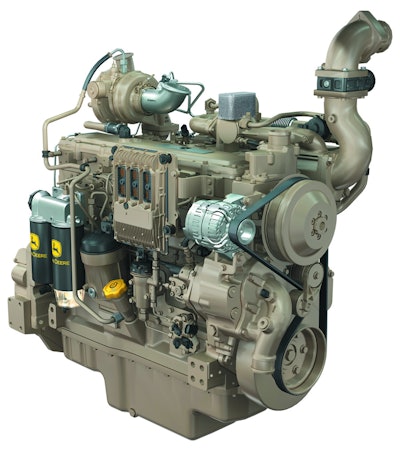
Give a little background as to JDPS's technology solution to accomplish Tier 4 Final goals.
John Deere will continue its planned building-block approach to meet Tier 4 Final and Stage IV emissions regulations. To achieve regulatory compliance, John Deere developed the Integrated Emissions Control system—a solution that optimizes engine performance, operating efficiency and long term durability.
For Tier 4 Final/Stage IV, John Deere will offer its familiar PowerTech displacements of 2.9L, 4.5L, 6.8L, 9.0L and 13.5L. Power ratings throughout the lineup will, in some cases, be higher than previous offerings.
For engines 56 kW (75 hp) and above, the Integrated Emissions Control system encompasses the combination of aftertreatment and emissions reduction components designed and integrated by John Deere engineering to meet the most demanding customer requirements. This optimized solution will deliver emissions compliance without sacrificing power, performance, ease of operation, fluid efficiency, reliability, durability or economical operating cost.
John Deere Tier 4 Final/Stage IV engine performance will meet or exceed that of the John Deere Tier 4 Interim/Stage IIIB engines. The Tier 4 Final/Stage IV engines will continue to provide the same or higher levels of power density and torque along with transient response that meets or exceeds that offered with Tier 4 Interim/Stage IIIB engines.
In addition, John Deere Tier 4 Final/Stage IV engines will meet or improve upon the total fluid economy of Tier 4 Interim/Stage IIIB engine models. The Integrated Emissions Control system will enable John Deere engines to meet emissions requirements while utilizing less diesel exhaust fluid (DEF) than alternative Tier 4 Interim/Stage IIIB SCR solutions. DEF consumption with John Deere Tier 4 Final/Stage IV engines will be 1 to 3% of diesel fuel consumption depending on the application. Lower DEF consumption means DEF tank size can be smaller—minimizing the impact on vehicle applications while extending DEF filter service intervals and reducing operator involvement. Increased pressures created by John Deere's Tier 4 Final/Stage IV high-pressure fuel systems will reduce engine-out particulate matter (PM) and extend intervals between an active exhaust filter regeneration.
John Deere engines below 56 kW (75 hp) will meet Final Tier 4/Stage IV regulations using an Integrated Emissions Control system consisting of an exhaust filter without cooled exhaust gas recirculation (EGR) or selective catalytic reduction (SCR).
What is "Tier 5" going to be?
The complete implementation of Tier 4 Final/Stage IV emissions regulations represents an enormous effort for all involved. It is difficult to predict what might happen after Tier 4 Final/Stage IV.
Reductions in PM on the basis of particle size and greenhouse gases (GHG), such as CO2, are considered likely candidates for future emissions regulations. John Deere's current technology strategy positions us well for the implementation of these potential regulations. Internationally, there are select countries that already employ particulate count emission strategies which our Tier 4 Final/Stage IV engine technologies are able to meet.
There have been concerns as to selling used equipment oversees that is Tier 4 compliant, considering many regions do not yet have an established ULSD infrastructure to use this technology. What is JDPS's response to these concerns, and does it have a plan to accommodate this complication?
If export markets are a consideration for users of Tier 4 Final/Stage IV solutions, they must take into account varying levels of fuel quality and sulfur levels. John Deere has new equipment solutions designed specifically to meet customers' requirements in markets where ultra-low sulpher diesel (ULSD) is not available. Similar to previous emissions tiers, John Deere will have recommended solutions for advanced emissions equipment that migrates to markets with lower quality fuel. As each situation is different and there is wide variance of fuel quality, the best solution is to utilize equipment specifically designed to operate with the fuels in the market. We require consulting a John Deere dealer prior to operating equipment with substandard fuel to identify the best fit solution for the given situation.
What is JDPS doing to streamline its manufacturing process? Is system modularity, reduced engine options, or other practices in place to help lower the overall cost of the engine system considering the price increase with Tier 4 systems?
The building block approach that John Deere utilizes adds incremental technologies needed for each new tier of emissions regulations, which ensures the new technology will deliver emissions compliance without sacrificing power, performance, ease of operation, fluid efficiency, reliability, durability or economical operating cost.
This approach starts with the previous tier engine and adds the most appropriate engine technology to meet the required emissions standards. While there is added complexity in manufacturing, this approach minimizes the overall manufacturing cost of the solution. Furthermore, John Deere leverages six engine manufacturing facilities around the world which are specifically tailored to meet the needs of their respective markets.
How is JDPS involving itself in the hybrid technology development movement?
Hybrids promise significant efficiency gains for many different machines. John Deere drivetrain, engine, and equipment marketing and engineering have been working for many years to understand the benefits of hybrids over traditional powertrains in John Deere and non-Deere OEM machines. We've observed that some form of additional energy storage is required in most machines to provide significant benefits over traditional powertrains.
Today, and in the near future, additional energy storage is expensive. The design of four-wheel drive loaders allows them to store kinetic energy in the mass of the machine. This energy can be extracted with a properly designed hybrid powertrain. Examples of production versions of these systems were introduced in the 644K and new 944K John Deere four-wheel drive loaders at CONEXPO in 2011.
John Deere engineering also collaborates with our subsidiary Phoenix International and several suppliers to evaluate how the characteristics of one component in a hybrid powertrain (prime mover to wheels/tracks) influences the efficiency, durability, packaging, cost and need for other components in the system. By doing so, we jointly develop hybrid systems that improve machine efficiency, productivity and ease of operation with a payback that our customers expect.
Bottom line, John Deere Power Systems is part of a team that continues to advance the state of powertrain technology and implement hybrid systems with the right level of technology at the right time.