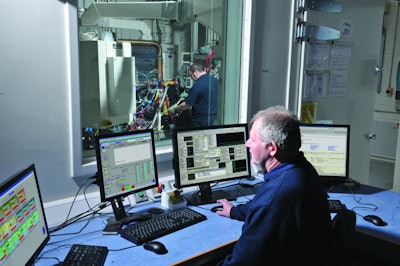
Over the last three years Perkins has installed 12 new validation cells, a tilt cell and upgraded five existing cells at its Global Engine Development center (GED).
The facility, which allows Perkins to put its latest Tier 4 engines through the most stringent validation tests, follows on from the company’s investment in a world-class crankshaft machining center at Peterborough, which opened in November 2009.
“Three years ago this facility upgrade was a significant announcement. Today it is a significant reality,” says Perkins president Gwenne Henricks.
“And I believe it is significant for a number of reasons; it is a reflection on the quality and capability of this plant; it ensures a stronger future for our employees; it provides our customers with better quality engines using processes that are quicker and consume less energy; and importantly it sends out a very strong message that this business remains at the forefront of engine design, manufacture and delivery.”
GED has approximately 50 test cells and additional specialist cells undertaking a variety of complex validation tests, including performance and emissions, mechanical development, endurance and transient development.
Robin Woodward, general manager GED says, “We wanted to create a highly flexible testing center able to support our long-term needs. The new cells will have a significant additional capability and will enable us to develop and test our engines so that they are truly customer and application specific.”
By investing in a state-of-the-art facility, rather than outsourcing large parts of its test program, Perkins will have greater control over timing and thereby will be able to serve its customer base more effectively.
“This facility will give our customers the best delivered quality yet,” Woodward says. “The new cells will enable us to replicate the way customer machines work, which lessens the amount of time we need to spend testing in the field, meaning that we can do it far faster than ever before. We can also operate these cells 24 hours a day and with greater efficiencies, so our customers not only get their engines quicker, but the engines are validated for their specific requirements.”
In addition to customer benefits, the new cells also enable Perkins to meet one of its key business goals of reducing the impact it has on the environment.
“This facility also helps meet our long-term aim of reducing our carbon footprint,” Henricks says. “Currently three of the test cells can regenerate electricity back to a substation which reduces our site dependence on the grid. This means we can save an anticipated 500 megawatt hours of electricity per year; that’s the equivalent of 272 tons of carbon dioxide. It’s an encouraging start and by adding more of the regenerative technology to the cells over time we can increase this figure.”