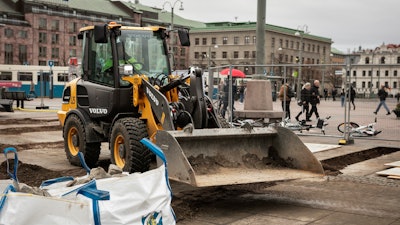
Construction equipment is estimated to generate around 400 metric tons of CO2 emissions per year, representing roughly 1.1% of global emissions. Consequently, decarbonization of non-road mobile machines is considered an important factor in efforts to limit global climate change.
With an increasing number of countries committing to a net-zero carbon future, the construction industry is facing growing scrutiny of greenhouse gas (GHG) emissions. Given the necessity for zero-emission construction machines, a new IDTechEx report, “Electric Vehicles in Construction 2022-2042” forecasts that the global electric construction machine market will be worth $105 billion (CAGR 25.6%) by 2042.
The report analyzes ongoing electrification work over the range of construction equipment types, including excavators, wheel loaders, cranes and telehandlers. It also provides IDTechEx’s independent 20-year outlook for the electric construction vehicle market, with forecasts for sales, battery demand and market revenue by machine type, and separate regional forecasts for Europe, China and the US.
The starting point for most OEMs has been and will continue to be smaller compact machines, whose duty-cycle requirements are relatively light. Shown is a Komatsu electric prototype.Komatsu
The starting point for most OEMs has been and will continue to be smaller compact machines, whose duty-cycle requirements are relatively light, meaning the daily workday energy and power requirement can be met with a practical size of li-ion battery, electric motors and a well-defined charging strategy. Recognizing the potential for electrification in this segment, Volvo CE has already committed to moving its entire range of compact wheel loaders and compact excavators to electric powertrains and ceasing development of new diesel models. IDTechEx predicts other OEMs will follow this lead.
However, excavators over 10-tonnes are responsible for around 46% of the total CO2 emission by construction equipment, making it crucial that zero-emission solutions are developed for large machines. The arduous duty cycles of heavy-duty machines mean those over 20-tonnes need more than 300 kWh of energy to deliver a full eight-hour workday.
Excavators over 10 tonnes are responsible for around 46% of the total CO2 emissions by construction equipment, making it crucial that zero-emissions solutions are developed for large machines.Volvo Construction Equipment
Critical to the deployment of electric machines will be the total cost of ownership. There is a premium on electric machines over diesel, primarily related to the cost of the large battery packs. An IDTechEx analysis in its report “Electric Vehicles in Construction 2022-24” suggests that the extra cost of an electric mini-excavator could be modest enough that diesel fuel savings and reduced maintenance could largely offset the additional premium. But for larger machines, the extra cost of electrification likely remains prohibitive, and OEMs will need significant regulatory and financial support to promote uptake.
While GHG emission reduction is key, there are other important drivers for machine electrification, most notably health and safety issues around diesel engine operation on construction sites. For example, the construction industry in the UK is reportedly responsible for the largest annual number of occupational cancer cases, with around 8% of these directly related to diesel engine exhaust emissions.
Construction is also a high-risk industry for noise-related health issues. Electric machines are significantly quieter, offering the potential for improved communication, safety and productivity on site, while reducing the inconvenience of noise pollution for the surrounding area. The elimination of toxic exhaust emissions could improve air quality on jobsites and in the surrounding vicinity, improving the work environment for construction workers.
Click here to access the full report.