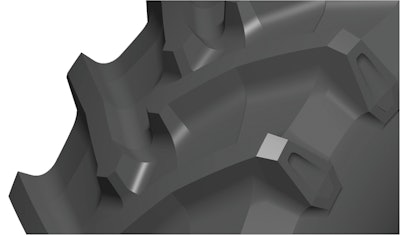
About a decade ago, the Brazilian sugarcane ethanol industry was still utilizing manual harvesting techniques to remove cane from the field. The process began by burning the entire field to remove dry leaves from the crop before the workers entered the field to harvest the cane by hand. But, during the burning process, the flash fires were causing significant air pollution and subsequent respiratory problems. “The sugarcane is harvested in Brazil between March and December, which is the dry season. In areas where sugarcane is heavily concentrated, a blue haze can be seen over the fields, which lingers because of the lack of rainfall to clean the air,” explains Michael Cordonnier, President of Soybean & Corn Advisor, Chicago, IL.
According to Federal Legislation of 1965, the use of fire for agriculture management was forbidden all over Brazil, however sugar mill owners were able to protest that there was not yet another viable technology at the time for harvesting, so the law was not applied to the sugarcane producers. As harvesting equipment and crop management tools continued to advance over the years—as well as with mounting community pressure to solve the environmental issues concerning crop burning—the government intervened and revised the legislation in 1998 to include sugarcane gradually, with complete burning elimination by 2021 in areas with slope under 12% (by 2031 in areas with slope above 12%).
In 2007, Sao Paulo and the Sugar Mill Association agreed to the Environmental Protocol which committed harvesters to the protection and recovery of vegetation around streams, a plan for soil conservation and water management, and a reduction of CO2 emissions by 2014. The Environmental Protocol is not a law, but rather an agreement, which means sugar mills and suppliers of cane are not obligated to follow it. “In some cities, burning is allowed when done at night or when humidity is above 30%,” says Leonardo Barbieri, Global Product Marketing Manager - Sugar Cane and Coffee Harvesters, Case IH (company information, 10630574), Sorocaba, Brazil.
The benefits to mechanical harvesting go beyond pollution reduction; a sugarcane grower will gain nutrients from the leaves left in place which introduces more organic matter into the soil, improves soil fertility and the sugarcane it produces, as well as reduces soil erosion. According to Cordonnier, the sugarcane crop is planted once and the same plant can be harvested once per year for six to seven years before the land is given a year off (referred to as renovating) and a new cane crop is planted. “If you were to keep burning off the leaves and taking away that nutrient source, you would essentially need more fertilizer for the soil, so mechanical harvesting shows promise for reducing fertilizer costs,” he claims. “There is about a 10% reduction in yield per year that a field is not renovated. But, when you renovate, you lose income for a year, so the government is trying to address that by offering low interest loans to sugarcane producers during their renovation year.” There is a drawback to the mechanical harvesters however, which is the reduced labor needs for the sugarcane harvesting process. By replacing a dozen workers in a field with a machine and a single operator, that’s a lot of people out of a job.
The Environmental Protocol addressed other challenges of mechanized harvesting that needed to be investigated. This included harvester production keeping up with demand, research to understand the production impacts of mechanized harvesting, and equipment improvements needed for more severe slope applications.
Case IH legacy companies’ first established its manufacturing location for agricultural equipment in Curitiba, Brazil in 1975. Now, Case IH has 107 dealers in Latin America and several manufacturing locations. In 1996, Case IH bough Austoft—the largest manufacturer of cane harvesters in the world—and later Brastoft, a Brazilian cane harvester manufacturer partially owned by Austoft.
All of Case IH’s Austoft cane harvesters serve the cane industry worldwide, explains Barbieri. When mechanized cane harvesting started in Australia, the equipment was being used on relatively flat land. Today, Brazil and other areas of the world produce cane in more hilly terrain, so the machines were developed to harvest in moderately unlevel areas. As the harvesters were being imported from Australia to Brazil to help meet the excessive demand after the mandate was put in place, a simplification of operator control was needed to match the skill level of the operators in Brazil who were used to simpler tractors.
Meet the machines
The Case IH Series 8000 Austoft sugarcane harvester comes in two models—the A8000 and the A8800—to handle different terrain types. The A8000 is equipped with tires for maneuverability and fast transport speeds of 12.4 mph on more level ground. For improved stability on sloped ground, the A8800 features tracks, which also reduce soil compaction.
Both models are equipped with a 353 hp engine with Smart Cruise technology to match engine speed with power demand for each condition of the sugarcane crop while it’s being harvested for optimized performance at all times. A digital engine function gauge delivers insight on engine speed, hours, coolant temperature, engine load and oil pressure with applicable engine error codes when necessary. The redesigned cooling package features a remote cooling module with rotary screen for reduced maintenance requirements and a mechanically driven fan from the engine crankshaft pulley for simplified operation. The cane that is removed from the coolers is ejected from the bottom of the screen and thrown clear of the harvester.
When it comes to harvesting equipment, the feeding system is essential to efficient production. Conditions such as strong winds, tangled cane and heavier varieties of sugarcane can present unique harvesting challenges, all of which were taken into consideration for Case IH’s feeder system. All 8000 Series Austoft cane harvesters come standard with a high-horsepower topper motor on the severing drum which offers 20% faster drum rpm and 44% higher motor horsepower from previous models.
Rotating toes at the base of the 45-degree crop dividers improve lift of down cane, as well as move less soil minimizing the amount of dirt pulled into the harvester which can cause unnecessary system wear.
A simplified hydraulic system is integrated with Case IH’s exclusive Auto Tracker automatic basecutter height system which automatically lowers or raises the harvester’s basecutter through sensors in the hydraulic suspension system. The system helps preserve the roots (stools) of the cane, which is extremely important to ensure a productive crop the next year. According to Case IH, the Auto Tracker system reduces the number of cane stools pulled out by the basecutter by 27.2% and at the row heads by 62.9%. The results affirm that the automated system improves basecutter operation to equal that of (or greater than) a skilled operator running the harvester manually, which speaks directly to the unskilled labor shortage problem found in Brazil and around the world.
In the end, a productive harvester provides the most crop yield. Excess straw can cause losses in the production of sugar and Ethanol. Case IH’s Anti-Vortex cleaning system on its 8000 Series harvesters separates trash from cane billets and deposits the trash behind the machine. The design, as the system’s name implies, reduces vortex effect while reducing cane losses by up to 50% and operating power by 30 hp for more efficient fuel consumption with increased productivity and crop quality.
Industry growth expectations
Case IH sees the harvester equipment market in Brazil as an area of growth. According to Barbieri, Case IH has an optimistic industry forecast for 2013 and 2014 with total volume at the same levels of 2010 before the financial crisis. Case New Holland (CNH), parent company to Case IH, sees Brazil as a continually developing agricultural market with growth potential in harvesting equipment. “Scientists say that one third of the world’s food in the year 2030 will be produced in Brazil,” Barbieri says.
“The second harvest in Brazil has become as important as the first one to use soil resources and weather conditions more effectively,” he continues. “Therefore, the period left for harvesting has been reduced gradually to enable the second crop within the agricultural year. And the advancements that have been made in inputs such as GMO seeds, fertilizers and crop protection, as well as crop management have led to increasing yields in all Brazilian cash grain (corn and soybean) production regions.” Labor legislation is pushing for training to get machine operators up to speed with the newest machinery technologies. All of these opportunities are favorable to the agriculture machinery manufacturer and will likely encourage demand for higher performance machines for more productive crop harvesting with lower operation time.
As the Brazilian sugarcane market continues to develop and accept more advanced equipment, the increased productivity and yield of the cane crop will be a contributing factor for the long-term likelihood of sugarcane ethanol as an export.