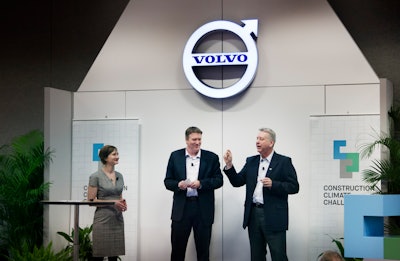
The CONEXPO-CON/AGG exhibition in Las Vegas was the venue for the latest gathering of the Construction Climate Challenge. Tackling issues such as calculating the whole life impact of building materials, the potential for cutting emissions in construction equipment and the environmental opportunities of delivering California’s high speed rail system, leading speakers discussed the climate challenges of reducing Carbon in Infrastructure Construction from their own diverse perspectives.
The Construction Climate Challenge is an initiative hosted by Volvo Construction Equipment, whose aim is to promote environmental awareness, enhance collaboration and share best practices throughout the construction industry value chain. The Las Vegas seminar was moderated by Dr. Bryan Staley, President and CEO of the Environmental Research and Education Foundation.
Dr. Staley also discussed the consequences and complexities of calculating the lifetime environmental impact of building material choices. He discussed how manufacturing processes, construction quality, transportation and material longevity all affect the whole life environmental impact calculation, adding to the difficulty of accurately determining the optimal building material choices. “Even using recycled materials, while intrinsically beneficial, doesn’t always lead to reduced emissions. Thankfully, models used to estimate emissions are becoming more sophisticated, leading to greater accuracy and the ability to accommodate site-specific optimization of emissions and cost,” commented Dr. Staley.
‘New, green standard for infrastructure development’
Dr. Staley was joined on stage by Margaret Cederoth, Sustainability Manager at the California High-Speed Rail Authority. California High-Speed Rail is a high-speed rail system currently under construction in the U.S. state of California. By 2029, the system will run from San Francisco to the Los Angeles basin in under 3 hours, at speeds capable of over 200 mph. The total system length will be about 800 miles (1,300 km) long. Cederoth described how the project also has ambitious environmental targets, which, if achieved, will see CO2 emissions reduced in the state by 176,000 million metric tonnes in its first year of operation. “The project is setting a new, green standard for infrastructure development,” said Cederoth. “This includes operating with 100% renewable energy, all steel and concrete from demolition and construction recycled, low emission equipment used on site – 40% better than average – and materials life cycle analyzed. We are promoting the use of innovative technologies to drive down CO2 emissions. Thanks to efforts such as urban greening and tree planting schemes that offset emissions, we are committed to carbon neutrality during the construction phase. The whole scheme is trying to move behaviors into a new low carbon reality.”
Intelligent, electric and connected
The final speaker was Dave Ross, Vice President of Advanced Engineering at Volvo Construction Equipment. In a wide-ranging presentation, Ross discussed the challenges facing equipment manufacturers in their efforts to achieve economic, environmental, and social sustainability. “While other industries have made huge advances in efficiency over the years, the process of construction hasn’t really changed, and is, if anything less efficient today, with major projects commonly taking longer and costing more. This actually offer us a lot of opportunities to drive down the part of emissions that derive from construction equipment.”
Ross described how the adoption of new technology is leading to a new breed of intelligent, electric and connected machines. “Volvo Construction Equipment’s HX2 prototype autonomous, battery-electric, load carrier – which is on display here at CONEXPO, is one element of an electric site research project that we predict will deliver up to a 95% reduction in carbon emissions and up to a 25% reduction in total cost of ownership,” he said. “While only a concept today, the HX2 is already six times more efficient than the latest generation haulers that use internal combustion engines.”
The presentation concluded with Ross describing how Volvo Construction Equipment has set itself the target of increasing efficiency by 10 times, thanks to the adoption of intelligent, electric and connected technology. “Not only that,” ended Ross, “We are also working towards objectives whereby our equipment delivers zero downtime, zero accidents and zero emissions.”