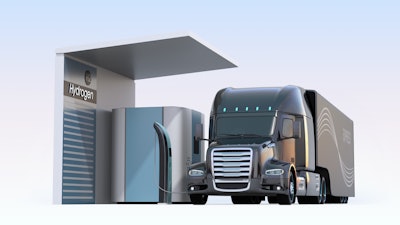
In recent years, hydrogen has emerged as one of the most attractive alternative fuel options for OEMs seeking to dramatically cut emissions from their engines. This is for good reason – hydrogen is a true zero-emissions fuel, emitting only air and water while generating the significant horsepower and torque required in a variety of heavy-duty applications. The technology is evolving rapidly, as governments and industry leaders continue to address some of the barriers to widespread adoption and provide support for OEMs to develop reliable infrastructure and high-performing fuel cell systems.
Hydrogen as a fuel source comes with some special considerations that must be made in relation to material selection and specification of critical system components. The systems (see Figure 1 below) are responsible for on-vehicle hydrogen storage and for converting hydrogen and oxygen to electricity, typically involving a variety of valves, fittings, and tubing. Here, these components must deliver uncompromising, leak-free performance—vehicle and driver safety depend on it. Likewise, the refueling infrastructure that will be necessary for wider adoption must be able to reliably contain and transfer large volumes of hydrogen from storage tanks to the vehicles needing to refuel.
The fluid systems involved in performing these tasks are highly important, and they should not be overlooked by OEMs during the design phase of hydrogen vehicles or refueling stations. This article will explore a few challenges inherent to hydrogen fuel systems in vehicle applications and how to overcome them by selecting high-performing componentry.
Figure 1: Material selection and specification of critical system components which store hydrogen on the vehicle must be taken into careful consideration to meet application needs.Swagelock Company
Hydrogen embrittlement and material concerns
Corrosion is a problem that can plague any metallic system on an on-road vehicle, and it is often exacerbated by a variety of driving and operational considerations. A city bus operating in a snowy North American climate, for example, may have to contend with roads treated by salt or other form of de-icer, which can be harsh on equipment.
Hydrogen containment under conditions like these can be especially challenging due to a phenomenon known as hydrogen embrittlement. Because hydrogen molecules are very small, they have the tendency to diffuse into metals, causing them to become brittle. This issue affects traditional 316 stainless steel, which is often used for valves, fittings, and tubing deployed in hydrogen vehicle architecture.
This can become a significant problem impacting system performance. The dissolved hydrogen atoms can cause changes in the mechanical properties and behavior of the metal, including reducing its ductility, impact strength, fracture toughness, and resistance to fatigue (see Figure 2 below). In effect, hydrogen embrittlement may cause lesser grades of stainless steel to act similarly to cast iron—highly brittle and more susceptible to corrosion and cracking. Subjected to sufficient static or cyclic tensile stress, the embrittled stainless steel is at a greater risk of failure. Considering this issue, a hydrogen system that has been designed and constructed with higher-grade stainless steels that are more resistant to embrittlement can be more reliable over the long term.
What differentiates a higher performing stainless steel? For example, 316/316L stainless steels that include nickel content between 14 and 30% will show relatively little embrittlement. These higher percentages help promote greater ductility and corrosion resistance. Conversely, ferritic alloys with lower nickel contents can become significantly embrittled when hydrogen atoms diffuse into these materials. And while ASTM International requires a minimum of 10% nickel in 316 stainless steel formulations, such formulations with a minimum of 12% nickel can be better suited for the unique operational challenges inherent to hydrogen interaction.
Figure 2: Hydrogen embrittlement may cause lesser grades of stainless steel to act similarly to cast iron–highly brittle and more susceptible to corrosion and cracking.Swagelock Company
Higher pressures for hydrogen storage
The pressure at which the gas is stored is another unique consideration for hydrogen transportation. As the technology has advanced, pressures have risen—the higher the pressure, the further the vehicle’s range.
Many modern fuel cell vehicles store hydrogen at either 350 or 700 bar (5,000 or 10,200 psi), which is typically dictated by the needs of the application. Vehicles that make up a short-range fleet, for instance, commonly have 350 bar storage. The range, and therefore the storage pressure, can be lower here because the vehicles will return to a centralized hub for refueling each night. A long-haul trucking application, by contrast, will need 700 bar storage to obtain the ranges operators are seeking, typically greater than 400 mi. (643.7 km).
High pressures require high performance, and traditional components are not typically applicable. Stringent regulatory standards must often be met for hydrogen fuel service. The (EC) No 79/2009 EU H2 Regulation in Europe, for example, must be met by any component that is intended to handle compressed hydrogen with a nominal working pressure above 30 bar (435 psi). This includes the 350-bar systems and the higher-pressure 700-bar systems that are becoming more prevalent to meet evolving market demands. For these reasons, it is important that OEMs seek out and specify tubing and tube fittings that meet (EC) No 79 certification for Europe, and HGV3.1 certification for North America.
Operational vibration
In addition to their ability to handle high pressures, fittings and connections in hydrogen vehicle applications must be able to withstand constant and repetitive vibration while maintaining their leak tightness.
Consider, for example, traditional cone and thread tube and tube fittings that are commonly used in a variety of industrial applications. Ongoing vibration can cause cone and thread fittings to loosen over time, especially since cone and thread connections are made manually. The quality of tube preparation and the finished connection can vary widely depending on the skill and experience level of the installer. Hydrogen gas is not forgiving of these kinds of imperfections—tiny hydrogen molecules once again can cause potential issues if operational vibrations have caused even the slightest opening in a connection, allowing hydrogen gas to escape through even a miniscule space.
Two-ferrule fitting systems can make for a better selection here. A double ferrule design (see Figure 3 below) can create a twin mechanical grip on system tubing, effectively reducing the likelihood of fittings backing off, even when subjected to continuous operational vibration. This style of tube fitting is additionally less prone to manual installation errors. A new style of two-ferrule fittings that are specifically designed for hydrogen are made by threading a preassembled cartridge (including a nut, two ferrules, and a plastic arbor) onto the fitting body. The tubing is then inserted and marked to establish alignment, and one full turn is applied to complete the connection. After checking with a gap inspection gauge, the fitting is complete and ready for use.
Figure 3: Two-ferrule fitting systems can create a twin mechanical grip on system tubing, effectively reducing the likelihood of fittings backing off, even when subjected to continuous operational vibration.Swagelock Company
Making the right selections for hydrogen fuel systems
In summary, hydrogen fuel systems have unique demands that must be met by each of the components that contribute to reliable, safe operation. Materials must combat hydrogen embrittlement and be able to withstand corrosion; they must be able to contain compressed hydrogen gas at increasingly high pressures to attain higher mileage ranges; and they must be able to withstand continuous operational vibration and maintain leak-tightness at all times.
In addition to ensuring the specification of high-performance components that can meet these demands, designers and manufacturers should look to work with component suppliers with considerable, wide-ranging experience in the hydrogen space. Materials science knowledge, along with experience helping OEMs build reliable systems in a variety of gaseous applications, can be a major advantage for organizations seeking to seize new opportunities in the growing hydrogen transportation market.