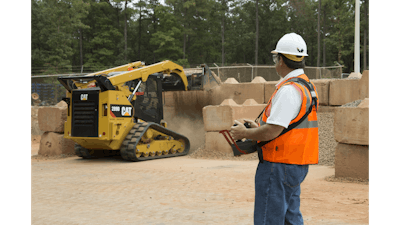
Helping making the job site more productive and efficient is the goal for many OEMs, and the way they have found to do this is by incorporating more automation technologies into their machines.
In its latest round of machine launches, Caterpillar has introduced new automation technologies to help make work on the job site easier. These technologies are also steps along what John Carpenter, in charge of the Construction Technology & Solutions division at Caterpillar, calls the company’s road to autonomy. The goal, he says, is to make the job site fully or partially autonomous, where it makes sense, providing customers with the ability to have real-time remote access to all job site processes through the use of automation, visualization and analysis technologies which will ultimately enable them to make more money.
By providing real-time machine data and connectivity between various pieces of equipment, the company is building a foundation to the eventual overall autonomy of the job site. Carpenter adds that the company’s autonomy goals are at the heart of what it is wanting to do with data collection and analysis.
Read more about Caterpillar’s investment in “big data”:
Caterpillar announces new Analytics & Innovation Division
Caterpillar partnering with Uptake to develop analytics solutions
Carpenter notes the steps along the road to autonomy are:
- Automation – Operating or controlling a process by highly independent means, reducing human intervention at the site level.
- Semi-Autonomy – Remote control of equipment and operations from an office or off-site location.
- Autonomy – Taking advantage of sophisticated technologies to enable equipment to work safely and productively with minimal input.
Now available on the company’s 323F L Hydraulic Excavators is Cat GRADE with ASSIST which expands upon the standard Cat Connect GRADE product by adding semi-autonomous capabilities. Brian Stellbrink, Excavator Market Professional at Caterpillar, explains that the system automates the boom and bucket functions of the excavator, particularly the boom height and bucket angle. The grade target is entered into the operator display and once the bucket gets within 4 in. of that target the system automatically takes over boom and bucket movements to ensure proper grading. Operators simply have to control the speed using a single lever.
According to Stellbrink, utilization of this system can help operators achieve up to 30% faster grading. It also helps protect the grade, minimizing opportunities for overdigging and thus rework, as well as the need for support personnel on the job site to monitor and check the grade for accuracy. He notes the system can also be beneficial for unskilled operators by providing them with an easier to use system on which they can build their skills.
The new D6N dozer comes equipped with Cat GRADE with Slope Assist which automatically maintains grade and slope orientation based on pre-established blade angles entered into the operator display. This enables up to an 80% reduction in manual inputs by the operator, helping minimize fatigue during the work day. Sam Meeker, Product Application Specialist at Caterpillar, says this system also enables novice operators to enter the cab and immediately operate the dozer like an expert. And because the system is integrated directly into the dozer at the factory, no additional tools or software need to be added to the machine to aid with grade accuracy.
Remote operation, also an element of Caterpillar’s autonomous job site goal, is now an available option for its D Series Skid Steer, Multi Terrain and Compact Track Loaders. The RemoteTask remote control system was developed by Caterpillar and TORC Robotics, and enables operators to precisely control a machine from outside the operator cab. This enables them to have better visibility on the task at hand, as well as keep them working at a safe distance when necessary. Jeff Griffith, Senior Market Professional at Caterpillar, says the remote control mimics the in-cab controls of the machine, making it easy for operators to transition from manual to remote operation. All controls found within the machine are included on the remote controller.
The remote controller has a signal reach of 1,000 ft. and provides almost instantaneous response, ensuring there is no lag between operator input and machine functionality. If the signal between the remote controller and the machine is somehow lost—such as if the operator were to drop the controller or fall—the machine stops within half a second of losing that signal, ensuring safety for all on the job site.
Read about more recent Caterpillar machine launches featuring technology enhancements for job site automation and improved operational efficiency.
Caterpillar introduces new B-Series Tandem Vibratory Rollers
Cat AP600F, AP655F pavers feature increased technology, quick-heating screed
New Cat 307E2 mini excavator includes High Definition Hydraulics for improved performance
Caterpillar introduces suite of integrated technologies for M Series Motor Graders