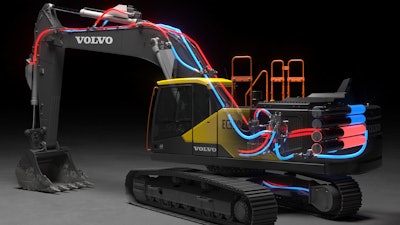
Efficiency is a key design criteria for almost all components and systems on a piece of heavy-duty equipment—as well as for the machine itself. Hydraulics are one of the many areas in which manufacturers are looking to achieve efficiency gains.
Hydraulic components and systems remain a vital part of most machines due to their power density but are often seen as less efficient. Incorporation of electronics and advanced software control are among the methods manufacturers are utilizing to improve efficiency.
Erik Westergaard, Senior Systems Engineer at Danfoss Power Solutions, says the company’s Digital Displacement pump technology—which the company has described as being inherently digital—has shown between 15 and 30% efficiency increases. The design of the pump itself combined with use of an electronic controller and advanced software controls enables these efficiency gains. In addition, Westergaard says the architecture around the pump also plays a part in improving efficiency. Read more about Danfoss’ Digital Displacement pump technology.
Digitalization provides opportunities for improved efficiency
The design of hydraulic components, as well as what components are used to form a system are important factors for improving efficiency, says Westergaard. How the chosen components are controlled through software is equally as important. It can help make the system operate smarter, offer better integration with engine operation as well as help operators be more efficient with the work they’re doing—all of which can lead to efficiency improvements for an entire piece of equipment.
Understanding and analyzing the duty cycle of different applications enables Danfoss to better determine where there are areas for improvement. Doing so makes it easier to determine where gains can be made, and where they might not. “Then you can lay out the system accordingly and also design the controls to still meet the demand of the application [while trying] to optimize it…from an efficiency or a productivity point of view,” says Westergaard.
Software controls are an area Westergaard says Danfoss is focusing much of its development efforts for hydraulic components and systems. This includes designing the software in such a way that productivity increases can be achieved as well as inherent efficiency gains to help make machine operators more accurate. Doing so can reduce wear and tear on components, improving the overall lifespan of a machine.
In the area of steering, the company is working on electrohydraulic systems with multiaxis steering capabilities and steer-by-wire, both of which can help enhance operator comfort and reduce fatigue. Moving a steering wheel for off-highway equipment often requires a lot of shoulder and elbow movement, says Westergaard. Eliminating the need to use a steering wheel and instead utilizing an electrohydraulic joystick, for instance, can greatly reduce these movements that would otherwise put a lot of strain on operators. “We have some studies showing that you are on average reducing 65% of these movements,” he says when moving from conventional steering using a steering wheel to joystick steering on a wheel loader.
A more comfortable operator is a more productive one, which leads to more efficient operation and control of a machine.
READ MORE: Danfoss and AGCO Design Completely Joystick-Operated Combine
In December 2020, Volvo Construction Equipment (Volvo CE) announced it was developing a digital hydraulic actuator with the goal of improving fuel efficiency of construction equipment. Development of the technology began at a university in Finland and with a Finland-based company, Norrhydro, with whom Volvo CE is partnering on further maturing the technology for use in construction and other heavy-duty equipment, particularly excavators.
The actuator works like any other linear actuator, says Kim Heybroek, Research Engineer at Volvo Construction Equipment. “It controls force and speed of individual drives such as the boom or arm function of an excavator or a wheel loader,” he explains. “However, if you compare it to a normal double acting cylinder drive, this actuator is comprised of a mechanical cylinder and a number of electronically controlled valves and ECU (electronic control unit) with a software control interface that is controlling those valves with feedback from sensors within the actuator.” The Norrhydro patented system, NorrDigi, is a key part of the new digital hydraulic actuator technology Volvo CE is developing in collaboration with Norrhydro.Volvo Construction Equipment
Feedback from the sensors control the force and velocity of the actuator in a closed loop fashion, he further explains. Instead of a conventional two chamber hydraulic cylinder, the actuator utilizes a four-chamber cylinder; the four chambers can be selectively pressurized by two supply pressure lines to enable 16 discrete force states to be achieved for any given pressure level in the supply lines. “Basically, you can think of this as the hydraulic equivalent of a stepped mechanical transmission,” says Heybroek.
“Another way of understanding this is that the effective hydraulic area inside the cylinder is altered in steps depending on which of those two supply pressures is applied to which cylinder area,” he says.
According to Heybroek, the digital hydraulic actuator enables the design of a new type of hydraulic system which overcomes some of the shortcomings found in traditional systems such as the inability to recuperate kinetic energy excessive pressure compensation losses.
The digital hydraulic actuator allowed the creation of a hydraulic common pressure rail system in which all actuators are connected to a pressure rail containing hydraulic accumulators used for system decoupling and energy storage. With this design, pressure is applied only to the amount of cylinder area needed to generate the required force for the application, radically reducing pressure compensation losses says Heybroek. “It also enables bidirectional energy flow to and from the common pressure rail, which means that kinetic energy in a boom down motion may be recovered and stored in the accumulators,” he says. “At the same time, accumulators also serve as a source of peak power which means the power supply system may be downsized.”
For rotary drives and functions, such as the swing or travel drive of an excavator, Heybroek says only the required amount of motor displacement is engaged to generate exactly the required amount of torque. This is achieved through the use of variable displacement motors.
Prototype testing to date for the digital hydraulic actuator on a 30-ton excavator has shown fuel efficiency improvements of 50% compared to a standard Volvo CE machine working in the same operation.Volvo Construction Equipment
He says the company has conducted prototype testing to date on a 30-ton excavator which showed hydraulic losses are approximately cut in half and fuel efficiency improved by 50% compared to a standard Volvo CE machine working in the same operation. “We define fuel efficiency as the amount of work performed over the amount of fuel consumed,” he explains. “Part of this improvement comes from reduced fuel consumption and the other part from increased productivity.”
While the technology is currently being evaluated for excavators, Heybroek says it would suit use in machines or functions where there is a relatively high load inertia. “The highest efficiency gains are found in work functions or duty cycles where heavy mechanical structures are lifted against gravity, then lowered again.”
Lubrication choice is a vital component
Blayne McKenzie, Ph.D., Strategic Technology Manager, Industrial Products at The Lubrizol Corporation, says any change to a hydraulic system will impact its efficiency, including those made to the hydraulic fluid. Because hydraulic fluid is so important to the functionality of the overall hydraulic system, several performance factors can be impacted when changes are made to a fluid.
Optimizing aspects such as viscosity maximizes both volumetric and mechanical efficiency, which aid overall system performance. “Every change to the lubricant, every enhancement of hydraulic flow in the power delivering primary flow direction can be really significant,” says McKenzie.
As part of its efforts to develop sustainable energy efficient hydraulic fluids, Lubrizol is deploying a new class of energy efficient performance polymers. The company is doing so by enabling the move from monograde fluids to multigrade alternatives using Lubrizol’s performance polymer technology, says McKenzie.
“We're developing those fluids with an eye towards saving energy consumption, whether that's fuel or electricity, [and] being able to do more work,” he says. Lubrizol’s viscoelastic performance polymers enable hydraulic energy efficiency. Their ability to coil and uncoil in situ can dissipate energy losses from secondary flows.The Lubrizol Corporation
McKenzie says adding a performance polymer to a hydraulic fluid is not a new concept. What is new is the chemistry of the polymer Lubrizol is using. The new energy efficient performance polymers are long and flexible, capable of coiling and recoiling in a solution based on temperature and flow. They are also able to store and disperse energy. These features enable the polymers to disrupt parasitic, or secondary flows, which occur any time fluid is being pushed in anything but a straight line, which is basically all the time in a piece of heavy equipment, says McKenzie.
Traditional performance polymers, on the other hand, tend to be short and rigid, and do not have an inherent capability to enhance hydraulic flow like the new Lubrizol polymers can.
The energy efficient performance polymer is used in conjunction with an industry-standard additive technology to ensure it continues to provide the existing durability, oxidation and corrosion protection requirements of the market. “That gives confidence to our end users that any changes we've made for efficiency’s sake have not compromised [industry requirements],” says McKenzie.
Testing and use in operating equipment has demonstrated the new energy efficient performance polymers’ capability to reduce fuel use for heavy equipment owners. It has also shown the ability to make systems themselves run more efficiently, which can help to reduce costly downtime and enable machine operators to get more work done.
These benefits can also lead to a reduction in emissions produced, helping the environment and meeting the sustainability targets Lubrizol is looking to achieve with its new polymer chemistry.
As fluid passes through a 90-degree bend in this hydraulic line, flows across the primary direction arise. These secondary flows are visualized here with greater intensity of red (clockwise) or blue (counter clockwise).The Lubrizol Corporation
Hydraulic systems and requirements will continue evolving
Sustainability and doing more with less will be two of the biggest pressure points placed on hydraulic fluids and systems in the coming years, says McKenzie. “What that means for hydraulic systems and ultimately for hydraulic fluids is higher speeds, higher pressures, higher loads, [as well as] lightweighting, yet construction equipment will still be expected to carry the same amount of dirt from A to B or dig the same hole,” he says. Hydraulic fluids will therefore see more intense workloads in which they are utilized, placing a greater pressure on their ability to meet both efficiency and application requirements.
The push toward electrification as part of sustainability initiatives is already having its impact with electric and hydraulic systems coming together to create more efficient machines which leads to fewer emissions produced.
Heybroek says the digital hydraulic actuator Volvo CE is developing can actually be an enabler for electrification and other industry trends such as automation due to its integrated sensors and other electronics. In addition, the actuator features a more simplified package which requires less space claim in both traditional and alternatively powered equipment.
The common pressure rail system design uses only two main pressure lines to which all the actuators are connected. The distributed valves are integrated together with a cylinder or the actuator, enabling the main control valve normally used in an excavator to be eliminated or significantly reduced in size which leaves more available space in the center of the machine. For electric machines, this could allow more batteries to be installed into the machine to help meet power requirements of construction or other heavy equipment.
He also notes the reduction in losses achieved with the digital hydraulic actuator can help to simplify machine electrification and reduce the amount of battery capacity required.
With the efficiency gains today’s hydraulic components and systems can achieve, and those that are yet to come, manufacturers are well equipped to meet the growing need for solutions which are more sustainable and capable of doing more with less.
Danfoss test machines in a gravel pit help the company evaluate the capabilities of its new hydraulic system technologies.Danfoss Power Solutions