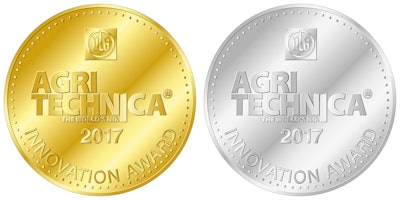
The trend towards further automation of processes – coupled with intelligent data management systems to optimize the regulation and control of equipment, logistics, documentation, quality assurance and traceability – is proceeding unabated in agriculture. This is demonstrated by the more than 320 new product registrations the DLG (German Agricultural Society) has received for this year's Agritechnica.
The terms Cloud Computing and Big Data have entered the common parlance, and in addition to 4.0, the digitization and networking of the value chain in agriculture is becoming increasing important. It is appropriate, therefore, that a Gold Innovation Award at Agritechnica 2017 goes to the first fully automatic tangential threshing system that uses sensors to adjust itself to suit crop conditions and achieve optimum results.
Classic engineering, however, continues to result in products with benefits for the entire agricultural sector, and this year’s second Gold Innovation Award goes to a maize header with an integrated stubble mulcher. This development helps control the corn borer, a significant pest affecting maize crops, and results in an overall reduction in the use of pesticides.
Elsewhere in the awards, there is a clear trend towards adapting existing, innovative solutions already used in other industries so they can be used in agriculture. Examples include Silver Innovation Awards for e-mobility, a height-adjustable operator’s cab, intelligent networked vehicles and augmented reality applications.
Among the other targets of new and further developments that received special appreciation from the DLG Innovations Jury were new ways of making operators’ jobs easier. Thanks to innovative solutions, there has been a continuing reduction in long hours of monotonous, very tiring and complex work for operators, and these tasks will eventually be taken over entirely by the new technologies.
Overall, the DLG Innovations Jury has recognized two innovations with the Agritechnica Gold Innovation Award 2017, and 29 innovations with the Agritechnica Silver Innovation Award 2017. The full list of awards follows:
Gold Agritechnica Innovation Award 2017
CEMOS AUTO THRESHING - the autonomous threshing system for CLAAS straw-walker and hybrid combine harvesters
Claas-Vertriebsgesellschaft mbH, Germany – Hall 13, Stand C02
Currently operators have to find out by themselves which settings strike the best balance between the optimum drum speed, the optimum concave gap, the suitable aggressiveness of threshing and the quality of the grain. Some operators find this complexity too difficult to come to terms with, and find setting up the combine a chore. Consequently, very often a combine is not set up perfectly to suit the current harvest conditions.
Cemos Auto Threshing is the first system that sets the tangential threshing system on straw walker and hybrid machines automatically. As such, it makes a significant contribution to optimizing the quality of work and performance. Depending on the strategy entered into the system by the operator, it sets the drum speed and the concave gap for optimum results in the current harvest conditions. The USP of the entire system is the fact that all controllers communicate with each other. For example, the throughput controller operates via a special communication module to control the throughput relative to the threshing controller, as well as the separation and cleaning controllers.
Another module in the system is Auto Threshing, which for the first time completes the enormous complex technical step to implement fully automated threshing. On such a harvester, users no longer need to know which settings they have to make to get the desired results. Instead, they enter the harvesting strategy, which is then used by the auto-learning system to optimize all parameters. This innovative automation technology allows combine harvesters to continuously combine at maximum efficiency.
StalkBuster
Kemper Maschinenfabrik GmbH & Co. KG – Hall 13, Stand C31
Developed jointly with:
John Deere GmbH & Co. KG – Hall 13, Stand E30
Since the corn borer spread across Germany about 15 years ago, it has become the most notorious pest in silage maize crops in the country. It causes losses in yield and quality, because the cobs do not develop well, and they become infested with Fusaria which may then spread to the following wheat crop. One of the most important methods to fight the pest, along with chemical and biological options, is to chop the maize stubble thoroughly and immediately after the crop is harvested.
The Kemper StalkBuster is the first stubble-destroying technology that forms an integral part of a maize header. It is the only machine on the market that destroys all the stubble before it is driven on by the forager or the tractor and trailer. Usually about 30% of the stubble remains intact, and as the corn borer winters inside it, a high percentage of undestroyed stubble offers them a haven so they can infest the area again the following year. The corn borer pupates in the stubble in spring and the moth starts infesting the new crop after that.
The topper is integrated in the header, is relatively lightweight and has a relatively low power input requirement. This means no extra limitations apply for legal road transport.
The Kemper StalkBuster is a technical solution that offers great benefits for users, their productivity and the environment.
Silver Agritechnica Innovation Award 2017
Fliegl Büffel overloading station for haulm crops
Fliegl Agrartechnik GmbH – Hall 4, Stand B43
Forage wagons may offer better fuel efficiency and performance than forage harvesters, but the drawback is that they are not productive during road travel, that is, the cutting system is not at work. The Fliegl Büffel is a loading platform with a rotor and an intermediate hopper, and which combines various components from a forage wagon (pick-up, rotor cutter), a baler (intermediate hopper) and a forage harvester (unloading system). The innovative rotor-based overloading system with intermediate hopper picks up the haulms, cuts and feeds them into the intermediate hopper, from where the material is overloaded onto a trailer. Serving as a feeder unit, the Büffel is never idle and never involved in transport work. It chops the forage very efficiently and reduces soil compaction. Overloading the crop onto ferrying trailers allows farm managers to tailor the harvest fleet to the necessary road work and the capacity of the rotor cutter/loader platform.
Consequently, the Fliegl Büffel is a new, cost-effective and very efficient alternative to rotor cutter forage wagons and forage harvesters.
AXION 900 TERRA TRAC semi-tracked and fully suspended tractor
Claas-Vertriebsgesellschaft mbH, Germany – Hall 13, Stand C02
Tracked and semi-tracked tractors are rarely used for swift road travel because they offer very little operator comfort. While wheeled tractors offer significantly better comfort in road work, high-power models cannot offer the level of soil protection provided by a tracked machine.
The semi-tracked Claas Axion 900 is the first tractor that has a suspended front and rear axle. This brings a significant improvement in operator comfort compared to triangle-design semi-tracked tractors. The Claas Axion 900 semi-tracked model also has a substantially larger contact area compared to Triangle tracks, which results in excellent directional stability, both in the field and in swift road travel.Optimum adaptation to the ground contours is key for low compaction. This is achieved by a 15-degree pivot range, and the fact that the machine weight is distributed to all track rollers hydraulically. The pivot point was moved forward, which shifts more weight to the rear axle. This benefits from a larger contact area and so can transmit tractor power to the ground more effectively while keeping compaction low.
The machine transfers more than 450 hp engine power to the ground without causing damage to the soil. At the same time, it does not exceed the statutory road width limit.
EZ Ballast Wheels
John Deere GmbH & Co. KG – Hall 13, Stand E30
For tractors to develop sufficient traction in heavy draft work, it is necessary to ballast them in the optimum way. The front axle is ballasted by attaching weights in the front linkage, which is usually easy and safe to do on today’s tractors. The rear axle is ballasted with up to 1,000 kg wheel weights. The drawback of this solution is that these weights are difficult to attach and remove, and very cumbersome to handle – a time-consuming and hazardous approach. A much simpler solution is EZ Ballast Wheels. These weights are fitted to the wheels with a pallet fork and without bringing the wheels into the proper position first, which eliminates the need of jacking the tractor. Once fitted, the wheel weights are secured with toggle levers instead of bolted down. This means they are quick to attach and remove by a single person, and so ensure optimum ballasting in every job. As such, EZ Ballast Wheels make a significant contribution to fuel efficiency and soil protection.
CEMOS for tractors – operator assist system optimizing tractor/implement set-up
Claas Vertriebsgesellschaft mbH, Germany – Hall 13, Stand C02 Claas' CEMOS terminal.
The complexity of a modern tractor can be overwhelming to uninitiated operators. This applies especially when a software menu is not very intuitive to navigate, but rather suits the development requirements of the manufacturer. Claas CEMOS is an interactive system that offers a user-friendly approach to optimize the setting-up of traditional tractor-implement combinations. The system guides the operator through the settings menu – before and during work – using every-day farming language. The system takes into account both the settings entered by the operator and the settings recommended by the manufacturer. In work, it is constantly working to optimize the current settings of the tractor and the implement. To do that, it makes suggestions to the operator after validating the various options. The operator is free to accept or reject the suggestions in line with the targeted quality of work.
Read more about the CEMOS system's use in Claas' LEXION combines.
The expertise that is built into CEMOS allows unexperienced operators to utilize the combination to its optimum potential with respect to the quality of work, work rate and fuel efficiency. In addition, the system is ready to plug into future automated-and-assist systems.
VarioPull
AGCO GmbH – Fendt, Hall 20, Stand A26a
The distribution of weight on a tractor’s rear and front axles is defined by drawbar load, drawbar power, ballasting and the traction booster if fitted. With a specific implement attached, the weight distribution is always the same. VarioPull alters the implement’s attachment point – on the move, on a horizontal plane, and bringing it flexibly up to within 80 cm of the tractor’s rear axle. As the attachment point moves closer to the rear axle, the weight distribution is optimized and road stability increases. For example, the operator can shift the attachment further to the rear to provide more space for the drawbar to make headland turns. The system allows operators to reduce the front weight and hence the tractor weight, which in turn increases fuel economy and protects the soil.
e100 Vario
AGCO GmbH – Fendt, Hall 20, Stand A26a
Electric bikes and cars have increasingly arrived on the market, but the technology has not been available for commercial vehicles so far. This is attributed to the challenge of developing high-performance battery technology that suits the needs. This battery-powered tractor is a world first and was developed to serve in a wide range of applications. Using the powertrain of a 50 kW Vario model, it replaces the combustion engine, the exhaust, air and fuel systems and the radiator by a battery block, a compact electric motor and the necessary electric control system. The 100 kWh, high-voltage battery charges quickly and stores enough power to work for four hours at an average workload. An innovative thermal management system that comprises a heat pump ensures the cab temperature is controlled efficiently. The battery pack can also serve as intermediate storage for farm-generated power.
The modification does not affect the tractor’s suitability for taking on any type of implements. The exhaust-free and very quiet machine is ideal for use in buildings, but also for transport work in cities.
MARS - Mobile Agricultural Robot Swarms
AGCO GmbH – Fendt, Hall 20, Stand A26a
There has been much discussion on whether the trend in farm machinery manufacturing will continue towards ever bigger and more powerful individual machines, or to “swarm” solutions, that is, many small machines. The Fendt MARS System is the first marketable application of swarm technology in agricultural engineering, and thus presents a completely new solution. The system relies on a number of small, auto-steered and electric units that are deployed for maize drilling.The autonomous units are filled with seed by an operator, who also monitors their operation and who hauls them to the field on a trailer. Operating at very low noise levels and without lights at night, these units are suitable for drilling fields near villages and homes 24 hours a day. Manufactured to a cost-saving concept and weighing as little as 40kg each, the swarm units coordinate their work in the field, reduce compaction and minimize the hazard that big machines pose to humans and the environment. The robots log all job data into the “Cloud”, and communicate with each other and the operator.
Camera supported seedbed preparation
Pöttinger Landtechnik GmbH, Hall 27, Stand C39
Jointly developed with:
New Holland Agriculture, Italy – Hall 3, Stand D10
Josephinum Research, Austria
When operators want their power harrow cultivator drill to produce a consistently fine and consolidated top tilth on sites with varying soils, they have to set up the tractor’s ground speed and the power harrow speed manually, and then will still need to intervene manually as they work, which is very tiring and not very effective in extremely varying soils.
This technology now introduced by Pöttinger uses cameras that take real-time footage of the surface and its degree of “cloddiness.” The operator enters a target value and the actual cloddiness is measured behind the power harrow. This reading is transmitted to the job processor, which sends it the implement’s ECU. The system will then automatically control the tractor ground speed and the power harrow PTO speed (“closed-loop control“) to produce the selected level of top tilth. The system creates a uniform seedbed even in varying soils. At the same time, it reduces operator fatigue significantly. This automatic tractor/cultivator drill control system that works relative to the quality of work being achieved is a new development.
GPS-based and automated body-lift-out feature optimizes ploughing results
KUHN Maschinen-Vertrieb GmbH – Hall 12, Stand C05
The working width on ploughs has increased constantly in recent years. These wider widths, however, leave a Z-shaped ploughing pattern on the headland when the bodies are retracted and the plough is raised. This makes it difficult to plough the headland neatly, while crop residues and volunteers are not properly incorporated, leading to volunteer growth in the following crop. Kuhn’s “Section control” is an electro-hydraulic control system that uses the hydraulic, non-stop break-back system to control the individual bodies based on GPS positioning data, raising and lowering them automatically. The system leads to an absolutely straight furrow edge were there used to be a “Z.” The straight edge is a boon for the following work, such as headland ploughing, drilling, spreading and spraying, and ensures crop residues are effectively incorporated – an enormous plus for field hygiene.
Overall, the system reduces operator fatigue and takes load off the rear axle, the rear wheels and the couplers. Added to this, it can also varies the number of plough bodies in work to suit individual tractor powers and soil conditions.
LevelTuner
Landmaschinen Wienhoff GmbH – Hall 23, Stand B39
The center of gravity varies greatly on slurry tankers when they are fitted with different applicators of different weights. This also affects the drawbar load. As a result, drawbar load may quickly become negative in empty runs – a fact that has accounted for serious accidents on public roads in the past, where ball hitches worked lose after operators forgot to secure them. On multi-axle slurry tankers, the LevelTuner automatically alters the air pressure inside the bellows on the front axle, thereby adjusting the pressure relative to the drawbar load that is measured by the drawbar suspension system. This way, the drawbar load is always good and road stability is better. In addition, the system ensures field traction is always sufficient during spreading as the tank is being emptied. Unlike existing options (for example variable-width axles), this center-of-gravity shifting system operates automatically without operator input.
Swing Stop pro
Amazonen-Werke H. Dreyer GmbH & Co. KG – Hall 9, Stand H19
Developed jointly with:
Rometron B.V., The Netherlands – Hall 9, Stand H19
Accuracy of application is key in chemical spraying. The higher the accuracy, the better the plant coverage at the desired product concentration levels. Moving the boom horizontally fore and aft, and in parallel to the ground, has a particularly good effect on spray accuracy. SwingStop pro combines the boom’s active shock absorbing system with very dynamic rate control on every single nozzle and achieves an unprecedented level of accuracy in direction of travel and across the full spraying width. The “pro” specification has new valves on every nozzle that constantly control the current application rate and bring it back into balance. SwingStop pro controls the application rate by using sensors that measure the relative application rate on each nozzle and relate the measurements to the sprayer’s ground speed in real time. This makes SwingStop pro the tool for achieving maximum spraying accuracy. The technology is another milestone on the road to precision farming.
ESV Electric Shut-off Valve
Lechler GmbH – Hall 8, Stand B20
The best solution in precision spraying is currently an individual nozzle control system that operates the closely spaced nozzles relative to their current GPS position. Pneumatic valves are technically very difficult to make and require an extra air system on the tractor.The Lechler ESV (Electric Shut-off Valve) unit comprises a valve, an electric line and a connector for straightforward and fail-safe installation on all regular single- and multi-nozzle holders. The nozzle opens and closes rapidly, and CANbus controlled. Its responsiveness and great application accuracy allows ESV to be easily integrated in smart farming systems, and used on 25 cm sections with uniformly spaced nozzles, for example.
Fitted by connecting the electric lines, ESV offers easy and fast installation. Lechler ESV valves offer reliable and profitable operation and thus great user benefits.
Stereoscopic row-crop CULTI CAM camera on mechanical hoes
Claas-Vertriebsgesellschaft mbH, Germany – Hall 13, Stand C02
Developed jointly with:
Einböck GmbH & Co. KG, Austria – Hall 11, Stand B05
Thomas Hatzenbichler Agrotechnik GmbH, Austria – Hall 11, Stand D42
Bednar FMT, Czech Republic – Hall 12, Stand B05
Carre SAS, France
Chemical spraying is increasingly viewed very critically by the general public, consumers and policy makers. In this context, mechanical weed control in row crop is experiencing a comeback. Quality and efficacy of the mechanical work is achieved by the hoe’s side shifting frame that is controlled in the row by a robust system. Up to now, this type of control has been implemented by 2D color screen cameras. The CULTI CAM system from CLAAS employs just one camera with two lenses (stereo camera) for 3D footage of the crops. At the same time, the 2D color segmentation algorithms have been refined and an automatic camera height and angle detection feature has been implemented. By operating a proportional valve on the hydraulic frame, the frame aligns the hoes in parallel with the rows. The system also feeds any information on less-than-optimum performance to the operator
The benefits of CULTI CAM include more rugged and yet more accurate row control on sites with a heavy weed burden across the full width. This is attributed to the fact that it profiles the field along the ridges, irrespective of the leaf coloring. As another benefit, the hoe can also be used in windy weather and into small crops. It reduces operator stress and the use of chemicals, while allowing for higher work rates and earlier hoeing in the year. In addition, it reduces losses due to steering errors.
Tractor integrated implement steering with Infield auto system for high-capacity hoes – AutoTrac Implement Guidance
John Deere GmbH & Co. KG – Hall 13, Stand E30
Developed jointly with:
MONOSEM, France – Hall 11, Stand C54
Mechanical pest control in row crops is becoming more and more important as chemical spraying is viewed ever more critically by the general public. This has caused a rethink of existing machine concepts. AutoTrac Implement Guidance is an active steering system for row hoes that is controlled from the tractor and provides accurate control between the rows and without using a traditional shifting frame. Instead, the hoe is shifted by the tractor’s hydraulic three-point linkage stabilizers. These stabilizers are controlled by a tractor integrated control circuit that provides feedback on their current position. The control system uses the camera signal from the hoe and calculates the distance between the mounted hoe and the detected rows of crop.In addition, hydraulic coulters are lowered into the ground behind the tractor to absorb the side draft that develops as the hoe moves to either side, thereby improving the functionality of the system, especially on slopes and at high work rates. Depending on the quality of the signals, the system also controls the ground speed of the tractor. It also has an interface for monitoring and logging positioning parameters of the system.
By refining the shifting frame, it has been possible to move the implements closer to the tractor, which in turn improves the stability of the side-shifting control mechanism.
MultiCoater CM 300
PETKUS Technologie GmbH – Hall 6, Stand E40
Wetting in seed coating should be as uniform as possible and is, in fact, achieved by traditional seed coaters through intensive mixing of dressing and seeds. As the seed coat dries over time, it is increasingly at risk of rubbing off, which leads to high Heubach rates, that is a high levels of airborne seed treatment dust.
The MultiCoater CM 300 is a system that treats the coated seeds particularly gently inside the mixing chamber and dries them here too. This has been made possible by a special air cushioning technology in combination with metal-free deflectors. The MultiCoater coats and dries the seeds at the same time, it improves the seed flow and guarantees gentle treatment through optimal and uniform wetting. At the same time, it drastically reduces seed stress due to friction, thereby reducing the development of seed treatment dust substantially. As a result, the Heubach rates drop significantly below the statutory limits. In this way, the system contributes to implementing the strict rules on resistance to abrasion and protecting the environment.
The first pro-active and automatic combine setting system
New Holland Agriculture, Italy – Hall 3, Stand D10
Maintaining maximum throughput levels while keeping losses and the percentage of damaged grain at acceptable levels is a massive challenge and a strain to every combine operator who spends the whole day in the cab. In an effort to reduce operator fatigue, New Holland has introduced the first combine that looks ahead. To do this, it is first necessary to program the following data into the combine: past yields, field topography and all combine settings based on GPS positioning data. During the first pass of the following harvest campaign, the system can then interpolate these data and the setting system responds rapidly to varying conditions. The proactive system relies on traditional sensors and control systems that have been supplemented by a new pressure sensor on the cleaning system that measures indirectly the load on the sieves. The amount of time the material spends inside the threshing and separation areas in the rotor housings is controlled by adjusting the angles of the guide rails. This technology has a bigger impact on the rotor speed and the efficiency of an axial-flow combine than changing the concave gap. It offers operators three different harvesting strategies to choose from. Using the data stored into the system, the combine will optimize its settings by itself – and before the header actually starts cutting and taking in the crop.
IDEAL combine
AGCO International GmbH, Hall 20, Stand A26
Developed jointly with:
AGCO GmbH – Fendt – Hall 20, Stand 26a
AGCO Deutschland GmbH – Massey Ferguson – Hall 20, Stand A 26b The AGCO IDEAL combine.
As high-capacity combines continue to increase in size to boost productivity and efficiency, road transport width is becoming the limiting factor in this development. This is seen especially on the running gear and the large contact areas that are necessary to protect the soil. The IDEAL combine from AGCO is the only high-capacity combine that does not exceed the 3.3 m transport width and still uses ground-friendly running gear. This is achieved by limiting the threshing width to 1.4 m. The system comprises two axial rotors of 4.85 m in length and extra-long, 0.6 m diameter threshing and separation concaves as well as up to 480 kW engines. Smaller IDEAL models have only one axial rotor. The IDEAL combine from AGCO is the first combine in years that was developed from scratch and that features special technology. Further award-worthy features include fully automatic header attachment with header identification so that the settings of the particular header are retrieved. The novel preparation and return pans are segmented and provide up to 15% side slope levelling. A new sensor system detects the separation processes on the threshing and separation concaves and on the cleaning system, and provides the necessary database for an automatic machine set-up. The IDEAL combine from AGCO is the first combine in years that has been developed from scratch and that features special technology.
SmartTurn
Holmer Maschinenbau GmbH – Hall 24, Stand A24
Developed jointly with:
Reichhardt GmbH Control Technology – Hall 15, Stand F45
Tractor headland management systems record sequences of repetitive functions and allow operators to retrieve them automatically either by pressing a button or based on GNSS positioning when approaching a specific area in the field. Reichardt and Holmer exxact have now developed an integral software solution that automates the full headland turn of a beet harvester including raising and lowering the lifter unit and carrying out the turn. To achieve this, the two companies combined the mechanical row guidance system including headland management from Holmer exxact with the GNSS controlled version from Reichardt, and tailored the new system to a self-propelled tanker harvester – in this case the Holmer Terra Dos T4. The innovative solution optimizes all headland turn maneuvers in the field to be harvested, thereby minimizing field traffic and therefore reducing compaction, losses, non-productive times and costs. Its greatest benefit is, however, reduced operator stress – not only during night work.
Ventor 4150 – self-propelled four-row potato harvester with world-leading lifting system that doubles capacity
Grimme Landmaschinenfabrik GmbH & Co. KG – Hall 25, Stand F13
Like many other farm machines, the development of high-capacity potato harvesters for higher performance and efficiencies is limited by the sheer physical size of the machines and the 3.5 m road width restriction. Grimme has now implemented its extremely gentle soil and haulm web system on the Ventor 4150 potato harvester, a four-row and self-propelled machine that stays within the 3.5 m transport limit. The two intake web lines that feed the tubers into the machine are followed by a first web that is made up of two separate belts. These are followed by a second endless and steep elevator web with a wide-mesh and pegged trash removing web. At the end of the line, the two streams of crop leave their individual systems and flow into the trash separation units on the right- and left-hand side, which offer sufficient capacity and stepless adjustment to ensure high throughputs and very gentle crop treatment. A folding mechanism (patent applied) folds the two trash separation units into the machine so it does not exceed the transport width of 3.5 m.
Sensosafe
Pöttinger Landtechnik GmbH – Hall 27, Stand C39
The beginning of the harvest seasons poses great risk to fawns and game in general, because the time of the first cut usually marks the beginning of the breeding season. The techniques and methods developed up to now to save game have not proven very effective. An effective new system however is Sensosafe, a sensor bar that is installed to the header and that detects any wildlife hidden in the field to protect it from fatal injuries. The sensors are optical infrared sensors with integral LED lights that detect animals while the machine is moving. As soon as an animal is detected, the hydraulic system of the header is signaled to raise the unit. The wildlife is saved and the crop is not contaminated. The infrared sensors are bespoke developments for this specific application, and are able to detect fawns effectively also in bright daylight and sunlight, while ignoring other obstacles like mole heaps.
LiftCab
Maschinenfabrik Bernard Krone GmbH & Co. KG – Hall 27, Stand G21
As modern and high-yielding maize varieties reach growth heights of 4.0 m and more, forager operators feel like driving their machines “up against a wall of maize plants” all day long.
The Krone LiftCab is a feature that allows operators to raise the entire cab by up to 70 cm. The feature reduces operator strain and provides a convenient overview of the crop and the harvest fleet. The space underneath the cab also offers easy access to service and maintenance points. The cab lift is a novel feature on a forage harvester.
It significantly reduces operator strain as it frees operators from driving up against a full-width wall of crop all day long. In addition, he can easily spot hazardous situations.
Flexwave Grain Silo Unloading System
GSI Hungary Kft – Hall 20, Stand A26j and Hall 6, Stand E33
Flat-floor grain stores offer higher storage capacities than outlet-funnel grain stores of identical heights. The drawback about flat stores, however, is they never empty completely and a cone of residual grain remains in the bin. To clear out all grain it is necessary to bring in mobile augers, which in turn need manual feeding at some point – a dusty, time-consuming job and heavy work that is dangerous, too, because the running augers present a risk of injury. A new approach is the Flexwave Grain Silo Unloading System which is made up of two air cushions. These are installed inside the store and to both sides of the outlet feeder. The cushions are not inflated at installation time. They cover the floor and reach up the wall to a height that is level with the tip of the grain cone that is formed during emptying. When the store is filled the cushions are flat on the floor and wall. During emptying, the grain initially flows by gravity to the outlet feeder. Yet when the grain stops flowing the first cushion fills with air. As it does so, it pushes the heap away from the wall and to the middle of the store. After the first half of the bin is completely empty, the process starts over on the other side of the bin; before this happens, the air inside the first cushion is released. At the end of the process, the two empty cushions are pulled back into position by ballasted straps. The emptying process is monitored remotely, and so it is possible to refill grain stores without people having to go in to ensure thorough emptying. The Flexwave Grain Silo Unloading System is a very straightforward solution that can be retrofitted to existing non-funnel flow bins with flat floors. It empties the store completely without time-consuming and hazardous manual work.
SmaArt Camera System for automated blossom thinning with Darwin
Fruit-Tec Adolf Betz – Hall 21, Stand E10
The regulation of the amount of fruit on a plant or tree, that is blossom and/or crop thinning, is one of the most important measures used in intensive commercial fruit growing for achieving the required fruit size and quality in marketing. The greatest challenge for mechanical blossom thinning is the evaluation of the degree of thinning and the optimum adjustment of the spindle speed. The Darwin SmaArt Camera System replaces the subjective estimation of the blooming strength with the eye with objective detection by camera. To do this, a camera in front of the thinning spindle detects the blossom density of each individual tree and passes on the data to the on-board computer in real time. Using a thinning algorithm, the computer then calculates the optimum spindle speed and controls the thinning unit. The thinning unit consist of a spindle on which six rows of cord bars are arranged that remove the blossom through rotation. The thinning intensity is controlled to a great extent by the spindle speed. As an option, the system can be combined with a GPS receiver. Using the GPS system, it is possible to detect each individual tree and to assign the data, such as the number of blossoms and the spindle speed, to the tree and to compare it later with the yield data.
As a mechanical system, the Darwin SmaArt Camera System for automated blossom thinning can replace chemical or manual blossom thinning. With its high efficiency and the degree of thinning based on objective parameters, the previous main reasons for the reluctant acceptance of mechanical blossom thinning is expected to diminish.
Beacon+GPS+Sigfox – Fliegl COUNTER SX / Pöttinger PÖTPRO Guide
Fliegl Agrartechnik GmbH – Hall 4, Stand B43
Jointly developed with:
Pöttinger Landtechnik GmbH – Hall 27, Stand C39
So that food manufacturers can verify the route the product takes from the field to the consumer in accordance with the EU regulations, for many years now Fliegl has focused on beacons, which in their original form are small, inexpensive Bluetooth transmitters for machine recognition. With Fliegl COUNTER SX, the beacon technology has been considerably expanded with additional functionalities, enabling an inexpensive, flexible entry into smart farming technologies with major benefits. The COUNTER SX uses the innovative radio technology Sigfox, 3D sensors and GPS, that go beyond previous functionality. With the data radio network, Sigfox is a very inexpensive continuous Internet connection, and therefore provides automatic communication between the machines and the farm independently of mobile networks. It records movements of the machines through the intelligent evaluation of the 3D acceleration and tilt sensors integrated in the beacon. Then it analyses them with corresponding algorithms of a broad range of processes, assigns them and saves and transmits the information collected. Thanks to decreasing unit costs and simplified application integration, beacon technology is recommended for use in agricultural applications. As a universal system, beacons can close a broad range of information and documentation gaps. When a grubber is used, it can, for example, recognize the state of work, transport or break, enabling it to determine detailed operating times. When pressing round bales, it can also record the bale output and the placement location of the bales. However, it can also be used for other applications like theft protection, tracking or temperature monitoring.
Farmdok – automation of agricultural recordings with smartphones
Farmdok GmbH – Hall 15, Stand G10
The recording requirements for agricultural operations continue to increase. These present farmers with new challenges, however the data that is documented and processed can also be used to improve company management and operational development. It is always necessary to have complete and plausible data, and the easier the data collection system is to operate, the more likely it is that detailed and accurate information is recorded.Farmdok is agricultural software for the mobile and automatic documentation of agricultural data in the field with a smartphone and/or tablet. The innovative sample analysis of cultivation and GPS data enables virtually complete automation of data acquisition. The Farmdok TaskPrediction algorithm measures parameters including operating materials, quantities and machines used. The data to be collected is automatically proposed at the start of each job; as a high probability of the planned measures can be achieved at this point thanks to comprehensive data analysis.The WorkCognition algorithm is used for the reliable detection and determination of the cultivated area using a far-reaching driving pattern analysis without the need for geo fences. This enables road and field work to be differentiated, and applied loads to be counted. The farmer benefits from time saved and more convenient recording with minimal operating effort. The easy-to-operate system requires no additional hardware, and therefore enables an inexpensive entry into farm record digitization for farmers, machinery rings or contractors.
agrirouter
DKE-Data GmbH & Co. KG – Hall 15, Stand G38
Jointly developed with:
AGCO International GmbH – Hall 20, Stand A26 and Hall 15, Stand G38k
Amazonen-Werke H. Dreyer GmbH & Co. KG – Hall 9, Stand H19 and
Hall 15, Stand G38c
Grimme Holding GmbH – Hall 25, Stand F13 and Hall 15, Stand G38h
HORSCH Maschinen GmbH – Hall 12, Stand C41 and Hall 15, Stand G38i
Maschinenfabrik Krone Beteiligungs-GmbH – Hall 27, Stand G21 and Hall 15, Stand G38e
KUHN S.A. – Hall 12, Stand C05 and Hall 15, Stand G38l
LEMKEN GmbH & Co. KG – Hall 11, Stand B42 and Hall 15, Stand G38j
PÖTTINGER Landtechnik GmbH – Hall 27, Stand C39 and
Hall 15, Stand G38f
Rauch Landmaschinenfabrik GmbH – Hall 9, Stand D16 and
Hall 15, Stand G38g
Same Deutz–Fahr Deutschland GmbH – Hall 4, Stand D28 and
Hall 15, Stand G38m
In the course of additional digitization of agriculture, the majority of large companies try to ensure customer loyalty with corresponding proprietary solutions. In contrast to this, small and medium-sized companies are hardly capable of mastering this technical challenge on their own. However, for farmers themselves the primary focus is also on the critical topics of data security and data sovereignty.The agrirouter is a universal data exchange platform for farmers and contractors that combines machines and agricultural software across all manufacturers to simplify operating procedures and improve economic efficiency. Only the user can specify who exchanges which data with whom and for how long. The following always applies: The agrirouter transports data, it does not store it. As a result, all available data is brought together for the first time in cooperation with corresponding farm management systems. The agrirouter therefore makes it easier for the farmer to take a major step toward digitization.
SmartService 4.0
Amazonen-Werke, Germany – Hall 9, Stand H19
Ever more complicated machines also necessitate increasingly more specialized training for service technicians. However, workshop employees often have to carry out repair and/or maintenance work on-site in order to avoid long downtimes, for example, until the factory customer service arrives. In the environment of increasingly more complex machines, AMAZONE SmartService 4.0 uses the technologies of "virtual reality" and "expanded reality" to further develop the learning and training processes for the end customer and customer service, and to support customers and service technicians during maintenance work. AMAZONE Smart-Service 4.0 enables both multimedia-based, technical real-time support from service specialists for service technicians, as well as in the field of applications technology from service consultants for end customers. With real-time support, the service specialist/service consultant sees the activities of the service technician/end customer and can provide corresponding warnings and/or working instructions. This would not be the case purely with support over the phone.
Telematics Large Vehicle Alert System warns car drivers of agricultural machines in road traffic
Claas-Vertriebsgesellschaft mbH, Germany – Hall 13, Stand C02
Agricultural vehicles in road traffic generally have a bad reputation among non-agricultural road users. Many car and truck drivers become uneasy when they encounter slow-moving, often unwieldy agricultural machines or tractors towing trailers or equipment on narrow roads or on blind curves – quite apart from the accident potential of such situations.
The Telematics Large Vehicle Alert System from Claas is the first traffic safety system that proactively informs drivers of networked cars on the position and status of agricultural machines on their route. For this purpose, the location of the agricultural machines is transmitted from the telemetry data via telematics or via a Claas app to the assistance systems of cars and trucks virtually in real time. With the open data standard, a broad range of navigation systems can access the data stored by Claas, enabling them to report any warnings to road users. The population can be notified of disruptions more vigorously with these kinds of active systems. This already enables hazards to be prevented beforehand or achieves improved acceptance when using large machines, as traffic safety systems have a major effect for agriculture.
Smart Crop Damage Identification – intelligent identification system for crop damage caused by game
Agrocom Poland – Hall 15, Stand J12
The ordinary estimation of damage caused by hunting and storms (hailstorms, intensive precipitation, night frost, ground softening and flooding) is difficult, labor-intensive and time-consuming, inaccurate and therefore hardly representative. An unclear estimate of damage is often the cause of conflicts between those incurring damage and, for example, insurance companies. However, a three-dimensional imaging process, such as the intelligent identification system for crop damage caused by game called Smart Crop Damage Identification (SCDI), provides a solution to this problem. It can record hunting and natural damage at the end of the vegetation period, even for tall plants, and makes an assessment and/or damage estimate possible. SCDI works with 3D images that are taken with drones at a low height. For this purpose, parallel paths are created at stable altitudes with photographic longitudinal directions using the planning software. In SCDI the images recorded in this way are then combined with existing LIDAR (light detection and ranging) laser data and the damage to the areas is automatically calculated. However, other photographs and evaluations are also possible. Intelligent data acquisition using drones does not prevent work in the fields. The system reduces the working time required by farmers when checking stocks, when looking after animals and for quality assurance.