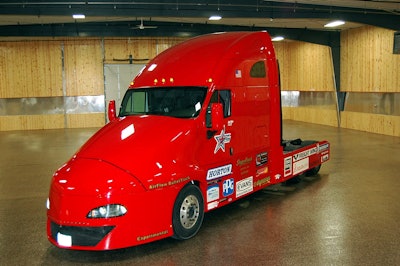
When thinking of the Class 8 trucks traveling across today’s roadways, the term ‘fuel efficient’ does not often come to mind. Though there has been much technological advancement over the years—particularly in the last decade due to ever-increasing fuel prices and environmental consciousness—the typical truck only averages in the range of 5 to 6 mpg.
However, Robert Sliwa, President and owner of AirFlow Truck Co., is one of many in the industry working to make the Class 8 truck a more efficient vehicle. As a former owner-operator, Sliwa saw firsthand the inefficiencies of these trucks, particularly when it came to purchasing fuel. He purchased his initial truck in 1980 which only got 4.4 mpg. “That was a rude awakening because as an owner-operator back then I was driving 600 or 700 miles a day,” says Sliwa. “Even though the price of diesel fuel was lower than it is today, it was still a lot of money.”
He soon began to experiment with making various modifications to the tractor and trailer, as well as using different driving techniques to improve the truck’s efficiency. Sliwa had sponsorship from a few companies for his project including Cummins Inc. and Goodyear Tire and Rubber Co. “I had a goal to be the most efficient I could from point A to point B because obviously I had a vested interest in spending less money for fuel,” Sliwa explains. “Through constant experimentation and the day-to-day grind of [trying different] things, the truck averaged pretty close to 10 mpg during the first run in 1984.”
Unfortunately, he says the truck was an anachronism because not many people at that time were concerned with saving fuel or had an awareness of greenhouse gas (GHG) emissions. Sliwa sold that first experimental truck in 1985 and took on other careers. But in 2008 he found himself quitting his job, buying another Class 8 truck and once again working to develop a more fuel efficient Class vehicle.
When he began working on what would become known as the BulletTruck, Sliwa says he thought it would take him just six months. However, he wound up working on it from 2009 to 2012, doing about 99% of the work himself and self-funding the project. Once completed, he drove the BulletTruck coast to coast and averaged 13.4 mpg over the course of the trip.
Sliwa was then contacted in 2013 by Shell Lubricants to do some testing together of the BulletTruck. At the beginning of 2015, AirFlow and Shell signed a contract to begin co-engineering a new truck design which will be known as the AirFlow StarShip. “We originally did this because we know there are a lot of efficiencies we’ve been able to gain through lubricants in an engine,” explains Dan Arcy, Global OEM Technical Manager at Shell Global Solutions. “We decided to look at this as an opportunity to say ‘beyond lubricants, beyond working with the engines, transmissions and axles, what else can we do to get the best use of energy that comes out of the fuel?’”
Bringing the StarShip to fruition
The new StarShip truck will be built from the ground up, starting with a new, proprietary cab design. Sliwa says some of the challenges associated with the previous truck iterations were the fact he began with a major OEM’s cab. “There are a lot of compromises they do with the windshield and the eight pillar angle, and aerodynamic compromises,” he says. “With Shell as the sponsor I’m able to design a new cab that is [very] aerodynamic, and we have high hopes for shattering all the mpg records for the new truck.
“It’s a completely from scratch designed cab, so we have almost no compromises aerodynamically,” Sliwa continues. “This truck will have the lowest coefficient of drag; the less the diesel engine has to spend energy just to push the trailer down the road, the less energy the truck extends to push through the air, the less fuel we use.” Aiding the improved aerodynamics will be joining the tractor and trailer into an integrated unit to eliminate the gap between the two which is a large source of aerodynamic drag and efficiency losses. The conjoined tractor and trailer will feature an Active Aerodynamics gap sealer that retracts, along with the newly designed side skirts, when driving less than 35 mph or approaching an obstacle, allowing for further efficiency benefits. In addition, the cab will be made of composite materials to help reduce its overall weight. Within the cab Sliwa will use a glass panel with all digital displays similar to that used in modern aircraft.
The look of the new cab will be somewhat of an amalgamation of previous cab designs, says Sliwa. Back in 1983 when making his first truck, cab-overs in which the driver and passenger sat above the engine were typical; these cabs were square in shape and looked similar to a barn door he says. The 2012 truck had today’s more conventional cab which places the driver and passenger behind the engine. “The new truck is a hybrid, a crossover of a cab-over and a conventional [cab], a unique body that nobody’s every seen before,” Sliwa says.
Shell is taking the lead on the lubricants and coolants side of the project, using it as a means for testing its next generation engine oils. With the impending PC-11 specification for heavy-duty engine oils due in 2016 (see sidebar, pg. xx), Arcy says Shell has developed new engine oils similar in viscosity to those it has available today, as well as lighter viscosity oils designed for improved fuel economy. “We’re going to be using these low viscosity oils in the engine, as well as next-generation transmission and axle oil.”
“Fuel economy is really driving the on-highway trucking industry right now,” Arcy continues. If the whole industry were to gain 1% in fuel economy, that would equate to almost 1 million gallons a day in fuel savings for the industry and about $3 million per day in cost savings. “From a lubricant standpoint, we have some lubricants that can provide fuel savings today of greater than 1%. The next generation will provide even greater gains, so the numbers are quite large when you start to look at it from a macro scale.”
While the cab and some of the lubricants used in the StarShip are new, much of its componentry is comprised of readily available products. “We’re using standard, off-the-shelf [products], a standard driveline configuration,” says Sliwa. “I’m building it like a standard OEM would, sourcing parts from suppliers.”
The truck’s engine will be a Cummins ISX 15 liter engine with downspeeding capabilities, enabling it to operate at lower rpms to reduce fuel consumption. “Cummins has a belief in my thesis that a bigger displacement engine, a 15 liter versus a 12 or 13 liter, in our application will get better fuel economy because we’ll be operating the engine at low rpms,” says Sliwa.
Other components on the truck will include an 18-speed Eaton automatic transmission, Michelin low rolling resistance, wide base tires, Alcoa all-aluminum wheels. No batteries will be used for engine starting, but instead a Maxwell engine start module. Batteries will be used, however, to power the all-electric HVAC system. An array of solar panels on the roof of the trailer will collect energy that will then be stored in the batteries and used to power the HVAC during hotel loads, eliminating the need to idle the engine, and thus reduce emissions and fuel consumption. Using an all-electric HVAC will also eliminate the parasitic losses often associated with the pulleys, belts and compressors used in traditional HVAC systems.
Parasitic losses will be eliminated in the drivetrain, as well, by using just one differential—a Meritor FUELite 6x2—instead of two as Sliwa had done in the previous BulletTruck. Use of Shell’s lower viscosity oils in the transmission and differential will also aid with this. Sliwa says the team is also looking into the use of an e-assist for further efficiency gains when traveling down mountains. The system would act similar to those found in hybrid cars in which it recharges batteries while traveling down a mountain and assisting the engine when driving up a mountain, requiring less demand—and thus fuel use—from the engine. “With the BulletTruck, if on straight roads we could have gotten about 17.5 to 18 mpg, but between Connecticut and California you have the Rocky Mountains,” says Sliwa. “When the BulletTruck would go up the mountain or even light 2 or 3% grades in Pennsylvania it would only get 2.5 to 2.9 mpg.”
Sliwa and Shell are working closely together throughout the project to ensure the team achieves the desired results. “We’ve got to work closely on this because any changes in design for aerodynamics and [other aspects] effects a number of other things, [such as] temperatures under the hood,” explains Arcy. Shell is currently in the process of developing its next generation oils to meet the new PC-11 specification, and is using what its learning from the development and testing of those for the StarShip project.
Currently Sliwa is in the process of virtually refining the cab design. “We have the cab and other tractor components probably 90 to 95% done,” he says. Once that’s complete, production of the cab will begin. He is also working with Cummins to specify the final rpm gearing for the engine that will be used in the truck, and will then work with the company to begin simulations of the engine and new truck design.
In his 8,000 square foot shop, Sliwa and his one full-time employee are assembling the rolling chassis of the truck, adding the transmission, suspension and other necessary components. “Everyday we’re getting that rolling chassis assembly steps further ahead and getting subsystems like the air conditioning system so when the new composite cab is done, it can be placed.
“Very soon we’ll be mating the chassis and the cab, and after that we’ll be doing some testing regionally and locally,” says Sliwa. He anticipates local testing will begin around the third quarter 2016, and regional and coast-to-coast testing to begin by late third quarter or early fourth quarter 2016. Once testing begins, Sliwa says “Fuel efficiency gains and GHG emissions will be astronomically better…than a truck you can buy from a large OEM at this time.”