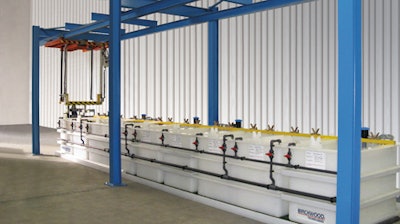
Confirming the growing trend toward less hazardous part finishing, a leading hand tool manufacturer has recently converted a third manufacturing plant to the TRU TEMP low temp black oxide process, according to Birchwood Technologies.
“These conversions prove the positive impact that the TRU TEMP process has on finish quality, turnaround time, worker safety and cost,” reports Jesse Vouk, Sales and Marketing Manager for Birchwood Technologies. “This customer is committed to the highest quality black finish possible, performed in-house for fast turnaround, while eliminating the hazards of the old hot oxide process. One by one, as each TRU TEMP system proved itself, another installation was slated for conversion.”
Being a brand leader means that finish quality must be consistently high. To meet those requirements, the TRU TEMP process produces a durable, satin black magnetite coating, 20 millionths thick (0.5 micron), with excellent corrosion resistance and appearance and no effect on the hand tools’ material hardness or tensile strength. The TRU TEMP finish is fully compliant with the prevailing Mil Specs, RoHS and ELV requirements. Customer acceptance has been high, as the finish provides long term protection for overseas shipping and dealer warehouse storage.
Worker safety is of paramount importance for this customer, who has struggled in the past to control the frequent splattering and boil-overs common with other blackeners operating at temperatures as high as 240 to 290 degrees. Because the patented TRU TEMP bath operates at 200 to 205 degrees (well below the boiling point), these boil-overs have been eliminated. Overall finish quality and worker safety has improved while brown coatings and reworks have been eliminated.
Process line conversion was easy. The customer was able to install the TRU TEMP process in the existing tank line, with minimal capital outlay. The tanks were cleaned, the hoist re-programmed, and full production began immediately, with on-site training by Birchwood Technologies’ factory personnel. An added benefit is the elimination of outside black oxide finishing. This work can now be brought back in-house for TRU TEMP black oxide, thereby lowering costs. Improved process consistency and elimination of reworks has tripled process line throughput, and has streamlined workflow patterns in adjoining departments, as well.
Cost studies have shown that the TRU TEMP process has an operating cost that is about the same as that of the high temp black oxide when chemicals, labor, energy, maintenance and reworks are taken into account.
Bottom line for this manufacturer: the TRU TEMP finish enhances overall quality and visual appeal of the customer’s hand tools while improving worker safety and lowering costs, thereby allowing the tools to be marketed as premium grade products, while maintaining competitive pricing.
“These installations are noteworthy,” Vouk believes, “because they reflect the industry trend toward continual upgrading of manufacturing processes in an environmentally responsible manner. Since the TRU TEMP process contains no EPA regulated chemicals, the rinse waters are generally sewerable as non-hazardous discharge, with no need for waste treatment in most areas. This benefit simplifies the installation and minimizes the capital cost of removing polluting processes from the premises.”
To minimize rinse water consumption, the TRU TEMP process can be configured to utilize the NEAR-ZERO Water Recycler system which re-uses the rinse waters with a 90+% reduction in water usage.