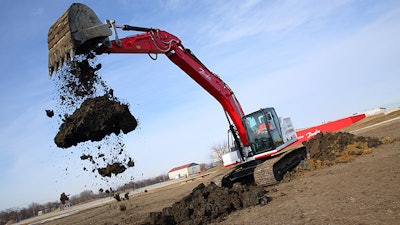
Danfoss has been developing and testing its Digital Displacement technology for several years now. The company sees Digital Displacement as a viable means of improving efficiency of heavy-duty equipment. These efficiency gains will also help to reduce emissions which is becoming an increasingly important for customers.
Hydraulics systems are an important part of many machine designs, even as they become more hybridized and electrified. Despite their power benefits, hydraulics also have many inefficiencies associated with them which Alasdair Robertson, Director, Product Portfolio & Marketing at Danfoss Power Solutions, said are under even more scrutiny as electrification increases.
"With Digital Displacement, we've created the technology that tackles these losses at the pump and brings new capabilities to the way hydraulic power is created," he said during the company's recent POWERtalk virtual event focused on the Digital Displacement technology. "[We can] make significant savings at the system level, no matter what the prime mover is."
The Danfoss Digital Displacement pump (DDP) allows direct control of each cylinder within the pump on a real-time basis. Robertson said the controller is integral as it contains the software which is used to determine all DDP functions. Sensors on the pump provide feedback on outlet pressure, shaft speed and crankcase temperature. The controller takes these inputs as well as demand from the machine user and turns it into a stream of valve actuation pulses.
Digital Displacement allows for independent control of each valve which Robertson said introduces new capabilities to the world of hydraulics. "This is really a unique opportunity in hydraulics to leverage not just an efficient way to create hydraulic power but also a unique platform for creating new system architectures that leverage these unique capabilities," he said.
READ MORE: The Next Chapter for Hydraulics
While the company sees the technology providing benefits to many types of heavy equipment, it believes excavators in particular will be able to achieve efficiency gains through the use of its DDP. Studies Danfoss has completed have found hydraulics systems on excavators can have an overall efficiency of 30%.
Niall Caldwell, Senior Director, Research & Development at Danfoss Power Solutions, said Danfoss has studied traditional hydraulics systems in excavators and found them to have an overall efficiency of 30%. This leaves a lot of room for improvement, which Danfoss believes can be achieved using its DDP. Caldwell said there are four main benefits DDP can provide to help improve the efficiency of hydraulics systems as well as the overall machine.
Niall Caldwell explained the many inefficiencies of current excavator hydraulics systems during Danfoss' POWERtalk event.Danfoss Power Solutions
1. Better Pump Efficiency
Because the DDP is a completely new digital pump it works on a completely different operating principle, said Caldwell. "You can simply take the analog pump out and put the digital pump in, and you can realize significant savings," he said.
From Danfoss' benchmark testing comparing its DDP to axial piston pumps, the company has found the DDP to be very efficient when operating at full displacement. Caldwell said the big takeaway from Danfoss' testing is the pump's part load efficiency. The DDP has shown an overall efficiency of 90% even when at 20% displacement. This equates to less heat generated by the system and thus less energy loss. "It's hard to think of a bigger impact that you could make, simply by a component selection decision."
He notes machine functions all remain the same, as does the user experience and the operator interface. The pump also fits into the same space as a conventional pump which can benefit OEMs as they are designing their equipment.
2. Better System Efficiency
Digital Displacement is not only a pump but a full system enabled by a unique feature of the DDP, said Caldwell. "We can design it so that it has multiple independent fluid outlets," he said. "They're all contained within a single body, and they're all controlled by a single controller, but they can all do different things." A multi outlet version of the DDP096 is expected to be released into the market in 2021.Danfoss Power Solutions
Each of the outlets could be doing different things in real time, changing their functions millisecond by millisecond. One could be doing pressure control, another could be doing a different type of control action and one could be completely idle, explained Caldwell. "All of these functions are coordinated by that single controller with a master torque limit, so that the engine torque is respected."
The outlets can be combined with digital valves which allows flow to be allocated where needed in the hydraulics system; if more is needed in one portion than another it can control the flow accordingly. This helps to ensure flow is generated efficiently and eliminates throttling in the system. "We can actually eliminate throttling losses in some hydraulic systems, and that for the far future is what we want to do to achieve the full potential of Digital Displacement," said Caldwell.
3. Digital Pump Control
The fact the pump is digital at its very core can provide many benefits. Since it is completely software controlled, the pump and its functions can be changed and configured for specific applications. The software determines what the pump is doing at any one time, said Caldwell. This helps provide predictable and accurate output.
"That means the pump action is inherently deterministic, and that's a very desirable property when you're thinking about control systems, particularly for automation," he said.
The DDP can also very accurately and quickly limit its output torque which Caldwell said makes it possible to get up to and maintain the torque limit of the engine. "In fact, we can get such good response speed and such accurate control that we can manage the engine speed simply from the pump, so that means the engine runs at full torque all the time in some stages of the duty cycle," he explained. "It's the pump's job to control the engine speed, because it's the load that the engine is seeing. That way we can actually maximize the power that's delivered by the engine."
In addition, he said the DDP provides very fast response of almost an order of magnitude better than most hydraulic systems depending on the rpm. Response speed can be coordinated with other system activities, as well, noted Caldwell.
He equated it to an electric motor and its response capabilities. Electric motors and their inverters are also software driven, enabling all parameters to be precisely controlled. "It takes hydraulic pumps into a world where electrical engineers would expect them to be," said Caldwell. "That is really transformative when we look toward electrification."
Multiple control functions and the ability to change the function of individual outputs provides system engineers the opportunity to potentially use the pump's functions in different ways and in different modes of the duty cycle.
The DDP's built-in software modules can be easily configured using Danfoss' PLUS+1 technology. A CAN interface on the pump allows communication via a CANbus protocol with either a Danfoss controller or an OEM's own controller.
From all of this, there are many benefits to OEMs. First is the ability to utilize model-based design which Caldwell said is the future for "how ever-more sophisticated off-highway systems are going to be designed and developed." DDP is very compatible with mode-based design methods, he said, which are used to more easily and quickly conceive of and validate more sophisticated designs.
By employing software to set up the parameters of the pump, there is no longer a need to manually do so as is the case with some conventional analog pumps, he said. Changes can be made quickly, speeding up the entire design process. This will come in handy particularly for engineering teams developing electric-powered equipment. "This is a machine which tells you exactly what it's doing. It tells you how much fluid it's making, what pressure it's at, how much torque it's taking. And so, it really is an active part in the overall control system of the vehicle," said Caldwell.
DDP can play a large role in automated systems, as well. Caldwell said if you're going to automate something, you need components which are predictable and will do what they are told and tell you when they have done it. "Automation really relies on the system components being deterministic and this is something that Digital Displacement supports," he said. "In the future we see that enabling of automation as becoming more and more important."
Danfoss continues to the test the use of its Digital Displacement pump technology in excavators to evaluate the potential efficiency and productivity gains possible.Danfoss Power Solutions
4. Efficient Energy Recovery
When lowering an excavator boom or swinging it, there is lost energy that could be recovered and used. Caldwell said Danfoss has demonstrated at its facility in Edinburgh, Scotland, the efficiency with which this energy could be collected and put back into use when employing a DDP.
He said the results the company have gotten thus far from the testing are encouraging. It's shown an overall efficiency of 87% when going through the entire cycle of moving the excavator boom. "This is really unheard of for hydraulics systems, and in the future will be a real enabler to get to the 50% and beyond improvements we think are possible with digital displacement," said Caldwell.
Danfoss is working to bring all of these benefits together into a pump it can provide the heavy equipment market. It is currently developing and testing three models which are at various phases of the design process. Two of the models have undergone extensive testing with the company and OEM customers. It announced in November it plans to bring the first DDP designs to market in 2021.
Niall Caldwell explains the various versions and benefits of Danfoss' DDP technology currently under development during the company's recent POWERtalk event.Danfoss Power Solutions
Each model builds upon the capabilities of the previous to provide more benefits and fit the varied needs of OEMs. For the third model currently in testing phases, Caldwell said Danfoss is designing a new fame size and structure for the DDP that will enable its use in larger machines.
The pumps have so far shown high levels of fuel savings as well as productivity improvements. This will help end use customers to reduce their fuel costs while potentially increasing the amount of work they can do in a day. Improved efficiency can also equate to other benefits including reduced emissions and the potential to downsize a machine's power system—whether that be an engine or batteries.
Overall, Danfoss believes its DDP technology could prove very beneficial for the heavy equipment industry.