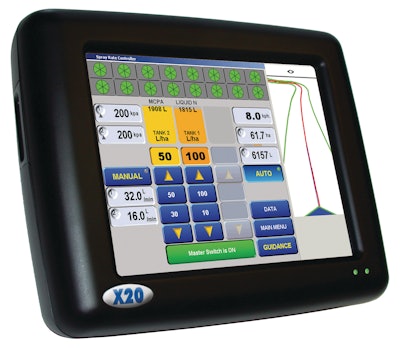
Simplification. The key to successful technology advancements. The more complicated the technology becomes, the harder it becomes to encourage OEMs to use it, and end-users to buy it.
The 2001 joint venture between two worldwide leaders, Topcon Positioning Systems (TPS), a developer and manufacturer of precision positioning equipment, and Sauer-Danfoss, a manufacturer of hydraulic and electronic control systems, form Topcon Sauer-Danfoss Integrated Controls (TSD). TSD has answered the call for easy-to-use, advanced machine automation technology "to make the complicated world in which their customers operate more simple."
Who is Topcon Sauer-Danfoss?
Ivan Di Federico, general manager of TSD, clarifies the role of the joint venture company: "TSD brings together a remarkable synergy of technologies and strengths between Sauer-Danfoss and Topcon. Sauer-Danfoss is a recognized leader by OEMs for hydraulic and electronic control systems and components. Topcon dominates the after-sales market of 3-D machine control and precision GPS positioning. The vast set of products that TSD can access through its parents represents a reliable combination of hydraulics, electronics and positioning technologies."
TSD brings together technologies such as hydraulic and electronic control, satellite-based positioning, inertial sensors and wireless communication into one completely integrated system. OEMs no longer have to spend time and money retrofitting their machines to equip themselves with the positioning equipment their customers demand. TSD has done all the complicated integration engineering work for them, saving precious time and money for the manufacturers. With Sauer-Danfoss as a complete control-system supplier working with Topcon positioning software, all of the parts work together.
Benefits were gained on all sides of the arrangement. TPS received direct relationships with manufacturers. Sauer-Danfoss gained access to all satellites involved with Topcon's advanced positioning system software. "The formation of TSD has allowed us to bring together the positioning technology from TPS (GPS and laser) with the machine control and application software experience from Sauer-Danfoss. Together, with the hydraulic expertise in Sauer-Danfoss, we can now control the machine all the way from the GPS signal to where the wheels meet the road," says Albert Zahalka, vice president of mobile electronics for Sauer-Danfoss.
The OEMs, working with TSD, can integrate specific components into their machines to create a unique piece of equipment that meets the specific demands of individual clients in a way that adds value around, and to, its other controls. "All OEMs like their automobile counterparts, want their machines to be unique, to feel different to drive," adds Zahalka.
Essential automation
Ray O'Connor, president and CEO of TPS, insists the "construction and agriculture industries are the two largest manufacturers in the world, where roads, buildings and bridges are manufactured and food is produced. The industries together make over $7 trillion a year," and machine automation is quickly becoming the best and most profitable tool to own in the industry.
Automation is essential for OEMs to sustain a competitive edge in the industry. With the technology available and already being used in the market, to avoid the technology is to avoid the inevitable progress already in motion. O'Connor warns, "If you don't have the technology, the bottom line is: You can't compete."
As the ability to find and maintain skilled operators decreases, automation becomes vital to making machines easier to operate while eliminating inefficiencies and waste in manufacturing processes. Automation technology allows an average operator to become a highly-skilled, fine-grade machine operator very quickly. The contractor is able to save time and money while increasing productivity, as an automated machine can handle materials efficiently and effectively, often at faster operating speeds. A single person can become a multi-tasking operator without feeling overworked or stressed.
Also to consider, in conditions of high wind, dust, or fog, when normal manual operation would have to shut down due to lack of visibility, the automated machine can continue working, regardless of the environmental issues. The project can move along smoothly allowing the contractor to stay on track, without losing time or money.
GPS also limits the amount of workers needed on the job site. Instead of a having one or more people physically observing for accuracy, the machine can now tell the drivers all they need to know. All the vital information is directly at their fingertips. Fewer workers equal less money and, more importantly, a safer job site for the workers and operators.
Michael Gomes, TSD product manager says, "The next step will be to have that information available via wireless technology to help assist management and operations personnel in making more informed operational decisions."
The future is here
Software enables us to simplify a process and move forward with progress and innovation. As users become more comfortable using technology, the software must remain easy to use.
Sauer-Danfoss' Zahalka comments, "The OEMs we serve in the off-highway markets are demanding more functionality and control of their vehicles, primarily in the form of electronic controls and software. Gone is the hydraulic control lever, replaced by sophisticated electronic joysticks with more functionality and superior performance. The differentiation for an OEM is now mainly driven by software. An example is the Sauer-Danfoss graphical programming tool PLUS+1 which allows an OEM to further customize and thus differentiate his machine."
PLUS+1 offers engineers an easy way to expand a machine's functionality by adding durable, stackable microcontrollers and modules. Using the PLUS+1 GUIDE (Graphical User Integrated Development Environment), the engineer can quickly build customized applications from Sauer-Danfoss' library of software control objects. Sauer-Danfoss' "plug and perform" platform reduces cost and development time normally associated with programming. Design engineers can use PLUS+1 to integrate control functions for their specific operating requirements "for almost any application, and everything they need is in one package," says Dan Ricklefs, product manager for Sauer-Danfoss.
Topcon's GPS+ can decipher and utilize both GPS and Russian GLONASS satellite signals, nearly doubling the amount of available satellites to users. The additional use of GLONASS' 20 satellites means global coverage, 24-hour operation, centimeter or better accuracy, with little to no down time, even in areas where standard GPS would falter.
The source is Topcon's Paradigm G3 chip containing a universal tracking device which allows the software to track all satellites and all signals. Its 72 universal channels track up to 36 signals simultaneously. This allows the tracking device to choose the best, most reliable signals available. The chip is fully equipped to accept signals from Europe's Galileo and any other future system. Topcon's O'Connor explains that those which use the GPS+ technology will be investing for the long run.
Many machine operators claim that using positioning technology isn't necessary to get the job done. But, those who try Topcon's GPS+ products quickly realize the benefits of the control and accuracy that can be achieved and how promptly a job can be finished.
A Topcon brochure cites a grading foreman for a construction company in Georgia who recalls the work before Topcon technology. Before, GPS+ technology, his crew had to have a stake and a hub every 50 ft. When he decided to change to Topcon's Millimeter GPS+, his crew was able to put a hub every 200 ft. cutting more than 50% of the time needed to do the job.
The accuracy that can be achieved using the GPS+ system can mean different benefits to different users. In construction, users reduce engineering costs, use and move less material and increase machine productivity. In agriculture, machine productivity is being increasing through wider implements, less overlap of material, better use of inputs and increased hours of productivity for equipment in critical time periods such as planting, spraying or harvesting.
TSD's Gomes says, with TPS software working together with Sauer-Danfoss equipment, figuring out how much material is needed for a particular project is very accurate. "Planning a job closely and accurately puts money in the customer's pocket — the contractors and farmers."
Topcon Positioning System's experience in 3-D control systems meshed with Sauer-Danfoss' machine control expertise creates "an array of possibilities for synergistic projects, including eliminating unnecessary timely and costly steps," says Gomes.
Ag infiltration
The TruPath system, a satellite-based, auto-steering system developed by TSD Integrated Controls, aims to bring repeatable centimeter accuracy to agricultural machinery. With the help of TruPath, which utilizes Topcon GPS+ technology and Sauer-Danfoss' steering units, farmers can work less, produce more and keep their competitive edge in the market.
TruPath is comprised of an integrated satellite receiver with inertial sensors that sense the machine's direction and acceleration. The receiver is connected to both a steering CAN bus system, as well as the ISO BUS system. This enables the operator to input commands and operate the system via a display that is as simple as a virtual terminal. Input received from the Topcon receiver and Sauer-Danfoss' steering wheel sensor is deciphered by the PVED-CL steering controller, and then compared to the feedback from the wheel sensor. The "talking" between systems by comparing data is what allows the machine to steer itself.
With the fully integrated GPS auto-steering technology offered by TSD, farmers can complete multiple jobs such as tilling, sowing and spraying in a single pass, saving fuel and time. They can confidently use wider implements without fear of potentially hazardous machine control, allowing them to cover more ground in a single pass and increase productivity.
In the past, rolling terrain and unpredictable weather conditions such as high winds could cause huge inaccuracies leading to wasted resources and possible damage to future production. TPS' software incorporates every bump and jostle into its program to automatically correct itself. Inefficiencies are eliminated without the operator having to take his focus away from his other tasks.
With the TruPath system, the average overlap is reduced from an industry average of 15 to 20% to less than 3%, and materials can be applied at a set variable rate eliminating waste and ultimately, saving money and material with positive environmental effects. And, the machinery can run accurately at all times of the day, in any conditions.
On the horizon
Recently, TPS acquired KEE Technologies Pty Ltd., a leading precision agricultural company based in Australia.
KEE provides users with a fully integrated control and monitoring solutions in a single-console system which allows farming equipment to be monitored and controlled in real time.
One result of the acquisition is the Topcon X20 console, an aftermarket product made by KEE. The X20 is a multi-tasking precision farming Windows-based computer. The monitor houses functions including communication, mapping, assisted steering, guidance, spraying, and boom control "which is probably a lot more than what most people want today," explains Gomes. Sauer-Danfoss helps supply TSD with numerous monitor options, so while you may not see many OEMs purchasing the entire X20 console suite, "you may see modules of the KEE-developed software becoming integrated into a machine at the OEM level" Gomes says. "Now, with all of the applications and all of the software pieces in one place, we can start to separate out and integrate those individual pieces for various OEMs as they want them."
"Every day manufacturers are fitting an ever-increasing number of machine control and GPS units to machines in the factory," O'Connor says. "We supply equipment to all major manufacturers of farming equipment, as well as to individual farmers.
Almost 50 OEMs and manufacturers install our equipment at the factory. The primary driver for the technology now is for farming operations concerned about waste of manpower and chemicals, doing their part to ensure a healthy environment, and drop more money to the bottom line."
Rhett Schildroth, TPS agriculture product manager, discusses field tests and farm application studies with the X20. The tests show that the guidance auto-steer, along with variable rate application and mapping function, has been documented to save 20% to 30% on fertilizer and chemicals, as well as more than 10% in fuel costs due to fewer passes.
Sauer-Danfoss' Zahalka and TPS' O'Connor agree on the future of machine control: "Eventually, technology will eliminate the operator, and in any case have more control," says Zahalka.
O'Connor, during the recent World Ag Expo, adds, "You're going to see, in the next five years, tractors and machinery operating on the farm that have no drivers. The agriculture industry will be the first robotically controlled industry in the world.
We're doing some of that today in the mining industry, a little bit in hazardous areas in construction industries, but the first mass market of that technology will be the agriculture industry. We, at Topcon, look forward to being a part of that future move forward."