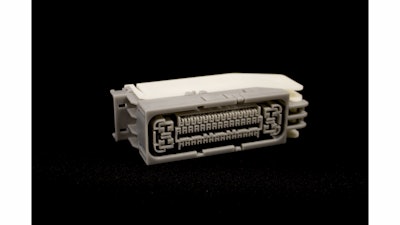
Though it may seem as if 3D printing is the “new kid on the block” in the manufacturing world, the technology has actually been around since the 1980s. Chuck Hull, founder of 3D Systems Inc. (company information, 12006241), is credited with being one of the first to commercialize the technology after inventing a type of 3D printing known as Stereolithography in 1983.
Three-dimensional (3D) printing is a form of additive manufacturing which creates 3D objects by continuously layering material until the object is fully formed. The item being printed is typically first created in CAD software where the design can be easily manipulated and validated. Once a 3D model is created, the file is transferred to the computer controlling the printer and the printer goes to work building the object.
Use of 3D printers has continued to increase as manufacturers have seen the time and cost savings associated with 3D printing, as well as found new ways to utilize the technology. In addition, improvements to the printing technology and the materials it uses has helped bring down the cost, further expanding its use within various industries.
According to Tom Charron, Vice President of Product Marketing at 3D Systems, the industrial B2B side of the business makes up 90% of the company's revenue. “Last year printer revenue in these categories grew more than 50% and approximately half of the professional and production 3D printers go into outright manufacturing applications,” he says, “and we expect that number to continue to grow.”
Time and cost savings
One of the biggest benefits manufacturers have seen from using 3D printers has been a reduction in time and cost associated with prototyping. During a recent webinar hosted by 3D Systems, Daniel Copley, R&D Manager at Parker Hannifin, Racor Division (company information, 10055895) explained how 3D printing has become a key part of the company’s new product development process.
Copley said the company has invested in several in-house 3D printing technologies which enable it to create prototypes within one to two days versus weeks and has also put prototyping costs into the $100’s, whereas outsourcing the printing of the prototype can cost into the $1,000’s. “For a design engineer, it’s fantastic to get your part in hand, be able to look at your concept idea and be able to experiment with it,” stated Copley.
With the 3D printed model, engineers can test and validate their design, and make any necessary changes at a minimal cost. This helps ensure the most optimized design is reached before going into the production tooling phase of the design process, which Copley said can take anywhere from 4 to 6 months and cost $100,000’s or more. Making even the simplest of changes at this stage could cost anywhere between $10,000 and $50,000, versus the $100s it costs to make another prototype in house. Copley estimated Racor has been able to save about $250,000 per year on prototypes due to its in-house 3D printing capabilities.
When Racor wanted to make changes to a new diesel engine blow-by filter for a customer on a tight deadline, Copley said 3D printing allowed the company to create a prototype and validate its design within three weeks. For the project, Racor chose a 3D Systems Stereolithography apparatus (SLA). The printer enables Racor to print large filter designs, and use a high temperature material called Accura 48HT to create working prototypes that can actually be tested on systems such as an engine.
According to Copley, the Accura 48HT material has a temperature resistance of 130 C which allowed Racor to test the filter by using oil heated to actual engine operating temperatures. With this material Racor was also able to create a clear, see-through prototype filter assembly that allowed the engineers to observe oil flow through the filter and better predict the effect of potential design changes. In addition, the Accura 48HT features a high print resolution which Copley said enabled the creation of small, highly detailed components to provide Racor with a functional prototype very similar to that of a production tooled filter.
More than just prototyping
Charron says one of the biggest challenges currently facing 3D printing is raising awareness of its capabilities. “A large number of engineers and manufacturers still do not use 3D printing technology…this could be due to the lingering misconception that 3D printing is only useful for prototyping or concept models, and that’s simply not the case.”
Copley said during the webinar the industry is going through a rebranding of what additive manufacturing means to better encompass what can be done with 3D printers.
He went on to say that Racor has found many uses for the technology beyond creating a physical prototype. Depending on the type of material used with the printer, Racor has been able to test its prototypes both in the laboratory and directly on engines. This helps ensure the functionalities of the filter are verified and the company is creating the most optimized design.
Its use of 3D printers has also helped the company take the manufacturing process into consideration early on in filter design to make sure the component can only be assembled in one way and that it will be quick and easy to produce. Copley said this helps save time and money by ensuring the product is ready for manufacturing before purchasing costly production tool and manufacturing equipment.
Racor continues to find new uses for its 3D printers, said Copley, such as using them to print molds that are used for making urethane filter seals. Once a mold wears out, a new one can easily be made at a price of about $300 or $400 each, whereas buying the molds costs between $3,000 and $4,000. The company has also been able to make custom designed fixtures to help make the assembly process easier during manufacturing.
Charron says 3D Systems’ latest SLA machines are capable of creating casting patterns as large as an engine block in significantly less time than traditional pattern making. “And Selective Laser Sintering can also be used in applications for end-use parts, housings and robust test parts.”
Growing use of materials
Plastic is one of the most typically used materials for 3D printing, though the use of ceramics, metals and recyclable materials have increased within recent years. For companies such as Directed Manufacturing—which makes prototypes and production parts using 3D printers—the more options of material types that can be used with 3D printers has enabled broader production capabilities and availability of products for customers.
Directed Manufacturing added a metal printer to its manufacturing facility in 2012, becoming the first U.S. commercial user of Renishaw Inc.’s (company information, 10056027) AM250 laser melting additive manufacturing machine. With this system, Directed Manufacturing has been able to create parts for its customers in a variety of metals including aluminum, cobalt-chrome, stainless steel and titanium. And if a customer requires a new material, the system’s open architecture allows the company to develop and customize the machine’s parameters to print parts from that new, specified material. Visit www.oemoffhighway.com/12006668 to learn more about how Directed Manufacturing is incorporating metal 3D printing into its business.
“Our direct metal 3D printing is a huge development that’s allowing manufacturers to produce tool-free, highly complex, chemically pure metal parts in significantly less time,” says 3D Systems’ Charron. “Material advances also allow us to directly produce robust tooling for hydroforming, molds and more, in as little as a few hours, so manufacturers can skip the sometimes elongated process of traditional tooling and go straight to primary manufacturing.”
Graphene is one of the next materials being investigated for use with 3D printers. Considered to be the strongest and thinnest material known to man, graphene is composed of a single lager of carbon atoms and has been found to conduct electricity 30 times faster than silicon. It is also a transparent and bendable material.
Because of its many advantageous properties, graphene has the potential to be used in various products including electronics and supercapacitors. Many within the materials industry also believe graphene could be used in place of steel in the aerospace, defense and automotive industries to provide components with increased strength, reduced weight and better fuel efficiency.
Graphene 3D Lab Inc. and Graphene Technologies are two companies currently developing graphene materials for use with 3D printers. In September, Graphene 3D announced a joint venture with Stony Brook University to test the functional and mechanical properties of 3D printed parts made with graphene-enhanced materials (learn more, 12006697). Through this joint venture, Stony Brook University will provide an impartial review of how the graphene material performs in 3D printing, as well as report on what the optimal printing conditions would be for the material.
Graphene Technologies is working with 3D printer manufacturer Stratasys Ltd. (company information, 12006043) to develop advanced structural 3D printing ink that will be made using Graphene Technologies’ graphene and nano-dielectric co-product magnesium oxide products. The Israel-U.S. Binational Industrial Research and Development Foundation recently provided the two companies with a development grant for this project (learn more, 12006660).
Making graphene material available for 3D printing would be beneficial for manufacturers as they continue to focus their efforts on finding new methods for light weighting. Its availability could also help expand the use of 3D printing even further by having more materials available for manufacturers.
As the types of materials available for 3D printing continues to evolve, so will the technology. Charron says the technology will keep getting better in terms of increased build volumes and speed, as well as becoming even easier to use. “We’re only at the tip of the iceberg,” says Charron. “In the coming years and decades, we’ll see designers and engineers get more accustomed to designing for 3D printing and embracing the unique geometry capabilities that the technology has to offer.”