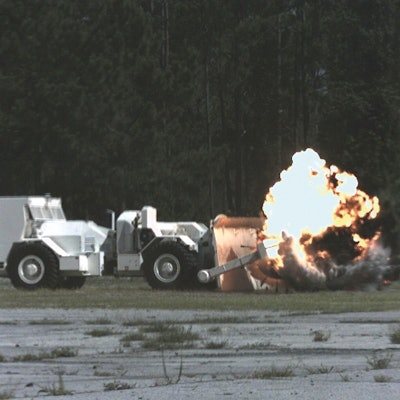
Old landmines are a serious problem in Afghanistan. According to the United Nations Mine Action Service (UNMAS), they kill or injure 100 people a month. An estimated 716 million square meters of land in 32 of the country's 34 provinces are affected. These hidden killers can seriously hinder development projects, both public and military.
"There are so many minefields in Afghanistan because of the number of years the country was occupied by Russia and then by the Taliban. It has made it tough to expand air bases because of the minefield potential," says Chief Master Sgt. Mark Lewis, chief of airfields for the 823rd Red Horse Squadron, the Rapid Engineer Deployable Heavy Operational Repair Squadron Engineers.
In order to remove landmines, the first Red Horse units were deployed with the Army in Afghanistan. "There were definitely some safety concerns. The job required two operators inside the cabin of the vehicle."
The operators are not bomb experts; they are Red Horse heavy equipment operators. "These guys aren't from an explosive ordnance disposal unit" the chief says. "They are pavement and construction equipment operators." They build roads, not diffuse landmines.
Air Force leaders decided to develop equipment that combat engineers could use to safely assist the Army and other services in mine clearing.
That's when the Air Force Research Laboratory (AFRL) at Tyndall Air Force Base in Florida got involved. Starting in August 2004, the lab, in conjunction with Red Horse troops, developed a system that could be completely operated via robotics. Machine operators now use laptop software and a control box to guide the vehicle through a deadly minefield.
The basis for the Red Horse machine is a mine clearing vehicle (MCV) developed by Hydrema, a construction equipment manufacturer in northern Denmark. When working in a potentially hazardous area, the articulated, 18-ton, hydrostatically controlled Hydrema 910 MCV-2 travels in reverse. A flail of chains with heavy carbide steel knuckles pummel the earth, detonating anti-personnel or anti-tank mines on contact. Two independent Perkins 1006-6TW six-cylinder diesel engines run the drive system and the flail. A heavy steel wall keeps the machine itself from becoming a victim. Hydrema's standard MCV has been used by the United States in Afghanistan since early 2002.
To build a robotic version of the MCV, AFRL took delivery of a new machine from Hydrema. After more than a year and $2 million to develop and perfect the system, the first fully functional MACV (for Mine Area Clearance Vehicle, pronounced "Mack-V") was scheduled to be deployed to Bagram Air Base, Afghanistan, this summer.
The MACV "is going to provide the Air Force — specifically Red Horse combat engineers — the opportunity to clear a known minefield or an unknown minefield to expand the air base or clear routes in a forward operating location," says Lewis.
Communication is key
During the development process, Representatives from Hydrema visited the Florida lab several times to provide technical insight of the machine's control systems. "To do the conversion, we went deep into the machine and we had to take a lot of things apart," says Walt Waltz, chief of AFRL's Robotics Research Group. The group is part of AFRL's Materials and Manufacturing Directorate, one of AFRL's 10 technology directorates. The remote system was developed by AFRL's Advanced Robotics Team using the Joint Architecture for Unmanned Systems.
The MACV sends back video data, while oil pressure and other information about the machine's health are fed to a laptop. MACV requires one operator, controlling both vehicle steering and monitoring the vehicle's gauges and the cameras. The biggest difference is that now he or she can be as far as a mile away from the vehicle.
"Typically commands make up your data set, but that is minimal. The biggest issue is video. You always want to have good video, as you don't want the machine to move without the picture being updated quickly. Video drives the cost of machine."
The Air Force is in the process of adding to its robotic fleet. The goal is to acquire enough vehicles with the remote control system so every active Red Horse unit will have two MACVs.
The system developed to make the robotic Hydrema MCV can be easily transferred to other machines. "We actually have it on several different platforms," says Waltz, including a six-wheel Land Tamer amphibious machine and a Polaris ATV. "You can build on the system. It's built with the future in mind. The limitations are only in your imagination."
In the field
The MACV operators will work in conjunction with explosive ordnance disposal technicians when doing mine clearing. "After using the MACV, you still have to come in with mine detection dogs or other manual means," says Lewis, "which means boots on the ground. The MACVs simply make it safer for everyone involved."
Besides making the area safer for the work crews, it also saves time. "Manual mine clearing is a very slow and tedious process," Lewis says. "So by having the robotic machine go in and flail the ground, that speeds up the initial clearing, which leads to faster construction."
The Red Horse squadron has nearly a dozen operators trained on the MACV, and it owns the pilot unit. "We're responsible for developing the standard operating procedures for the MACV," Lewis says. "Eventually, we'll develop a standardized lesson plan and study guide to train the other active duty units and even some of the Guard and Reserve Red Horse units."
The high-tech vehicle hasn't been that much of a challenge to learn for Red Horse troops. "This is the computer generation," Lewis says. "Today's younger Airmen are Gameboy and Nintendo experts, so it's pretty quick training for them."