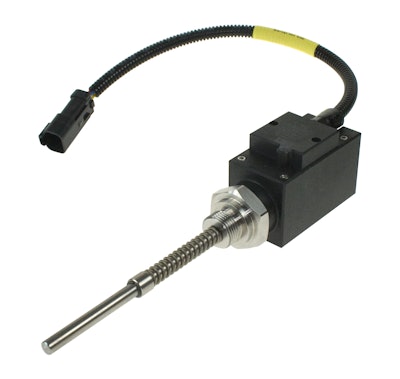
The ability to predict when a component or system will fail is key to ensuring maximum uptime for equipment operators. As such, many OEMs and component manufacturers are continually working to incorporate prognostics capabilities into their products to help reduce unscheduled downtime.
Gill Sensors & Controls Ltd. (Gill) was recently tasked by a heavy equipment OEM to develop a brake wear sensor for use in a large piece of earthmoving machinery. The goal was to develop a sensor which could inform operators of how much friction material was left in the brake system, enabling them to better predict component failure.
For this application, Gill chose to use inductive position sensing technology due to its ability to sense through stainless steel. This capability allowed the OEM to use the sensor in a wet environment where hydraulic fluid and other elements could cause contamination issues. By housing the sensor in a stainless steel cylinder, it would be protected from the elements and still provide accurate position sensing information.
“We consider this to be a significant differentiator to other position sensing technologies like potentiometers, LVDTs (linear variable displacement transducer), and Hall effect [because] they can’t sense through a barrier,” says Paul Cain, North American Business Development Manager at Gill Sensors & Controls Ltd.
How the sensor works
Placed directly onto the brake’s friction material, the sensor sends and receives energy pulses to determine the position of the material which in turn enables it to verify the thickness of the material. The sensor continually informs the machine’s brake monitoring system about what percentage of friction material remains. “The OEM’s mining customers are highly fixated on machine utilization and uptime, and they’re trying to do preventative maintenance and predictive failures,” says Cain. “If the OEM can tell their customer base how much friction material is left, they can plan a maintenance event and avoid…an unplanned failure because the cost of having one of these trucks out of service is extremely high.”
The sensor is based on Gill’s single coil inductive position sensing technology which is composed of three basic components—the coil, a piece of mild steel known as the target (or activator) and the company’s proprietary signal processing electronics. The coil transmits and receives energy which is absorbed by the activator in the form of eddy currents. Once this energy has been absorbed, the processing electronics measure the eddy current sent to the activator and the amount remaining within the activator, as well as the time duration between these events to determine position of the activator and thus the thickness of the friction material since the sensor is located directly on the material. This close proximity to the friction material helps ensure a high level of accuracy (1%). The sensor is capable of determining the remaining thickness within 1/100th of an inch in all operating conditions.
Changes in activator position are monitored over 1,000 times per second, enabling the sensor to continually determine the remaining amount of friction material.
For this particular brake wear application, Gill chose to utilize a two-coil design. One of the key benefits of the second coil is the ratiometric properties it provides which neutralize input voltage fluctuations and eliminate output signal errors. This improves temperature stability, susceptibility to outside magnetic influences and mechanical tolerance immunity. Calculation of absolute position and direction are improved, as well, as the second coil enables the sensor to take consecutive eddy current readings from both coils and receive two independent readings of the activator’s true position.
Cain says the sensor is now in full production, and has a flexible design which allows it to be customized for use in various applications.