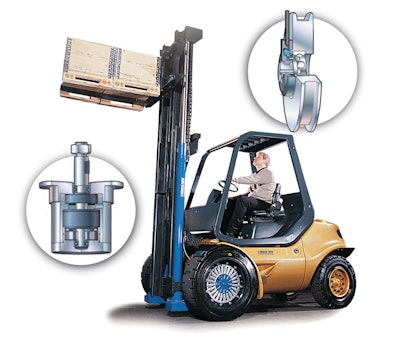
When SKF rolled out its concept "E-Truck" forklift, new possibilities were both imagined and realized from integrating mechanical and electronic technologies. Time has only accelerated interest in mechatronic solutions for off-highway vehicles.
Applications in the real world have moved forward. As an example, SKF has delivered an advanced mechatronic steering unit for Hamm AG's new series of DV tandem rollers. Hamm AG is one of the leading innovators in the field of compacting equipment for roads, airport runways, and bridges. The steer-by-wire unit is designed to improve the steering of the tandem roller machine and contribute to ergonomically comfortable working conditions for the driver.
Such a steer-by-wire module is only one of the "smart systems" engineered in the original all-electric concept forklift. Other key E-Truck components included electric actuators, which lift, tilt, and shift the mast and forks and tilt open the operator cab to expose the batteries; sensor bearings to communicate position, velocity, and acceleration feedback for the mast-height controller; and electric traction-motor wheels for propulsion, regenerative braking, and gearbox elimination.
Rolling out the all-electric E-Truck demonstrated how existing capabilities can eliminate hydraulics, reduce energy consumption, improve ergonomics for greater operator safety and comfort, and deliver new efficiencies and economies.
The concept was based largely on in-depth analysis of input from customers and end-users, who identified their needs for vehicle functionality and performance. Among OEMs, profitability remains top-of-mind.
OEMs continue to cite the need for products able to increase productivity and efficiency for end-users and promote product differentiation in the marketplace; perform reliably; and require simple maintenance. They confirm requirements for environmentally friendly products and express concerns about potential end-user exposure to hydraulic leaks or the exhaust of internal combustion engines. Operator safety (and the safety of surrounding workers) is paramount. And, in the quest to reduce manufacturing costs, OEMs strive toward more simplified and streamlined assembly procedures using fewer parts.
All these issues were addressed with the E-Truck concept, which began with a forklift truck stripped down to the frame. Existing systems were removed and the vehicle was rebuilt using an electromechanical steering system, actuators, mast height control, and direct-drive traction motors. Since then, many innovations incorporated into the concept forklift have found their way into OEM engineering departments and implemented for specific applications (such as the Hamm tandem rollers).
Among the more notable and available system and module technologies already brought to market are:
- Electro-hydraulic steering system. This combines the flexibility of electric steering with the power density of hydraulics. The system has its roots in the electromechanical model initially developed for the E-Truck.
The system factors out the steering column to enable more ergonomic steering solutions; reduce the number of parts; simplify assembly procedures and processes; and require less space. Without hydraulics in the steering column benefits can accrue in reduced noise; improved operator safety; decreased maintenance; and avoidance of hydraulic leaks.
The closed-loop system consists of a mechanical/electronic (mechatronic) steering module; a controller regulating all steering functions; kingpin bearing sensors featuring high resolution to achieve desired steering position input and actual steered wheel feedback; and electrically actuated proportional valve. Each component talks to the next using CAN-bus protocols.
When the operator turns the wheel, a signal is sent to the controller indicating the angle of the turn and the desired position of the wheels; the controller receives the operator's input and commands the proportioning valve to actuate; the valve actuates the hydraulic cylinder and forces the steered wheels to move to the position desired by the operator; the position sensor integrated into the kingpin measures the position of the steered wheels; and the feedback signal from the kingpin sensor is sent to the controller, where it is compared to the desired position input to correct any discrepancies.
The system can be programmed to adjust the number of turns for the steering wheel from lock-to-lock. Programming software further can govern steering sensitivity changes due to vehicle speed. This is especially noteworthy in operating off-road vehicles, when it is often necessary to steer quickly at low speeds and slowly at higher speeds.
- Mast height control unit. This can facilitate the automatic positioning of the mast on industrial vehicles and integrates a bearing with sensor electronics to detect mast height, speed, and acceleration.
Mast height control is particularly important to those operations demanding speed and accuracy from their operators. In these cases, a mast can be pre-programmed to a variety of shelf heights and, with the push of the button or the flip of a switch, the mast will automatically position itself to the desired height. This removes guesswork from the equation and helps operators work more efficiently and productively. When automatic height settings are not used, the mast height control system can provide an operator with a digital readout of the mast's height.
The control unit is mounted on the mast so that it can monitor its location as it travels up or down. As the mast is raised or lowered, the unit sends a continuous signal to the controller. These signals are interpreted into precise measurements. Using either a pre-programmed mast height system or a simple digital readout system, the vehicle "knows" the height of the load and can trigger other safety systems.
For example, the safety system could be programmed to limit speed or turning radius, depending on the height of the load. (This reduces the possibility of the vehicle tipping over.) Or the safety system can be set to prevent the mast from rising beyond a specified height when the load exceeds a predetermined weight.
Since their application in the E-Truck, two different designs have been engineered for mast control units. A spring-loaded cam arrangement uses spring force to press the sensorized bearing against the mast. This unit is driven directly by the moving frame of the mast. Pulley arrangement units are driven by either a wire or belt incorporated into the design of the mast-positioning system.
Both the cam and pulley control units respond directly to OEM needs for smaller components, simplified assembly, and reliable performance. The sensor technology is integrated into a very small bearing and the overall compact solution provides required strength to accommodate the typically encountered high loads in off-road vehicle applications.
Although most sensor bearings are inner-ring rotation, the one used for the mast height control unit is an outer-ring rotating unit. This proved to be more application-friendly and efficient from a design perspective and demonstrates the value of customization capabilities.
- Electromechanical actuators. In the E-Truck these replaced the hydraulic cylinders normally used to lift and tilt the mast and to move the fork carrier from side to side (side shift).
Ball screw actuators were specified for lifting and roller screw actuators for tilting and side shifting. They use a minimum amount of energy to raise a load and return a maximum amount of energy to the batteries when the actuators are lowered. The actuators are driven by an electric motor and the power is transmitted to the screw via a belt. (The side-shift actuator is a direct gear arrangement.)
Using actuators to replace hydraulics offers the advantages of quieter operation, elimination of environmentally damaging hydraulic fluid, and improved field of vision with the absence of hydraulic hoses.
- Sensor bearing units. These are key components in the progression of industrial vehicle technology and have enabled manufacturers to improve upon the performance of current mechanical systems and help reduce costs. Today's applications for industrial vehicles include systems for steering, mast height, position control, and motor control, among others.
Sensor bearing units (which integrate bearing function with sensor electronics) can detect shaft speed and acceleration, direction of rotation, and angular position. Their robust and simple design offers high signal accuracy and reliability, compactness, and ease of assembly.
They offer additional advantages in their uniform and high signal quality, minimal liability to interference, and low sensitivity to vibration or high temperatures.
A sensor bearing consists of a high-quality deep groove ball bearing; a magnetic impulse ring (or "code ring"); and two sensors with a body and connecting cable. The active sensor is shielded to protect against external electromagnetic influences, as well as moisture and the elements.
In operation the bearing unit's impulse ring moves past the stationary sensor ring when the inner ring rotates, generating a magnetic field of changing polarity. The sensor outputs a pulse, based on number of polarity changes per second. The sensor output signal then is transmitted via connecting cable to generate the required application-specific information. Speeds down to zero can be recorded.
These examples are among those that demonstrate technology has arrived to engineer electromechanical control systems and sophisticated electronics into a wide variety of off-highway vehicle applications, including forklift trucks, agricultural machines (harvesters and tractors), and mining and construction equipment.
By successfully merging mechanical and electronic technologies, solutions have been pioneered to meet OEM needs for improved reliability, increased operator efficiency, reduced maintenance, and energy efficiency. And by eliminating hydraulics, downsizing subassemblies, and decreasing energy consumption, industry has a bonus opportunity to further lighten the burden on the environment.
Timothy R. Ruiz is a business engineer for the Global Off Highway Segment of the SKF Industrial Div., Kulpsville, PA.