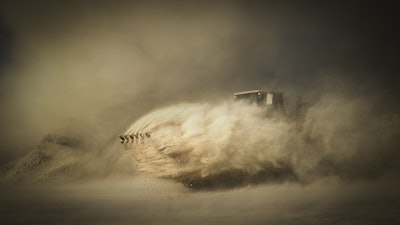
Heavy equipment operator cab designs have traditionally focused on two areas: the comfort of the operator and the ability to easily and safely operate the machine. Today, however, based on the growing body of evidence that breathing air contaminated with dust particles is harmful and potentially fatal, equipment owners (and therefore, OEMs) are increasingly interested in clean air in operator enclosures.
Dust particles of all kinds and sizes are inherent at every heavy equipment work site. Operating machines such as excavators, graders and dozers churn up veritable dust storms that release large quantities of particles into the air. Many of these particles are breathable or “respirable” and hazardous to human health. Crystalline silica dust, in particular, is associated with worker diseases and dust exposure is now OSHA regulated.
To meet the OSHA requirements, it’s recommended that a cab air quality system involve three steps: 1) let only “cleaned” and filtered fresh air into the HVAC system of a cab; 2) continue to filter the air as it recycles through a cab; and 3) monitor cab pressure to assure it’s positively pressurized. A complete three-part system, such as the RESPA Cab Air Quality System from Sy-Klone International, can also assist fleet owners to be in compliance with OSHA’s silica rule and its engineering controls for the construction industry.Sy-Klone International
What is “clean cab air”?
“Clean cab air” is air that is made as safe as possible for heavy equipment operators to breathe while working in a machine’s cab. It’s air that is first precleaned and filtered prior to entering the HVAC system and it’s air that is continuously filtered inside the operator enclosure. The goal of the precleaning and filtering processes is to remove the debris and dust, and most importantly, the dangerous and “invisible” respirable silica dust particles measuring in size from 0.3-10 micrometers. (A micrometer is one millionth of a meter and anything smaller than 40 micrometers is invisible to the human eye.)
Particles in the range of 0.3-10 micrometers are harmful because they can pass through the human body’s filtration systems (nose hair, bronchial tubes, etc.) and settle into the lower lungs. Material that gathers in the lower lungs usually and eventually works its way out of the body through the bloodstream. However, all respirable particles are not easily transported out, and some types, such as respirable crystalline silica in the 0.3-10 micrometer range, remain in the lungs.1
Additionally, OSHA has concluded that workers who inhale crystalline silica particles are at an increased risk of developing serious silica-related diseases, including silicosis (an incurable lung disease that can lead to disability and death), lung cancer, chronic obstructive pulmonary disease (COPD) and kidney disease.2
OSHA’s definition of clean cab air
Given the harmful and potentially fatal effects of inhaling respirable crystalline silica dust, OSHA issued a final rule for the construction industry (OSHA Standard 29 CFR 1926.1153) on March 26, 2016, setting a worker’s permissible exposure limit (PEL) for respirable crystalline silica dust at 50 micrograms per cubic meter of air (50 μg/m3) averaged over an 8-hour shift. (A microgram is one millionth of a gram.)
On September 23, 2017, OSHA began enforcement of the new silica dust standard. The standard requires employers to implement the engineering controls, work practices and respiratory protections listed in Table 1 of the standard, which are intended to allow equipment operators to meet the new PEL for silica dust. Employers, in kind, are turning to OEMs to design and manufacture heavy equipment with operator enclosures that comply with the engineering controls outlined in OSHA’s silica dust exposure standard.
Cab air quality systems can be integrated into any enclosed cab design.Sy-Klone International
Measuring exposure to respirable silica dust particles
To monitor a cab operator’s exposure to silica dust particles over the course of a work shift—and not just when the operator is working inside an enclosed cabin—a small device called a dosimeter is attached to the operator’s collar. The dosimeter continuously samples the air around the operator’s head throughout the 8-hour shift. At the end of the operator’s shift, the sample is analyzed for silica exposure.
Because OSHA’s silica standard requires concentrations to be averaged over an 8-hour shift, it’s vital that cabs be an area of very low exposure to compensate for the time when operators are outside of their cabs and overexposed to dust particles. With a proper cab air quality system (and OSHA engineering controls) installed, the cabins of heavy equipment can quickly become the safest place on the job site for operators.
How can OEMs provide clean cab air?
Cab air quality systems that create and maintain cleaner and safer air for operators of heavy equipment are available to OEMs as first-fit installations, as well as for retrofitting existing equipment. A complete cab air quality system should include a fresh-air unit, a recirculating-air unit and a cabin-pressure monitor.
Fresh-air unit
A fresh-air unit should integrate powered precleaning and high-efficiency filtration to preclean and filter the fresh air entering a machine’s HVAC system and to deliver continuous airflow to positively pressurize the cab.
The powered precleaner should remove more than 90% of all dust particles from the incoming fresh air before it reaches the high-efficiency filter. The delivery of “low-particulate” air is critical because high-efficiency filters by design are more restrictive and clog more quickly and the filtered air must be able to continuously flow into the operator enclosure to positively pressurize the cab.
As precleaned fresh air passes through the high-efficiency filter, the filter should capture 95% or more of the toxic respirable particles in the range of 0.3-10 micrometers to achieve the OSHA recommended dust exposure limits. In the diagram at right, powered precleaning technology is demonstrated in the RESPA Cab Air Quality System from Sy-Klone International. Powered precleaning technology available from Sy-Klone International enables the effective use of high-efficiency filters in the fresh-air unit of a cab air quality system.Sy-Klone International
- Air enters precleaner inlet.
- Louvers accelerate air as fan whips air into a vortex.
- Particles are spun against the outside wall and ejected.
- Precleaned air is pushed through the high-efficiency filter, pressurizing cab.
Recirculating-air unit
A recirculating-air unit with high-efficiency MERV 16 filtration continuously filters air as it recycles through the cab, which is particularly important because dusty air flows into the cabin as the operator enters or leaves the cab. More than 70% of the airflow in the cab passes through the high-efficiency recirculation filter, allowing the cabin air to be stripped of dust particles quickly, restoring and maintaining good air quality and reducing the accumulation of settled dust.
Cabin-pressure monitor
A cab air quality system that positively pressurizes an operator enclosure and includes a cabin-pressure monitor is highly recommended for two reasons:
- Positive pressure inside a cabin prevents dust particles from entering the cab through small openings in the enclosure and cracks in door and window seals and maintains a cleaner breathing environment for the operator;
- A cabin-pressure monitor provides continuous air pressure readings and alerts the operator when pressure inside the cab drops below a preset level insuring that the cause of the low pressure is addressed and positive cabin pressure is restored.
The cabin-pressure monitor also enables employers to proactively comply with OSHA’s recommendation to maintain continuous cab pressure.
OEMs now have the ability to meet customer demand by providing complete cab air systems that are in compliance with the engineering controls outlined in Table 1 of OSHA’s silica exposure standard.
The cabin-pressure monitor is an essential part of a complete cab air quality system as it alerts operators and employers when pressure inside an operator enclosure drops below a preset level for a predetermined period of time.Sy-Klone International
OSHA’s Table 1 silica standard engineering controls
To limit operator exposure to respirable crystalline silica dust, Table 1 of OSHA’s silica standard requires employers of machinery used in construction to implement the following engineering controls for operator cabs.3
- Be well-sealed and well-ventilated, using positive pressure.
- Have door jambs, window grooves, power line entries and other joints that work properly and are tightly sealed.
- Have heating and air conditioning so that operators can keep windows and doors closed.
- Use an intake air filter with a minimum MERV-16 rating (at least 95% efficient in the 0.3-10.0 micrometer range).
- Be kept free from settled dust by regular cleaning and maintenance to prevent dust from becoming airborne inside the enclosure. OSHA did not intend for this to be prohibitive, requiring a wipe down of the cab. Rather it was left up to the owner of the machine to decide how to implement controls or maintenance to keep dust from re-entering the air space of the operator.
Conclusion
Features such as ergonomic design, an advanced suspension system and a low noise level all help to make operators comfortable and minimize fatigue. The ability to easily control the machine and its tools is a major factor in worker and machine productivity. Now heavy equipment OEMs can add clean cab air to their factory offerings and meet the demands of operators, fleet owners and industry regulations.
References
1. https://www.oemoffhighway.com/operator-cab/article/11080603/its-what-you-cant-see-that-can-kill-you
2. https://www.osha.gov/dsg/topics/silicacrystalline/
3. Silica: Controlling Silica Dust in Construction - Heavy Equipment and Utility Vehicles Used During Demolition Activities Fact Sheet (OSHA FS-3936 - 2017)