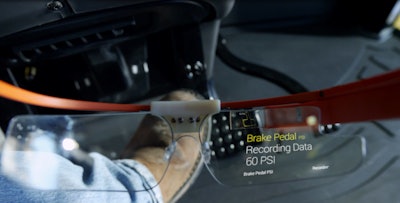
AGCO Jackson Operations, the Minnesota-based manufacturing center for AGCO Corporation, a worldwide distributor and manufacturer of agricultural equipment, is the first agricultural manufacturer to receive the AME Excellence Award presented by the Association for Manufacturing Excellence (AME). The Jackson facility manufactures complex, custom-configured Challenger and Massey Ferguson agricultural machines, including tractors and application equipment. The 2017 AME Excellence Award was presented Oct. 10 at the AME 2017 International Conference in Boston, MA.
AGCO is the only agricultural manufacturer to receive the AME Excellence Award. Adoption of advanced technology such as Glass assisted reality at AGCO’s Jackson, MN, manufacturing center is one aspect of the company’s efforts which led to the recognition from the Association for Manufacturing Excellence.
AGCO was chosen based upon the company’s work converting the Jackson facility to a mixed model line and the quality, efficiency and productivity improvements that resulted in just over 2 years. Empowering employees, adopting new tools and integrating innovative technology using Glass, an assisted-reality, wearable headset device, are key factors leading to the success. AGCO is the only agricultural equipment manufacturer to use Glass technology in its manufacturing processes.
“AGCO is proud to be an innovator and thought leader in the production of agricultural equipment, and we’re honored to be recognized as the first agricultural company to receive this award,” says Peggy Gulick, AGCO’s Director of Business Process Improvement. “The machines we manufacture are built to order, and rarely are two exactly alike. In fact, with our mixed model production approach, an employee may build an engine assembly in the morning and turn to an applicator later in the day.
“For our workers, Glass provides instant access to parts lists, assembly instructions, quality checkpoints and other work instructions for the specific machine on the line at that time. No one else in the agricultural equipment industry is utilizing this technology the way AGCO is, and the results have been phenomenal,” she adds. Mixed model lines also can present difficulties in part stocking, setup, skills and training, Gulick pointed out as she detailed AGCO’s best practices for lean and continuous improvement during a presentation at the AME conference.
Significant Quality Improvements
The new state-of-the-art assembly line with in-process quality testing, and the use of Glass implemented in the past 2 years, resulted in a 40% improvement in early-hour repair frequency for the tractors and applicators manufactured in Jackson. Other improvements achieved within the facility include a 30% reduction in inspection times, a 25% reduction in production time for low-volume, high-complexity assemblies and the ability to train staff 300% faster. Today, AGCO has more than 100 pairs of Glass deployed at the Jackson plant and has begun integrating Glass into other facilities around the world.
Empowered Employees Integral to Success
The AME Excellence Award is sponsored by the Association for Manufacturing Excellence. The award involves a rigorous selection process that begins with an extensive achievement report to demonstrate continuous improvement, best practices, creativity and innovation in manufacturing. Manufacturing facilities then are further evaluated through an extensive site visit during which the achievement report is validated. In selecting AGCO Jackson Operations for the award, AME evaluators commended AGCO’s employees and their continual drive toward operational excellence.
“Our employees take great pride in their work and in producing a quality product, and they see many time-saving, step-saving and process improvement benefits from Glass,” explains Eric Fisher, General Manager, Operations in Jackson. “They’ve embraced this technology and continue to identify additional ways to improve on the production floor. Everyone on the Jackson team is empowered to find better solutions to drive higher quality in our products and processes, and their efforts are certainly having an impact on our results.”