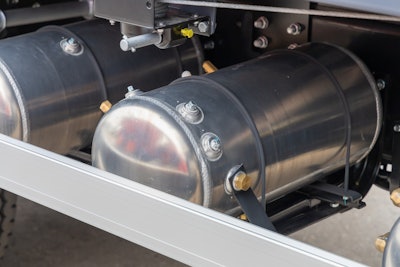
Today’s commercial vehicles tackle an incredible range of jobs across a growing number of applications and in varying environments. One common requirement among them is a reliable supply of clean, dry compressed air for the operation of brakes, lift axles, emissions controls, automated transmissions and leading-edge safety technologies like collision mitigation.
This means modern full-function air dryer technology demands three things: More dry air for the systems today’s trucks depend on, improved energy efficiency and and air system diagnostics. The emerging technology of electronic air control (EAC) addresses these evolving needs, as well as environmental regulations, while providing manufacturers with a high level of flexibility during installation.
Advancing air dryer technology
It’s essential to keep moisture, oil aerosols, and other contaminants out of a vehicle’s air system to the greatest degree possible, since they present a corrosion hazard to some of the crucial components within. Oil, in particular, can deteriorate seals, cause leaks, and damage valves and brake chamber diaphragms – so there’s a lot at stake.
Air dryers equipped with electronic pressure control incorporate a solenoid-operated valve that replaces the traditional mechanical governor. This electronically controlled governor enables precise regulation of the dryer’s charge and regeneration cycles using electronic air control software. Now the dryer can operate under different parameters in different conditions – increasing its dry air processing capability and saving energy.
A commercial vehicle air dryer with a traditional mechanical governor is engineered with two fixed setpoints that determine when the compressor charges and unloads. When the system reaches its full charge — usually 130 psi — the governor signals the compressor to unload.
However, when an air-drive system taps into the air supply — during a brake application, for instance — the pressure decreases, and when it reaches about 100 psi, the governor again signals the compressor to recharge and build pressure anew. It’s an automatic cycle based on the pressure in the tanks.
Electronic air control makes the process smarter.
Better connectivity, information and efficiency
An electronically controlled governor is operated by software that monitors information broadcast across a truck’s J1939 network – data including speed, engine torque and RPM. Using those variables, the governor can modify its charge cycle based on air system and engine demands.
For example, when a compressor is building pressure, it pulls approximately 8 to 10 HP from the engine. EAC software uses the vehicle’s operating information to adjust the compressor runtimes. Say you’re going downhill or idling: The engine is using fewer horsepower, so it’s got some energy to spare. The EAC will temporarily increase the cut-in and cut-out pressures because the compressor can charge above the standard programmed pressure without the driver losing any engine power. On the other hand, if a driver is passing another vehicle or climbing a hill, they'll want to maximize horsepower without the compressor charging. In this case, the EAC will lower the cut-in and cut-out thresholds to prevent charging. (It’s important to note the EAC software is programmed not to reduce the cut-in pressure below a safe setting, per FMVSS-121 regulation.)
While those are the generalities of EAC, the technology also delivers customizability. If the software determines an air system requires extra drying capacity – on a truck hauling multiple trailers or equipped with extra axles, for example – then it can command additional short purge cycles, providing more dry air for vehicles that need it.
Because an electronically controlled air dryer is connected to the J1939 network, it also offers maintenance benefits. Monitoring for excessive air demand can indicate system leaks or other issues, and information on regeneration cycles and the amount of air processed can help signal when it’s time for a new dryer cartridge.
New frontiers for air compressors
In an evolving propulsion landscape with an increasing focus on more environmentally friendly heavy-duty vehicles, it’s become important to develop flexible air treatment and control systems that can be integrated into both traditional internal combustion engines and new zero-emission drivetrains. This has led to the development of modular control systems as well as electric air compressors.
These modular systems can control both traditional air compressors as well as those operated by electric motors and integrate features of other electronically controlled connected systems like electronic parking brakes. Incorporating the parking brake also reduces the total weight of the air treatment system. Some current brake system features like anti-compounding and spring brake inversion can also be electronically controlled. Where original equipment manufacturers (OEMs) are concerned, these modular technologies offer scalability in the form of options for single or multiple circuit systems.
Electric-powered air compressors are also seeing adoption in various applications, providing an ideal match for alternative-drive vehicles since they run quieter than comparable piston compressors. As with EAC dryer technology, they connect to a vehicle’s controller area network and respond based on changing air demand requirements. Users will find electronic compressors equipped on both hybrid and fully electric vehicles, with various types suitable for high- or low-demand applications.
By building on the proven legacy of commercial vehicle air systems, steps are being taken toward safer, more efficient and sustainable vehicles in the future.