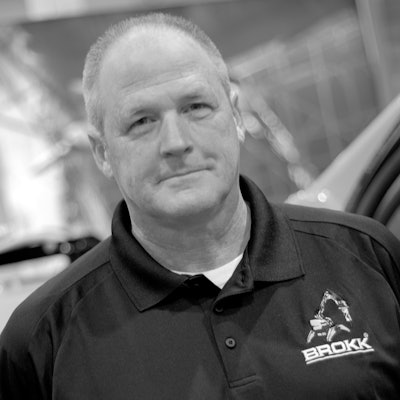
Each year, our State of the Industry issue looks at the top trends and technologies within the heavy equipment industries. We also dig into current and future market conditions, as well as regulations which may currently or in the coming years have an impact on how the industry will go about designing its equipment.
To get the best insights, we speak with executives from a variety of companies working in the industry—everyone from associations, to OEMs to component suppliers. Below are responses provided by Jeff Keeling, North American Sales and Marketing Manager, Brokk Inc.
Read all of this year's executive Q&As.
Automation & Smart Systems
How has automation helped the heavy vehicle and equipment industries become more productive?
I don’t think it’s an overstatement to say automating processes has revolutionized productivity for our customers. Demolition jobsites, for example, once required large crews with handheld tools. Workers performed hard, grueling labor that led to short- and long-term health problems and shortened careers. Enter technology, like Brokk demolition robots, that make it possible to reallocate that large crew, and to get more work done, more safely.
One customer cut the demolition crew by one-third on a recent interior demolition with two remote-controlled demolition machines. The robots are small enough to fit in a passenger elevator or climb the stairs but have the hitting power of an excavator three times its size. That made it possible, with a single operator, to access floors where even skid steers were deemed too heavy during a nearly 1 million sq. ft. (92,903 sq. m), multi-level tear out. With minimal labor requirements, the contractor was able to better utilize employees across simultaneous jobsites while increasing productivity and lowering overall labor costs.
What further benefits will automation bring to the heavy vehicle and equipment industries?
Along with greater productivity, manufacturers can create a path to safer jobsites. Having machines handle the hardest, most physically demanding work makes a big difference. With an operating distance of up to 984 ft. (300 m), remote-controlled units physically distance employees from silica dust and the strong vibrations of handheld equipment such as breakers, rivet busters and chipping guns. Long-term use of these common tools is linked to several chronic injuries, including carpel tunnel syndrome, nerve damage and hand-arm vibration syndrome. These health concerns affect a large number of construction and demolition workers, which is reflected in workman’s comp claims and insurance premiums for employers.
One concrete cutting contractor made the switch to demolition robots 20 years ago and has seen a decrease in annual compensation claims by about 50%, thanks in part to the reduced physical strain provided by these machines. The company has also seen a 25% decrease, or about $40,000-50,000 savings, in injury costs per year. Another concrete cutting operation reduced its experience modification rate, or EMR, along with workman’s comp claims with the addition of remote-controlled demolition machines. Insurance companies calculate EMR based on a company’s safety record and using it to gauge future chances of risk. Higher EMRs result in higher insurance premiums.
Customers who invest in automation invest in safety. And a safe, healthy workforce is a productive, cost-effective workforce.
How has the development and use of smart systems evolved, and what further impacts will they have on the industry?
Machines themselves are smarter, making it possible to better cope with less-than-ideal circumstances. Unreliable or faulty power sources, for example, are a problem for electric equipment. Our SmartPower technology, however, combats that. With SmartPower, an operator can still start the machine on a poor power supply, plus the system will protect the components from fluctuations. Having machines that can solve their own problems is quite amazing when you think about it, and the technology is only going to get better.
Challenges & Opportunities
What are the biggest challenges facing the industry currently, or do you see the industry facing in the coming years?
Finding skilled employees has been a challenge for years, and the situation is not improving. But, here again, technology can help save the day. Those who invest in advanced equipment are in a position to still get work done and to keep the employees they do have healthy. Also, the opportunity to be trained on and work with technology, like demolition robots, can be a recruitment and retention tool. It gives employees an opportunity to build their skillsets, which is a win-win for the employee and employer.
What are some of the biggest opportunities you see in the industry?
Rapid advancement in technology is exciting, but it can also be daunting to implement. It often means changing the way you work, and change is hard. As manufacturers, we have the opportunity to design safer, smarter, environmentally friendly, versatile equipment. We also have the opportunity to help customers realize the full potential they have access to. How many of us have a computer or mobile phone that can do a lot more than we actually use it for? The same can be true with equipment technology. A Brokk robot with a good selection of attachments, for example, does more than break material. It can crush, cut, grab and rip, drill, scarify, lift pieces of concrete and many other things, making it highly versatile. Helping customers understand how to leverage the technology ultimately can help them truly advance their businesses and the industry.
Are there any technologies or trends which you are currently excited about in the heavy-duty vehicle industry, or most looking forward to seeing in the coming years?
Battery technology is something to watch. A lot of contractors have found Brokk machines are an ideal solution for enclosed spaces, such as interior demolition, thanks to their compact size and emissions-free operation. The Brokk 70, for example, weighs just 1,235 lbs. (560 kg) and can fit through even the narrowest doorways. The next evolution for demolition equipment is to unplug the machine completely, allowing contractors to maneuver freely around the jobsite. There have been great strides in battery technology, and it will be exciting to see how it evolves.