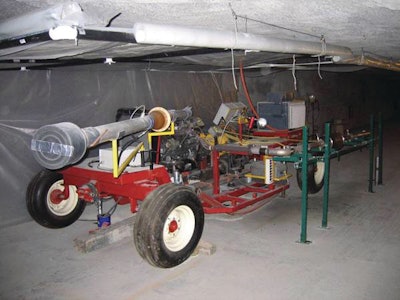
Emissions regulations are definitely not a new topic in the on- and off-highway equipment industries. Engine and equipment manufacturers have poured millions of dollars into laboratory and test facility updates, product research and development, testing, and manufacturing of diesel particulate matter reducing technologies and other aftertreatment devices. Equipment manufacturers have redesigned machines repeatedly to accommodate for larger engine system packages, where space was already at a premium.
Underground mining specifically is unique to the challenges of combating emissions because of the tight constraints of the engine package and the equipment itself within the narrow underground mine drifts. The limited space also means that the emissions released into the air are more contained and cannot dissipate into the air as easily as equipment running in an open environment.
Government regulation
Steve Mischler is the team leader in the Dust Control, Ventilation and Toxic Substances Branch, Office of Mine Safety and Health Research (OMSHR), National Institute for Occupational Safety and Health (NIOSH) an agency within the Center for Disease Control. His group looks for ways to monitor and control diesel emissions, both particulate matter and in the gaseous form, among other responsibilities and areas of focus. “As a government research facility, we work to reduce occupational exposure,” he says. “We work with manufacturers as often as we can to find and help solve the issues they are dealing with within the mining industry.”
Mischler’s group looks at any and all technologies available for diesel particulate matter (DPM) reduction efforts. The Mine Safety and Health Administration’s (MSHA) regulatory standard for DPM concentration limit is 160 micrograms per cubic meter of total carbon. The standard went into effect May 20, 2008.
According to a document released by MSHA in September of 2006 entitled “Metal and Nonmetal Diesel Particulate Matter”:
DPM is a component of diesel exhaust. DPM includes diesel soot and solid aerosols such as organic carbon compounds, ash, metallic abrasion particles, sulfates and silicates. The majority of diesel exhaust particles are less than 1.0 µm in size. Diesel soot particles have a solid core mainly consisting of elemental carbon, with a wide variety of other substances attached to the surface.
Exposure to high concentrations of DPM can result in a variety of serious adverse health effects. These health effects have been found to include: (i) sensory irritations and respiratory symptoms serious enough to distract or disable miners; (ii) premature death from cardiovascular, cardiopulmonary, or respiratory causes; and (iii) lung cancer.
“When you attempt to implement DPM control strategies,” says Mischler, “each mine is an individual. Often when one DPM control technology works in a mine, it may not work in another.” For example, the use of biodiesel to reduce particulate emissions works well in locations where the ambient temperature is warmer; however, if biodiesel is used in a machine that is running in a below-freezing environment, the fuel can congeal and become difficult for the engine to handle.
Current solutions
There are plenty of technologies currently in place that effectively reduce the amount of particulate matter and toxic gasses. Selective catalytic reduction (SCR) systems, diesel oxidation catalysts (DOCs) and diesel particulate filters (DPFs) are just a few examples.
“We know that diesel particulate filters will filter a large amount of the particulates coming out of an engine. They’re over 90% efficient and do a nice job of reducing diesel particulates in a mine, but they also have issues,” Mischler explains. While DPM accumulation does make the filter more effective at removing particulates, as more accumulates it will eventually plug the system causing the engine to shutdown.
Besides the necessary regeneration process for a DPF system, technologies used in underground mining also have to be aware of the amount of nitrogen dioxide (NO2) released into the air. “On-highway DPF technology utilizes catalysts to coat the filter material. The catalysts enable the soot to burn off via chemical reaction, but the use of catalysts may also result in the formation of NO2 which is a health hazard,” he says.
In an enclosed space such as a mine, workers should be concerned about any increase in the amount of NO2. “When we put these control technologies into the mining industry, we have to ensure that the DPM control technology does not result in an increase in NO2 concentrations to above levels established in mining regulations.”
Cutting-edge, cutting DPM
AirFlow Catalyst Systems Inc. of Rochester, NY, specializes in the development of catalyst technology. Its EZCat™ DPM and gaseous emissions (hydrocarbons, carbon monoxide, and NOx) reduction system for diesel exhaust systems is a continuously regenerating, passive system based on a low temperature chemical reaction, especially well-suited for underground mining.
Unlike common DPM reduction systems, the EZCat system does not require a DOC or a filter pack. Heat exchangers are unnecessary, though should an operator choose to use one with the EZCat system, it would require no cleaning. The simplified system hinges on AirFlow’s continuously regenerating soot trap, which uses low amounts of precious metals allowing for a low temperature chemical reaction that eliminates soot particles before they form. The system thus has no need for a physical filter device.
“In mining there are two critical things people want to clean up from the diesel exhaust. One is carbon monoxide (CO), and one is the soot itself. A DOC is meant to clean up the CO, while the soot has to be collected mechanically via a filter device and cleaned later,” explains Zaki Mustafa, president, AirFlow.
“What our system has done is combined the function of CO removal and soot removal into one unit, so we don’t have a DOC or a filter pack. The unit removes CO and chemically transforms carbon soot into gaseous exhaust before it reaches a solid state, and therefore needs no mechanical device to collect any particulates.” All of this is done while containing NO2 within the regulated parameters.
Paper filters on other technologies catch soot particles, which causes build-up and then back pressure on the system. “When our system is running, the soot never forms at all. It is in the gas state and removed before it ever becomes soot,” explains John Belgiorno, sales and marketing for North America, AirFlow. The company has EZCat systems running for over 11 months and logging over 2,000 hours without any cleaning or downtime.
The development of the EZCat technology was made possible by low light-off temperatures of the washcoat, covering the entire range of idling to full load operation. Back pressure is controlled by an in-house proprietary technique of coating the washcoat on support material.
The EZCat system can fit in a small compartment, an important issue for underground mining equipment manufacturers. The absence of a filter pack offers significant maintenance, labor and materials savings. The time spent replacing filters is eliminated, as is the cost of purchasing the replacement filters. AirFlow suggests that maintenance, materials and labor savings annually can be as much as $50,000—potentially more with downtime eliminated.
The system has been listed on MSHA’s website of acceptable emission filter devices. MSHA’s test validated that the EZCat system offered 93% efficiency for collecting DPM (7.69-30 CFR, ISO 8 mode test).
Additional NIOSH studies: