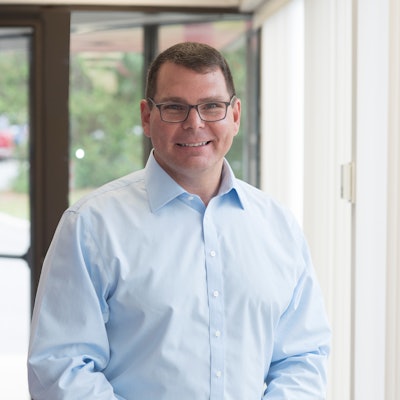
responses submitted by Derek Kuhn, President and General Manager, Sciemetric
Data, IoT & Connectivity
What role is data playing in your company, and how do you anticipate it will grow in the coming years?
Data is our bread and butter.
Over the past 30+ years, Sciemetric has worked with manufacturers to perfect how to extract, organize and derive actionable insight from the data generated by manufacturing processes. I think we have been focused on elements of Industry 4.0 tools for manufacturers decades before Industry 4.0 became a thing.
Even now, with “Industry 4.0” being mainstream in the eyes of so many, we find there is still a lot of work to do. Small to mid-sized manufacturers still struggle to make effective and practical use of their data to improve quality, yield and operational efficiency. We are helping large manufacturers regularly with the same. It’s far from in place and mainstream. Helping companies make that transition is the focus we continue to see for ourselves.
What benefits is the Internet of Things (IoT) bringing to your company, and/or the industry as a whole, and how do you see it continuing to be beneficial in the coming years?
For us, IoT (or in this context, Industrial IoT [IIoT], of which Industry 4.0 is a subset), is fundamentally about eliminating silos.
By silos, we mean that the data generated from a process or test station on a production line, or by the operation of any other mechanical system in an industrial setting, remains stuck at its point of origin. The data can’t easily be integrated into a centralized system where it can be analyzed with other pertinent data from its larger environment to paint that big contextual picture.
Equipping machines with the sensors to collect more data, or by grabbing data from the machines’ existing sensors that track their functional health, then networking all these data sources together for that big picture analysis – for continuous quality improvement, and troubleshooting – is where our focus remains because this is the kind of capability our customers need to compete and grow their businesses.
If IoT is not already being utilized by your company, do you foresee it being so in the near future, and how will your company go about using it?
We truly “eat our own dog food” and have been doing so forever. We are by no means a large manufacturer, but we benefit from the use of our own data tools and instrumentation. So we are constantly looking at how to make more effective and timely use of data, not just the part data from the production line but across any number of industrial processes. Many of our customers have asked us to bridge the discrete manufacturing process with continuous process monitoring, which we have accomplished. This allows us to include opportunities outside of the manufacturing environment.
So we need to figure out where else we can go, based on our expertise, customer traction and technology assets. The obvious direction is to apply this expertise to industrial processes and expand our product offerings to be able to take advantage of the latest cloud-based tools and computing power.
Are you seeing any new opportunities in regards to connectivity, and if so, what technologies are making these possible?
Everything is being fueled by this massive and elastic computing environment we all refer to as the cloud. Manufacturing lies in the cross-hairs of this transformation. Connectivity between the plant floor, the corner office and the supply chain is making industrial manufacturing and production near unrecognizable from even a decade ago.
In combination with this, digital sensors, special new forms of machine vision and instrumentation, coupled with data lake-based correlations of dissimilar data, is giving manufacturers more insight and more control than ever before to drive quality, efficiency and profitability.
This isn’t impacting only manufacturers, of course, but every industrial process, and the operation and management of every piece of industrial equipment, from a remote oil and gas site to the HVAC unit on the roof of an office tower.
Automation & Smart Systems
What challenges are there yet to implementing more advanced automation capabilities and what is needed to overcome those challenges?
There will always be challenges. To effectively use machine learning or AI-based systems, you must develop the algorithms that make them shine. We remain in a world where the power of the cloud has not yet been fully embraced for many reasons. The volume of data and analysis from the shop floor can overwhelm us and embracing the connectivity to allow the same to reach the cloud in a timeframe where it is relevant remains a tough ask of many customers. We solve this by ensuring we can transform the data in production real-time at the edge while still ensuring we can deal with the connectivity to enable the power of the cloud.
As we connect the shop floor, (yes, many have not yet done so) we must ensure a secure environment for business and this is a tremendous focus of ours. We are starting to see the beginnings of wireless sensors/wireless connection of machines. The promise of 5G, especially private 5G-connected shop floors, is a very interesting challenge as the data rates and volume in precision manufacturing are driven by capture and analysis of far more than simple scalar values. It will be very interesting to see how our world embraces these technologies.
Read more: 5G Enables the Next Wave of Connectivity