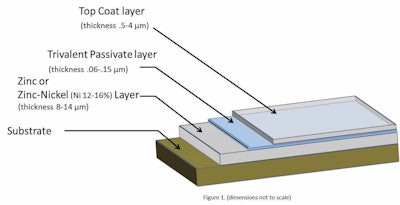
Off-road vehicles, from construction equipment and agricultural machinery to maintenance vehicles for electrical power wires, telephone lines and video cables are significantly more subject to corrosive attack than on-road and in-plant vehicles. Construction vehicles, such as excavators and bulldozers, in addition to operating outdoors, often sit idle and exposed to the weather between projects. Agricultural equipment is exposed to corrosive chemical fertilizers and herbicides.
But when they are needed, these vehicles must spring into action and work for hours, days and weeks on end in conditions that can produce extreme wear and thermal stress. They must operate at high rates of productivity, and maintenance often needs to be postponed because the equipment cannot be spared from working to meet demanding deadlines.
These factors make off-road vehicles especially good candidates for having their critical parts electroplated with a Zinc-Nickel (Zn-Ni) coating that offers superior protection against the corrosion and wear stresses that will otherwise shorten their productive lives.
Protecting off-road vehicles with electroplated coatings presents unique challenges, since they are often larger and more complex than on-road and in-plant vehicles. As a result, companies exploring this added protection for their vehicles need to evaluate electroplating suppliers carefully to evaluate not only their experience with Zn-Ni coatings, and experience coating large complex parts, but also the physical capabilities they offer. Few electroplaters, for example, have large enough electroplating tanks to accommodate the large booms, lifts and component assemblies of off-road equipment.
Electroplated Zinc-Nickel alloys coatings
The development and practical application of electroplated Zn-Ni alloy coatings began during the 1980s, and its acceptance and use have grown slowly but consistently ever since. But, like many innovations that are introduced and gradually accepted into design concepts and manufacturing processes, these coatings have not been as widely implemented as other traditional protective coatings.
This is unfortunate, because while the process and the benefits it brings are subject to some misconceptions, Zn-Ni coating offers the manufacturers of off-road vehicles a valuable tool for not only protecting and extending the working life of their equipment, but also for meeting ever-increasing regulatory, warranty and performance requirements. These coatings have already been extensively adopted by the aerospace and automotive industries, but have yet to be widely used for the off-road heavy construction, mining and agricultural equipment that is routinely exposed to harsh environments that can result in excessive corrosion.
The benefits of Zinc-Nickel alloy coating
An electroplated Zn-Ni alloy coating (composed of approximately 85% Zinc and 15% Nickel) is applied as a protective coating to carbon steel. It is applied to the substrate in a similar way as a Zinc coating, and the coating has a similar structure to that of a zinc coating: a thin (8-14 mm) layer of 12-16% Nickel alloy next to the substrate, topped by a 0.06-1.0 mm trivalent passivate layer and a 0.5-4.0 mm top coat layer. (See Fig 1). Figure 1: Typical Zinc and Zinc-Nickel plating layers
There the similarities end: the Zn-Ni alloy coating significantly exceeds the protection offered by other coatings in two main ways: it offers greater corrosion protection and increased wear resistance for moving parts.
The following is a brief summary of Zn-Ni benefits:
Corrosion protection
As a true alloy, Zn-Ni coating technology has been proven to provide two to three times more corrosion-resistant protection than that, for example, of a 16% Nickel co-deposit. (See Fig. 2). Figure 2: Neutral Salt Spray comparison chart for Zinc and Zinc-Nickel coatings.
Zn-Ni coatings are especially effective against corrosion. In SAE J2334 Cyclic Corrosion tests (See Fig 3.), a much more stringent test than a simple salt test, parts coated with Zn-Ni outperformed Zinc-coated parts by a factor of four. This level of protection on the critical parts of an excavator or a combine can extend its working life by years. Figure 3: Cyclic corrosion resistance comparison between Zinc and Zinc-Nickel coatings.
Increased wear resistance
A hard, thin film coating with a consistently smooth finish Zn-Ni alloy coating increases wear resistance both through the hardness of its finish and by producing a surface that virtually eliminates irregularities, significantly reducing opportunities for abrasion–one of the main sources of surface damage to coatings on off-road vehicles, opening the door to corrosion. On the Vickers hardness scale, (See Fig. 4) parts coated with Zn-Ni alloy reached 450, compared to less than 150 for Zinc-coated parts. Figure 4: Hardness comparison between Zinc and Zinc-Nickel coatings.
Laboratory tests have shown that electroplated Zn-Ni alloy coating offers a unique set of beneficial qualities not found in other electroplated or traditionally-applied coatings. Real-time field experience has shown that these qualities can play a significant part in extending the life cycle of equipment.
In addition, the smooth, hard, consistent surface finish of Zn-Ni coating continues to provide excellent corrosion protection even for components that have been formed or bent following coating. They also provide an excellent base over which paint or powder coating finishes can be applied.
Successful Zinc-Nickel coating applications
Being able to provide a much higher degree of substrate protection means that Zn-Ni alloy coatings can play a major role in reducing the effects of many of the stresses that inevitably shorten the working life of a wide range of off-road equipment. The automotive manufacturing and aerospace industries are already adopting these coatings. Manufacturers of construction and agricultural equipment and other off-road equipment are only now beginning to see the potential advantage of adopting them to protect the value of their products.
Automotive and truck manufacturers have used Zn-Ni alloy coating’s ability to increase wear resistance on moving vehicle parts, a critical factor in extending the working life of parts that experience consistent wear stress, yet must perform successfully––such as brake calipers. This benefit will be even more important for parts on off-road vehicles that work extended hours without maintenance.
Zn-Ni coatings have been applied to a wide range of the most exposed parts of off-road equipment, from control boxes that protect the electronic controls for boom lifts, scissor lifts and other working booms to the booms themselves. Control boxes have been traditionally powder-coated or painted–a protection that is easily scratched or scraped off, exposing the box to corrosion. An undercoating of electroplated Zn-Ni protects the cabinet further, protecting the controls as corrosion penetrates the paint and threatens the integrity of the box itself.
Zn-Ni coating protects not only because it forms a hard, resistant layer of protection, but also because, as paint or powder coating surfaces are penetrated, Zn-Ni acts as a sacrificial coating: it will corrode before the underlying steel begins to corrode. This extends the working life of the coated component by significantly delaying deeper corrosion.
Equipment booms and lift arms are continually subject to external contact that scrapes through paint, as are also the safety cages on electrical equipment maintenance aerial lifts. Manual and hydraulic lift gates are easily scraped during loading.
Larger components, such as the boom arms of backhoes and excavators probably take more of a beating than any other construction equipment. They are almost continuously subject to scrapes and scratches as they operate, then sit exposed to weather when they are not.
For much off-road equipment, including agricultural equipment and mining trucks, while the main body of the piece of equipment might be adequately protected from weather by paint or powder coating, it is the working parts that contact the soil and the corrosive chemical fertilizers and herbicides it contains, or the truck beds and gates that directly contact minerals and ores that face the greatest stresses. Because they face greater stresses, they are the most likely candidates for the superior protection provided by Zn-Ni coating.
How electroplated Zn-Ni coatings are applied
Components and assemblies to be electroplated are placed in a tank containing a chemical bath, and an electric current passing through the bath deposits the Zn-Ni alloy directly on the metal component. This creates a bond much stronger than that of traditional paint or powder coating application, but which also provides a secure base to which paint or powder coating can be applied to produce a desired brand image. It also provides a much more even coating than alternative protective procedures, such as hot-dipped galvanizing, for example, which can result in uneven coverage that requires later smoothing operations.
Smaller components, such as control boxes or parts of equipment assemblies, are hung from racks during the electroplating process. These pieces are thoroughly cleaned beforehand, including all welds; hollow components, such as arms and tubes, are provided with drain holes to prevent chemicals being trapped inside.
Gatto electronics enclosures for lift equipment.
An experienced electroplating facility will carefully hang these parts and components so that they receive maximum exposure to the tank’s anodes, ensuring complete coating protection. The Gatto facility is unique in that it includes among its multiple tanks a very large tank (27 ft. long) that can electroplate large parts such as booms, lift arms and safety cage assemblies without disassembling them, resulting in a superior coating result while simultaneously controlling coating time and cost.
For further information, contact Gatto Industrial Platers at 866-623-9634, or visit www.gattoplaters.com.