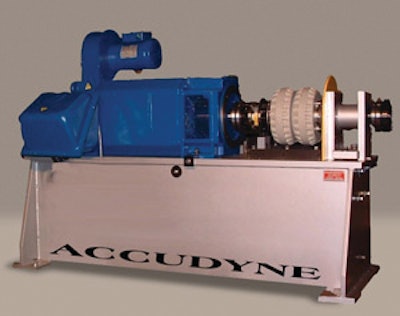
The engine system has undergone countless revisions while engineers worked to meet demanding Tier 4 requirements. What were consistent testing demands and challenges you faced, or that the engine manufacturers and OEM integrators faced with this rapidly shifting system?
In a sense, the Tier 4 government initiatives have conflicting goals—on the one hand they want to reduce the impact of emissions on the environment, and on the other hand they want to increase engine efficiency. At the highest level, the goal is to reduce the use of hydrocarbons. However, it is important to realize that lowering emissions and maximizing power density are often at odds with each other.
From a testing standpoint, we ran into the same situation that the designers are dealing with—a point of diminishing returns. We are looking at finer and finer accuracies and resolutions, and unless you have some fundamental change in technologies, you are not going to come up with a 50% improvement with an incremental change in your design. You start coming up with some very small improvements now, which, added together, add up to a lot.
We have already eliminated a lot of emissions and eked out a lot of the performance capability from this equipment as far as performance and economy. So, what you are left with is much smaller changes, or actually much smaller results. You are already measuring very low emissions with very small differences in performance. With older systems, you’d be able to work with fairly low resolutions, low accuracy measurement and still find substantial differences in your testing. Now as we go, instead of looking for grams, or even kilograms of pollutants in engine exhaust, we are now looking at milligrams and sometimes even less. Measuring very small quantities and very small differences is becoming increasingly more difficult from a testing standpoint, and that has become a major issue.
As far as the people that are building the equipment, they need to build engines that are lighter, stronger, more powerful and with lower emissions. In our case, it’s being able to measure the changes. If you make a 50% change, which means you are already down to a miniscule amount of emissions, and now you need to measure a 5% difference of something really tiny, it is a very small difference. So, the whole level of accuracy and resolution of test equipment is becoming a much bigger deal. We have to be able to come up with more precise detail in the testing data we provide. This is the challenge that faces us when it comes to the new regulations and the new tiers.
Do you see a movement toward design platform standardization?
Design standardization sounds like a great idea, and in a perfect world, it would be a great idea. I think it could make a huge difference. The biggest problem I see with it is that many of our customers have different technologies they use in different situations – and they do this deliberately because they want their information to be kept confidential. In other words, they do not want things in a standardized format or standardized form. In their view, their information is extremely proprietary, so getting individual companies to agree to true standardization is going to be very difficult.
For large companies, standardization may be a difficult challenge internally, but overall, the question here is more about industry standardization. And, many of these companies have very high levels of inertia. They don’t like to make huge changes and many of them don’t want to be too standardized with other companies. Standardization makes their proprietary information and designs far more transportable.
I think there’s a definite tendency to resist standardization in a lot of places in industry. I do think it’s getting better over time. One of the issues we run into in our area of testing is when someone has a new design for an engine or transmission or hybrid vehicle system and they need to be able to test this equipment quickly and precisely, when they design it, they often do not take into account the fact that it has to be tested. It may work very well in the vehicle, but may be very difficult to interface within a testing environment; so, some standardization when it comes to planning for testing would be very useful.
For example, the mechanical system may work great in the vehicle where it is designed to work. But, the bearings on the shaft that we need to attach to a dynamometer may need to be bathed in oil, something that’s normally taken care of by the housing of the transmission that it’s attached to. But in the testing environment, the transmission doesn’t exist. The test system then needs to provide the required lubrication, which has nothing to do with the actual testing, while carefully avoiding any mechanical differences that may skew the results. This can add a great deal of cost and complexity to an otherwise straight-forward test.
Another example is if you have something that is not a standard shaft that you want to attach to the dynamometer. We run into cases where users have large and unwieldy parts that are spinning or moving, and may be shaped in such a way that they work perfectly within the context of the vehicle, but which makes attaching to them very difficult. We spend a great deal of time coming up with some fairly exotic ways to be able to interface to these types of components.
By contrast, some customers are now putting some thought toward design-to-test, where they can make some fairly minor changes in the design phase that don’t affect the operation of the component and don’t have any major effect on its cost, but make it possible to more easily interface to a test system. Especially if the component has to be tested on the assembly line or tested out of the vehicle to see if it’s functioning, there are typically some simple things that can be done to make it much easier, and less costly, to perform the required testing. So, from our standpoint, one of those major standardization items we’d like to see would be design-to-test.
We are seeing some excellent examples of industry standardization that greatly simplify integration in the vehicle, as well as testing. Controller area network (CAN) is a standard that is used on most automotive applications now and is being used a lot in the heavier on-highway and off-highway vehicles.
CAN allows you to communicate with the engine controller, obtain data from it, and send it set points during the test in the same way that it happens in the vehicle. This goes a long way for us to be able to interface to a large component, for example, a large diesel engine or a large transmission, and be able to actually work with it, get data back from it and command it to do what we want it to do. Not only is this type of standardization making it easier to integrate the final product in the vehicle, it is also making it easier to integrate to a test system. That’s a perfect example of standardization that has worked very well. Electronics seem to standardize easier than mechanics at this point.
How have testing systems evolved in relation to hybrid technology development?
Hybrid systems are a unique animal in terms of what we have to test. In most cases, hybrid means you are dealing with an engine (gasoline, diesel or other type) that uses a transmission and driveline; at the same time, you have an electric motor that can transfer power to and from that system. The electric motor system is usually controlled by a high-frequency inverter and powered by a high voltage battery. The electric motor system can be used to assist the engine in cases where it needs a little extra power by using the power stored in the battery. When a vehicle is stopping or decelerating, the motor is used as a generator, and it regenerates power back to the battery. The power is used when necessary which is what makes the vehicle more fuel efficient.
The bottom line is that you have the usual complexities of testing a normal combustion engine and its driveline, to which is added the complexity of a more sophisticated transmission system and a high voltage battery with typically a three-phase electric motor and inverter system. We have to have the expertise to test the engine and powertrain, but we also need to know electric motors, inverters and high voltage batteries and how to either test and/or simulate those components in an integrated test system. It's like putting together two different test systems into one.
It’s been advantageous for us, because for the last 25 years SAKOR has been splitting our expertise about 50/50, in engine and powertrain testing, and in electric motor testing. So when hybrid vehicles came along, we were able to take the two technologies we’re best at and put them into one place.
Hybrid systems have necessitated the use of other technologies than those used with standard performance testing of combustion engines. In classical performance testing you can work with a load-only type dynamometer, which could be an Eddy current or water break dynamometer, which only load the engine and allowed you to do much of the required testing. When we start getting into the Tier 3 and Tier 4 testing, you need to have a motoring dynamometer to conduct certified emissions testing. Also, a hybrid/electric system is a four quadrant system, which loads and drives the vehicle at all times, so again, you need a four quadrant motoring dynamometer to test it properly. That has made the systems much more sophisticated.
AC motoring dynamometers, like our AccuDyne™, are very powerful dynamometers, which also provide very precise control. They are not like the old systems, which would basically absorb power and generate heat. AC dynamometers actually draw power from, and put power back on, the AC mains. They are much more sophisticated and capable because they can load and drive (motor) the component being tested. At the same time, they are more energy efficient and a greener technology in their own right, because with an AC dynamometer system, we absorb power and instead of dissipating heat, we put it back on the energy mains. That actually reduces the power bill and the company’s overall power consumption, so it saves money and reduces fossil fuel use.
What are the challenges and tradeoffs when combining two technologies into one optimized system versus using one technology?
With hybridization, the challenge is to get basically two full drive systems into one vehicle. They may not be exactly the same size, but you’re taking a vehicle that already had a drive system in it and trying to make a smaller vehicle with those same drive system capabilities and a complete electrical system that’s tied into the mechanical system.
Transmissions for hybrid systems tend to be more complex because you have to take power in and out of the electric motor as well as the engine. So, you’re essentially putting twice the capability into the same space, or sometimes even less space, which means a need for miniaturization.
To do this, designers need to work with lighter and stronger materials, for example, titanium, to lighten the overall weight while keeping the strength. The mechanics that are involved with the hybrid can be complicated. There’s a tendency with mechanical systems to operate at fairly low speeds—around 4,000 rpm—but when you get into high efficiency with hybrids, the hybrid part of the system may run at very high speeds, sometimes 10,000 to 14,000 rpm. So you have to step that speed down to a more normal speed that can be used with the rest of the vehicle.
The technologies are a bit different in some cases when you are dealing with very high speed, low inertia, precisely balanced equipment on the electrical side and a more standard engine and powertrain kind of mechanics on the other side. Then, these two different technologies have to be folded together. It is not simply adding one to the other; there are two different sets of technologies, a whole different set of experiences, and sometimes different teams of people. You don’t just load a motor onto a vehicle and have a hybrid vehicle; you will not get the efficiency you are looking for. To get all that equipment into one vehicle and increase the efficiency at the same time can be a very difficult job.
As a test system provider, you are exposed to prototypes and systems that are yet to be seen in the off-road and heavy-duty on-road industries. What new trends are you seeing engineering teams attempt as they continue to demand more from a system?
There is a drive for fuel economy, which is requiring lighter, stronger and tougher materials, and that means we will have to be testing much more precisely and be working with evolving and often cutting-edge testing technologies.
One interesting thing we are seeing is a lot more 100% quality testing, especially in military areas and some of the large on-highway engines, whereas in the past, one out of a hundred engines or transmissions would be tested. This requires a lot more test equipment, but there also seems to be a need to measure much more finely, more accurately, and there’s a drive towards doing more testing than we saw 20 years ago.
Work force and education development efforts
Dealing with two different technologies means you need a broader background in your engineering teams, and to some degree, people need to be cross-trained more. You need people who have experience in the standard mechanics of a combustion system, are comfortable in the electrical world, and can deal with the mechanics involved with the electric motors. Everyone can still work in a precise and narrow area, but you want people who understand the entirety of what they’re doing. So having a broader background in the mechanical disciplines and the electrical disciplines is important.
We are currently involved with a project at Michigan State University’s engine research facility. We’re also working with a small local college to get dynamometer systems incorporated into their programs so when people are working on engine design or engine repair, they’re using the proper equipment to test the results, rather than just the theoretical results of their work.
In the past, people could rebuild an engine and then start it; if it spins and runs, then it’s okay. But will that engine really run correctly? Does it really generate the right amount of power? Traditionally there have been few people who really know how to take it to that next level before actually putting the engine into a vehicle for testing. So, we’re working with some of the local schools, actually showing their students about dynamometer systems and the kind of test systems used by industry and the military to test engines. These systems will let the students see if it will really operate the way it’s supposed to. You quickly find out if there’s a bad bearing or something that went wrong in the rebuild or the repair process, which you can’t find out when you have it sitting on an engine stand and run it but don’t put any load on it. There’s definitely a push toward giving students a broader background so they understand more aspects of how to test their work, and verify that it does what it’s supposed to do.
What political topics are you most concerned with? How will policy changes potentially influence your company, positively or negatively?
The current administration has pushed very hard in support of hybrid vehicles and hybrid vehicle testing. There has been a lot of discussion and argument on whether the policies have been effective or not with the number of bankruptcies that have occurred.
We have been involved in these initiatives, and that has created quite a bit of business for us. I don’t see that going away at this point. However, I have had some customers telling us that if the current administration is replaced on election day, that they will be buying a lot of equipment, but if we stay with the status quo, it is much less likely.
So, from my business standpoint, there’s a great deal of business that is clearly riding on whether or not there’s an administrative change. The industry seems to be saying that if the administration stays the way it is, there will be very little growth and very little purchase in the research and development (R&D) sector. If there’s a change in the administration, then there will be much more equipment purchased. That’s what I’m hearing loud and clear from my customers. It really does impact my business in a huge way.