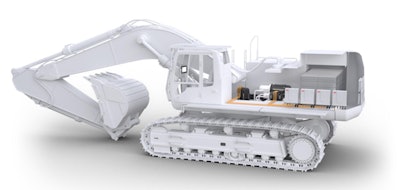
The march toward sustainability and energy efficiency has led to a notable shift toward electrified heavy working machinery, with OEMs and operators seeking groundbreaking technologies to power their machines more efficiently while further reducing their carbon footprint and operating costs.
An important component in the electric powertrain is the inverter (also known as a converter). It converts the DC voltage of the battery into the AC voltage required to drive the traction motor. By doing so, the inverter provides industrial heavy machines with the dynamic torque and speed control necessary for traction, as well as auxiliary functions such as operating the hydraulic pump in an excavator or moving the bucket on a loader.
From Two-Level to Three-Level Inverter Topology
Figure 1. This output current wave form on a two-level inverter illustrates the current ripple is higher compared to the current ripple of the three-level waveform.ABBToday, two-level inverters are widely used in electrified working machines and the automotive industry – these switch only between DC+ and DC-. A three-level topology, on the other hand, introduces an additional voltage step – the neutral – which halves the voltage step during each switching operation. Looking at the output current wave form on a two-level inverter, it is obvious that the current ripple is higher compared to the current ripple of the three-level waveform (see Figure 1). The current ripple introduces harmonic losses in an inverter-driven electric machine which has a negative impact on the motor efficiency.
Influence of Harmonics on Motor Efficiency
Looking into the losses of electric motors, there are the so-called “fundamental losses.” These are the losses that occur when supplied with an ideal sinusoidal waveform (fundamental wave). However, as soon as the motor is driven by an inverter, the current ripple as described above causes “harmonic losses” in the motor. These harmonic losses caused by a two-level inverter are typically in the range of 15% to 35% of the fundamental losses, so they have a significant impact on the motor efficiency. Using a three-level inverter will decrease harmonic losses up to 75%.
Figure 2. Pictured here, a three-level inverter will reduce the torque compared to a sinusoidal wave by only 28%, which results in a gain of 63% more power compared to a two-level driven motor-inverter system.ABB
How Much Power Can I Get Out of a Motor?
As an example, a 45 kilowatt (kW) permanent magnet motor, with the same limitation of internal temperature limits, will have different torque curves depending on the chosen inverter topology. Taking the sinusoidal values as a reference, which are typically used in datasheets, the two-level inverter will reduce usable torque by 65% due to the harmonic losses explained above.
Instead, a three-level inverter will reduce the torque compared to a sinusoidal wave by only 28%. This results in a gain of 63% more power compared to a two-level driven motor-inverter system (see Figure 2).
This boost in power delivery translates into enhanced performance and higher torque, enabling motors in heavy industrial vehicles to tackle more demanding tasks.
This effect is true at every operating point across the spectrum of speed and torque. A two-level inverter may exhibit efficiency limitations at certain operating points, but the three-level inverter is more efficient overall. This characteristic is especially pronounced at the partial load conditions where the majority of heavy machines frequently operate – creating an opportunity to reduce energy wastage, prolong battery use and minimize operating costs.
These lower losses lead to cooler operating temperatures and less stress on critical components, which extends the lifespan of the powertrain and enables cooling systems to be downsized. This is particularly valuable in working machines, where high ambient temperatures and demanding workloads are the norm.
Introducing Silicon Carbide Semiconductors
Figure 3. One option to harness SiCs is to upgrade the electronics inside two-level converters. However, these are not as efficient as three-level insulated-gate bipolar transistor (IGBT) inverters.ABBBesides the topology, the switching frequency is another measure that can positively influence motor efficiency. A recent development in power electronics is the emergence of silicon carbide (SiC) semiconductors. These are capable of higher switching speeds, which emulates an AC sinusoidal waveform more closely than a conventional silicon-based inverter. This results in reduced harmonic losses and enhanced efficiency.
One option to harness SiCs is to upgrade the electronics inside two-level converters. However, these are not as efficient as three-level insulated-gate bipolar transistor (IGBT) inverters (see Figure 3). The sharp switching characteristics of the SIC inverters (dU/dt) increase the stress on the motor insulation system. This requires greater attention on cable length and electromagnetic compatibility (EMC) measures when designing the system.
Therefore, three-level silicon inverters are still the most effective option as they strike a practical balance between improved efficiency, cost and flexibility in installation and motor selection.
From Rhäzüns With Love
ABB recently ran a comparison between two-level and three-level inverter systems on a train line running between Rhäzüns and Schiers in Switzerland (Figure 4). In the controlled study, conducted on two comparable trains running on the same line, the three-level inverter resulted in a net reduction in energy consumption exceeding 30%. This resulted from a combination of returning more energy recovered from braking into the grid and also drawing less energy to power traction due to the increased efficiency in the drivetrain.
These findings have far-reaching implications for heavy mining and construction vehicles, especially those equipped with regenerative braking systems.
Figure 4. In a controlled study, conducted on two comparable trains running on the same line, the three-level inverter resulted in a net reduction in energy consumption exceeding 30%.ABBIn fact, the company has now commissioned the first three-level inverter systems in heavy industrial machines to be introduced by the end of 2023. The projects are slated to continue into 2024, with a focus on underground mining and construction applications.
Overcoming Obstacles
While the adoption of three-level inverters promises plenty of advantages, it is not without its challenges. These advanced systems are inherently more complex than their two-level counterparts, as they feature additional switches that demand more space.
However, the improved efficiency of three-level inverters allows for a strategic downsizing of other critical components, including motors and filter components. This means engineers can effectively compensate for the increased size of the inverter itself.
Moreover, the energy savings offered by three-level inverters enable working machine OEMs to downsize their batteries or extend their battery life, effectively reducing charging times and minimizing downtime associated with recharging. Given that batteries contribute significantly to the overall cost of electrified vehicles, these efficiency gains translate into notable cost savings over the long term.
Figure 5. To prove the advantages of three-level inverters, ABB has developed the first pilot machines using 850 VDC inverters.ABBIn conclusion, the advantages of three-level inverters in heavy industrial vehicles are undeniable. With its ability to draw out more power of an electric motor, achieve superior efficiency at every operating point and reduced stress on the motor insulation system this technology has game-changing potential in the mining, construction, and material handling sectors
To prove the advantages of three-level inverters, ABB has developed the first pilot machines using 850 VDC inverters (Figure 5). In Q3 2024, serial production will start.
___________________________________________________
David Segbers is an e-mobility traction product manager at ABB Motion.