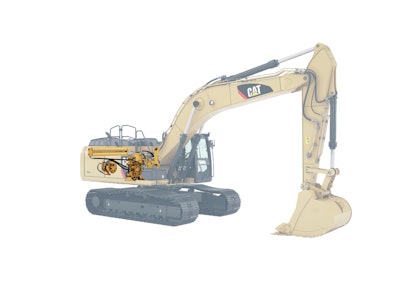
The concept of hybrid technology is to capture wasted energy and reuse it for productive purposes. Recently unveiled hybrid construction equipment designs claim fuel efficiency gains in excess of 20% without any degradation in performance.
Excavators and wheel loaders are at the forefront of this hybrid evolution. Komatsu was the first to introduce a hybrid excavator to the U.S. market, and it currently offers a second-generation model, the 23.8-ton HB215LC-1. Recently, Caterpillar announced its own unique hybrid technology with the Cat 336E H. And while it’s not currently offered outside of Japan, Hitachi (10745042), Tokyo, Japan, has its ZH200 hybrid excavator. This February, John Deere announced production of its 644K Hybrid wheel loader.
The approach differs depending upon the type of equipment and how it is used. First you need to identify where the majority of energy is wasted. For example, with an excavator, significant energy is lost as you swing the mass of the excavator upper structure back and forth on the undercarriage. Accelerating and decelerating this upper structure consumes a lot of energy. With a hybrid excavator, the goal is to capture this energy and put it back to use.
Repetition is key to success
Hybrid technology is often beneficial in repetitive applications. Consider the case of an excavator. The more you swing the upper structure, the greater potential benefit from hybrid technology.
“The Caterpillar 336E will deliver fuel savings in all applications it was designed to perform; however, the best fuel savings will come in high-volume truck loading and trenching where the machine is required to cycle frequently,” says Kent Pellegrini, Product Application Specialist, Caterpillar Inc. (10055175), Peoria, IL. “The more it swings or cycles, the more opportunities there are to store and reuse energy, which leads to more savings and quicker payback for customers.”
The same applies to the Komatsu hybrid. “Since the HB215LC-1 utilizes the energy created during the swing brake motion, applications that require a high amount of swinging maximize the effectiveness of the hybrid technology,” says Brian Yureskes, Marketing Manager for Excavators, Komatsu America Corp., (10633042), Rolling Meadows, IL.
A common misconception about hybrid technology is that performance is sacrificed for fuel savings. “This is not the case with the HB215LC-1, which offers the same high level of performance as its conventional counterpart, the PC200LC-8,” Yureskes asserts. “In addition to the 25 to 40% fuel savings, hybrid technology produces an environmentally-friendly machine that reduces CO2 and greenhouse gas emissions significantly. Noise levels are also reduced compared to a conventional machine, making the HB215LC-1 a suitable choice for urban areas or night work.”
According to Pellegrini, “the Cat 336E H uses up to 25% less fuel than the standard 336E without sacrificing power or productivity. Fuel efficiency—the amount of fuel used per ton of material moved—is also a benefit. Compared to our 336D, the 336E H is 50% more fuel efficient. Using less fuel per unit of work performed also results in a lower carbon footprint, and that benefits us all.”
Hitachi also reports substantial fuel savings (20%) from the hybrid system on its ZH200 compared to the standard ZX200-3 excavator, with a corresponding drop in CO2 emissions.
How they work
Basically, hybrids capture wasted energy, which is then released at the appropriate time to produce useful work. The actual components used depend upon the design of the particular hybrid system.
A few key electrical components form the backbone of Komatsu’s hybrid system. “The electric swing motor, generator motor and ultra-capacitor differentiate the HB215LC-1 from a conventional excavator,” says Yureskes. “The machine body, undercarriage, hydraulics system and work equipment are identical to those found on Komatsu conventional excavators.”
The electric swing motor recovers energy during each swing brake, and stores it in the capacitor to be used when needed. Energy can then be sent to either the swing motor or the generator motor to help the engine accelerate as engine assist. This allows the hybrid to quickly respond to hydraulic power demands. Such responsiveness gives the hybrid the advantage over a conventional machine.
Proprietary machine control logic also contributes to fuel savings. The Komatsu hybrid has a different approach to engine speed management during operation. A low engine idle speed of 700 rpm helps reduce fuel use between work cycles. The electrical engine assist helps the engine and hydraulic system quickly reach the necessary speed to match hydraulic demand.
In a conventional machine, the engine would lug down to peak torque. But with the hybrid system, the engine ramps up to the needed engine speed based on the hydraulic demand. There are other benefits, such as reduced noise. Due to the engine speed management and electrical engine assist, the engine spends less time at high rpm, making its quieter operation ideal for noise-sensitive areas.
The Hitachi ZH200 also uses a hydraulic/electric swing motor to generate electrical power under braking, which is stored in a capacitor alongside the machine’s cooling pack. The electrical power is used to boost slew speed, and also feeds a secondary hydraulic motor to assist the diesel engine when there is a demand for hydraulic power.
Caterpillar uses a different approach by capturing the swing brake energy with a hydraulic accumulator. A large accumulator, squeezed under the hood between the engine and counterweight, is pressurized by house-swing braking. That energy is then used to accelerate the excavator upper structure back in the opposite direction.
The Caterpillar 336E H has all of the same advantages of the 336E, with the biggest difference being greater fuel efficiency. Its design incorporates three building block technologies.
The Electronic Standardized Programmable (ESP) pump smoothly transitions between the hydraulic hybrid power sources, engine and accumulator for efficient engine power management. It also matches pump and engine load to outperform the 336E, even at lower engine speed.
The Adaptive Control System (ACS) valve intelligently manages restrictions and flows to control machine motion with no loss of power, and ensure operators experience no difference in control, hydraulic power or lift capability. The ACS main valve takes the energy wasted in conventional excavators when flow dumps over relief and directs it to circuits that can immediately use the power. It reduces fuel consumption by preventing pressure loss.
The hydraulic hybrid swing system captures the excavator’s upper structure swing brake energy in accumulators and releases the energy during swing acceleration.
The design of the Cat 336E H also allows it to run at reduced engine speeds, which saves fuel and reduces noise in and outside the cab.
The John Deere 644K Hybrid wheel loader uses yet another variation of hybrid technology. A diesel engine running at steady state turns an electric generator. “This machine, compared to our conventional drive 644, uses a smaller engine (6.8-liter),” says John Chesterman, Product Marketing Manager for Wheel Loaders at John Deere (10175527), Moline, IL. “It is 229 hp versus 232 hp. We run at a constant engine speed of 1,800 rpm, whereas a traditional wheel loader will run at 2,250 or 2,350 rpm. We are running at a more efficient point in the engine efficiency curve.”
This provides several advantages. “First off, the engine is always spooled up,” he explains. “We don’t have to worry about response. We have all drivetrain power available.” The engine also runs the hydraulic pump at constant speed so all hydraulic flow and power is available at any time. “That is an advantage over a conventional drive machine.”
“Engines that run generators at constant engine speeds have much longer lives than engines that are constantly hunting up and down the rpm range to make power,” says Chesterman. Also, by turning at a lower rpm the noise generated is reduced. “The noise level of this machine is 68 dB as experienced by the operator, a full 2 dB lower than our conventional machine. In the world of sound, a 3 dB reduction equates to cutting sound power 50%.”
The John Deere power electronics are the brains of the system. This is provided by John Deere Electronic Solutions of Fargo, ND. Three cables connect the power electronics to the electric motor. “All of the power to turn the tires is going through those three cables.”
The electric motor drives a simplified three-speed transmission but the system has four operating speed ranges in forward and reverse. The transmission on the conventional 644 has four or five forward speeds with three reverse. Reverse gears are not needed on the hybrid. “The electric motor operates equally well [in] forward and reverse,” notes Chesterman. With the conventional 644 you have to shift gears to change directions. “We have eliminated that shifting [by] simply reversing the motor. It is very smooth and very powerful.”
The electric system also recaptures some of the energy that would normally be wasted. “If you let off the accelerator and the machine is slowing, that is actually backdriving the motor,” says Chesterman. “When we backdrive the motor it acts like a generator. That power then lightens the load on the engine and reduces fuel consumption. This is common in a tight V-pattern operation. During a V-pattern operation the operator is decelerating and reversing while at the same time raising the boom. In a conventional machine the deceleration energy would be dissipated as braking heat, but in the case of the 644K Hybrid it is used to assist the engine in providing power to the hydraulic system.”
But this hybrid does not use an energy storage device. “Any excess electrical energy goes to the brake resistor,” Chesterman explains. “The brake resistor allows us to dissipate excess energy to prevent engine overspeed."
The 644K Hybrid does not compromise performance. The average customer can expect about a 25% reduction in fuel consumption. “That is a mix of various activities—transport, stockpiling, as well as V-pattern truck loading,” notes Chesterman. “But if they focus just on V-pattern loading they will exceed that fuel consumption reduction. From an application standpoint, this machine is not designed to do anything differently than the typical 644.”
The 644K Hybrid has also proven easier to use. “Operating a conventional machine can be a challenge because to effectively load the bucket the operator has to actively manage engine speed which changes pushing force and hydraulic speed,” says Chesterman. Since the engine on the 644K Hybrid runs at a constant speed the operator always has full driveline and hydraulic power. “That really helps the novice operators be productive since they can very easily push the bucket into the pile and they have the hydraulic power to curl the bucket and very quickly maneuver.”
The hybrid technology also allows adaptation of a few unique features, one of which is coast control. With a torque converter machine when you let off the throttle, the loader free-wheels. With a hydrostatic machine when you let off the throttle you get dynamic braking. With coast control you can select from four settings—from no dynamic braking to dynamic braking similar to a hydrostatic machine.
Another unique feature is Full Rim Pull Control. John Deere wheel loaders currently come with Spin Control. “It is a reactive system,” says Chesterman. “It has four different settings.” When a conventional wheel loader starts digging, it drops engine rpm to keep the wheels from spinning. For the 644K Hybrid, the system has been expanded to Full Rim Pull Control. "We are not changing the speed of the engine. It is just not going to generate as much pushing force or rim pull in certain settings."
The 644K Hybrid uses many of the components of the conventional 644. For instance, the frame is basically the same. “The axles and brakes are identical to the conventional drive machine,” says Chesterman. “We do some things to the counter-weighting of the machine, but this particular model we manufacture in Stage II emissions, Tier 3 emissions, Interim Tier 4 conventional and now Interim Tier 4 hybrid. We always have to do some juggling based on the engine and the aftertreatment device.” John Deere teamed up with industry leading suppliers for the electric motors and drives, but it manufacturers its own inverters as well as the transmission to which the electric motor is attached.
Will this technology be applied to other loaders in the John Deere wheel loader line? Chesterman indicates that this technology is scalable. “We are going to apply the correct technology to the right machine. This technology is flexible.”
Evaluate options
With excavators, there are currently two ways used to capture the swing brake energy: electrically with a capacitor or hydraulically with an accumulator. The Komatsu and Hitachi excavators use capacitors, while the Caterpillar excavator uses a hydraulic accumulator.
The electric excavator hybrids share little in common with automotive hybrid technology. “The way construction equipment operates played a major role in the development of the electric hybrid technology,” says Yureskes. “Construction applications differ from the automotive industry because there is less time for energy to be captured and converted into usable energy.”
To illustrate, take a typical 90-degree swing:
•Swing starts/swing acceleration—approximately 40 degrees
•Swing coasting—approximately 30 degrees
•Swing braking—approximately 20 degrees
“Even if the swing is large (greater than 90 degrees), the degree of swing brake still represents a small portion of the work cycle, resulting in a small window for capturing the energy,” says Yureskes. “By contrast, the automotive industry can use batteries, since the time it takes to accelerate from a stoplight is a few seconds; therefore, the battery has time to convert the chemicals into electricity.”
Capacitors provide the necessary solution. “A capacitor has the ability to capture the energy very quickly so the energy generated in that small window of swing braking is able to be captured and stored,” says Yureskes. “Due to the size of the machine, a large amount of energy is necessary to quickly decelerate the upper structure, and these large forces directly correlate to the amount of energy that is stored. A capacitor allows the machine to convert and use this energy instantaneously.”
Caterpillar weighed the electric and hydraulic options and took a different route. “We considered both the electric and hydraulic paths, and we built prototypes of both and tested them along with competitive machines,” says Pellegrini. “We determined that the most efficient, least complex and easiest to service is the hydraulic hybrid solution.”
By using this approach, there is very little difference between the Cat 336E H and a conventional 336E. “Nearly 98% of the machine is made from the same proven and reliable components used on our standard 336E,” says Pellegrini, “and that gives us economy of scale.”
“Production machines have been tested by operators globally,” he continues. “Productivity studies and customer applications have validated performance. The ‘brains’ of the system, the ACS valve, has been in the field proving itself with superior results for several years. In fact, the ACS and hybrid system have worked well together over thousands of hours of testing.”