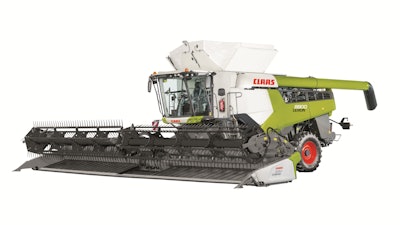
CLAAS has developed a new combine harvester specifically for the North American market, the LEXION 8000-7000 Series. Whereas previously the company would design a machine and North American-ize it, Blake McOllough, Product Manager - Combine at CLAAS of America, says these new combines were “truly designed from an engineering standpoint with what North America wanted.”
“Europeans are starting to figure out that if it works here, usually it will work over there as well,” he says. “Big grain tanks, fast unload, things like that are starting to become more popular in Europe so we’re starting to see it with our [North America] products as well.”
When designing the combine, CLAAS focused its efforts on four key aspects—efficiency, precision, convenience and reliability. Consistency of branding was also important, which is why the combines are now the same green and white colors as its other machines instead of the yellow and black coloring of previous models, a holdover from the company’s former partnership with Caterpillar Inc.
Efficiency
One of the key components aiding the efficiency aspect of the combines is the threshing and separation system APS HYBRID, says Jenna Zeorian, Marketing Specialist-Combine at CLAAS of America. It’s the heart and soul of the LEXION combines, she says. A view of the inner components of the new combine.S. Jensen
When looking at efficiency, one of the main factors for CLAAS and its customers is how many acres per hour can be harvested by the machine. This is why the company updated the APS HYBRID SYSTEM, now called APS SYNFLOW HYBRID. McOllough says the inside of the combines were enlarged to provide more capacity—10% more than the previous series—to increase harvesting efficiency. The extra capacity comes from increased efficiencies on a crop flow basis, as well as enlarged threshing cylinder. Initial testing has shown on average the 8000 can harvest 20.3 acres per hour, and the 7000 18.5; competitors’ combines are in the range of 15.5 acres per hour.
Fuel efficiency was another area of focus for the new machine design. Zeorian says it’s a combination of the machine design as a whole that enables this, as well as Dynamic Power, a new feature on the combine.
Dynamic Power was adapted from the company’s forage harvesters and was tailored for the new combines. McOllough says it’s going to act as a smart engine in which it optimizes the engine’s fuel map as the combine goes through the field to reduce fuel use. “If you're not using your full engine load, it’s not going to use the fuel needed to get to that fuel map,” he explains. “It’s going to take down your power output to ensure you’re not using more fuel than necessary.” It also provides a boost of power when unloading so operators don’t have to slow down the combine and potentially inhibit productivity.
He says the biggest difference for the Dynamic Power system used in the combines versus the one in the forage harvesters is the combine version shifts down fuel usage to achieve fuel savings. In the forage harvester engine rpm can be adjusted to reduce fuel use because it doesn’t have as many components to keep in motion as a combine does.
Also aiding efficiency and improved power output is the use of MAN and Mercedes-Benz engines in the new LEXION series; the company is no longer using Caterpillar engines in its machine. The largest model, the 8800, features up to 610 hp (454.9 kW), a large jump from the previous machine which was 570 hp (425 kW). Each machine in the series, except for the 7500, are seeing an increase in horsepower compared to previous models.
By using MAN and Mercedes-Benz engines, CLAAS is able to consolidate with the rest of its product line, as well as have its dealers certified as technicians for the engines. With the Caterpillar engines there were more restrictions—a different dealer was needed to service the engine or training dealers required them to travel to various locations. The MAN and Mercedes-Benz engines, however, allow CLAAS to bring training in house and dealers will be able to service every single combine.
Exclusive to the North American machines is a wider chassis on the Class 8 models as customers were asking to have that feature back. McOllough says about 45% of the total market for combines is Class 8 machines, so having the wider chassis available will better enable the company to serve the market and expand its customer base.
Other technologies on the new combine brought over from CLAAS machines include the rear axles and the driveline system. McOllough says the company saw the efficiency benefits and power transfer capabilities the driveline was providing in its JAGUAR forage harvesters and decided it could bring those same benefits to the LEXION combines. It’s enabled a reduction in the number of belts necessary on the machine, as well as increased efficiency.
A large grain tank—capable of holding 510 bushels in the largest model—on the combine pairs with a fast unload speed of 5.1 bushels per second to provide improved productivity to farmers. McOllough explains that with a 510 bushel grain tank, if a combine is moving 5.5 mph through the field and unloading 5.1 bushels per second, a farmer has the potential to unload almost 800 bushels with a single click of a button in the operator cab. “If we're able to go a half mile in a 250 bushel cornfield, we can do a quarter mile and be able to turn around and unloading the whole way back so the grain cart is not going to the other end of the field,” he adds. This adds efficiency gains, as well. By not needing the grain cart which collects crop from the combine to follow with every pass through the field, fuel and time savings can be achieved.
CLAAS of America
Precision
Ensuring precise machine adjustments to make the combine fit the farmers’ exact application and crop harvesting needs was an important aspect when designing the new LEXION series. Key to this is incorporation of the company CEMOS AUTOMATIC system which is capable of making precise adjustments with more speed and accuracy than a seasoned operator says Zeorian.
According to McOllough, it’s the consistency of the system which is unbeatable by even the most experienced operators. It can run continually all day, every day without taking a break, and it’s going to run the same at the beginning of harvest as it does at the end of the harvest cycle. “What that brings us is 10% more throughput,” he says. It also leads to less foreign matter getting into the grain tank, more engine utilization, and less grain loss because the machine knows what’s coming into it and can adjust accordingly as it moves through the field.
Since the introduction of CEMOS AUTOMATIC in 2013, CLAAS has continually added more features to the system. Cruise pilot, for instance, monitors the amount of material coming into the machine and changes machine speed based on that. Auto threshing changes the threshing area as needed while auto separation is responsible for automating the separation process as crop enters the machine. The system also includes a grain quality camera which reads material as it comes into the grain tank to ensure there are no cracks or splits. McOllough says these features all work and make adjustments together to automate the harvesting process.
Automation systems will continue to become more of a necessity, he says, as labor gets harder to find for farmers—much the same challenge other heavy-duty industries are experiencing such as construction and trucking.
Individual threshing and separation speed adjustments are another feature Zeorian says sets the new combine apart from other machines. This helps to minimize grain loss and improve grain retention. “We’ve done some studies that compares [the combine] with competitors’ which have a grain loss of about 1.5% whereas with the new machine we’re looking at less than 0.5%,” she says.
“Any machine can push to have the capacity it wants, but at some point to get that highest capacity you’re going to give up something,” says McOllough. Many times those aspects given up are grain loss or fuel usage. However, he says the new LEXION series is perfectly balanced so capacity can be achieved without compromising elsewhere. Being able to make the speed adjustments independently for the threshing and separation enables capacity improvements as well as reduced grain loss and fuel use. A rear camera helps to provide increased visibility around the machine.S. Jensen
In addition, more adjustments are coming from the cab because farmers don’t want to have to stop or get out of the machine. “Harvest windows aren’t big enough to do that anymore,” says McOllough. “So what we need to be able to do is push a button and the machine does what it used to take the farmer a half hour to do.”
Blanking off sections of the thrashing area and changing the rotor configuration are among the many aspects that can be changed by pushing a button in the cab. “Not only does it cut down the amount of time spent doing these tasks, but it also makes sure you can optimize that machine as you're going through the field,” he says.
“All those features are tied to CEMOS AUTOMATIC,” he continues. “It’s getting more control over the configuration of the machine as you're going through the field to make those adjustments. And it's able to tell what those adjustments do to the machine and its performance, and decide if it was the right decision or not much like the operator would.”
“We’re making things easier and making sure people get the most out of their machines,” adds McOllough.
Convenience and reliability
Zeorian says convenience was one of the most important aspects to ensure the new combine met the needs of the North American market. This equates to less daily maintenance to achieve the target goal of saving customers time and money.
One way the company is aiding convenience is enabling the combines to have a transport speed of 25 mph (40.2 kph). Travel time between fields is just as important as in the field, which is why the company increased the speed capabilities of the new LEXION series. The transmission and axles were improved to ensure the 25 mph speed could also be achieved when going up hills.
“It’s a very comfortable 25 mph,” notes McOllough. With the TERRA TRAC system—one of the available configurations for the machine—he says the combine is more narrow going down the road than some track or wheel setups, so farmers don’t have to worry about hitting objects along the side of the road such as mailboxes. They also don’t have to slow down for cars because the setup is narrower than a dual tire machine.
Active suspension within the TERRA TRAC system offers a smooth ride, as well, ensuring comfort for operators traveling at any speed.
To ease the transition between crops, CLAAS has now made it possible for the head to be removed from the front of the machine, as long as the farmer has a second person outside the machine to assist. With the touch of just three buttons, the head can be removed. McOllough says that was one of the biggest features customers wanted and the company had to be sure to provide for the North American market. The automatic central lubrication system ensures components receive the right amount of grease as needed.S. Jensen
An automatic lubrication system on the combine aids both convenience and reliability. CLAAS has improved upon the system from previous iterations by adding more greasers—up to 74—helping to extend greasing intervals. As machines become more precise, having the auto lubrication system also ensures critical components are getting the right amount of grease at the right time, every day. “It’s not only going to prolong the reliability of the machine, it’s also going to reduce the amount of [maintenance] time being spent on the machine,” says McOllough. “And you don't have to trust it to yourself or to someone else that they're putting on the right amount of grease, that system is giving you the right amount of grease.”
There’s also in-cab monitoring of the system to see the grease level and how much is getting pushed out; adjustments to the amount of grease and the intervals at which it’s used can be made if necessary from the cab.
Machine clean off is aided by the DYNAMIC COOLING system. It pulls air in and pressurizes it underneath the side panels of the combine, keeping interior components clean by minimizing dust buildup. This greatly reduces the need for farmers to blow off the machine in order to keep it clean and working correctly.
Traditional cooling systems are located on the side of a machine and pull air from the side then push it into possibly the engine or another system where it’ll exit on the other side. DYNAMIC COOLING, on the other hand, is horizontal and pulls air from the top of the machine so as to not get dust buildup from the tracks or tires. This prevents dirty dust from being pulled into the system.
The air is pushed toward the engine compartment where built up turbulence from a 67 in. (170.2 cm) cooling fan prevents air from escaping and instead causes it to go down the side panels which have vents through which air and debris comes out. This creates further turbulence to keep the air circulating so dust does not have a chance to build up. McOllough says it has a dual purpose—keeping things clean, as well as providing an efficient way to cool the engine and radiators.
A visualization of the combine's DYNAMIC COOLING system.CLAAS of America
It’s a variable speed system, ensuring it only runs as fast as it necessary to keep the machine running optimally. This can save up to 30 hp (22.4 kW) on a cool day which can be used in other systems if needed.
With the DYNAMIC COOLING and automatic lubrication systems and other features, daily maintenance is at 20 minutes, whereas competitive machines are at about an hour, says McOllough. “That’s 40 more minutes you could be in the field or doing other activities.”
CLAAS as a group sees North America as one of its focus growth points; the U.S. and Canada are one of their top six growth countries or regions. “And it shows through the equipment they’re [the headquarters in Germany] are giving us,” says McOllough. “It’s not just combines. We’re getting more tractors, a trailed mower…all of those things are coming because they see us as a focus area.
“And they're giving us what we need to make sure we can do the best we can. This combine is proven for that,” he concludes.