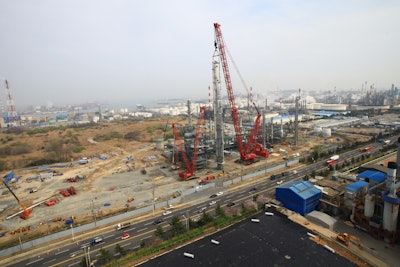
Lifting a 92 m tall wash tower that weighs 670 t with just 15 m of space for the counterweight sounds nearly impossible. But it is just the sort of problem that Manitowoc’s Variable Position Counterweight (VPC) system was designed to overcome.
Fitted to the Manitowoc 31000 crawler crane, the largest of three cranes to feature the system, the VPC enabled the 2,300 t capacity crane to complete the mega lift with relative ease, saving more than half of the time and cost compared to using an alternative conventional crane.
The lift took just a few hours and took place at Korea Petrochemical Ind. Co., LTD’s plant in Ulsan, South Korea. The Manitowoc 31000 had to be positioned between existing refinery equipment and a small river, which left just 15 m for the counterweight. No conventional wheeled counterweight trolley could fit in such a small space but the great advantage of the 31000’s VPC system is that it is suspended above the ground, therefore minimizing the crane’s footprint and – as a further advantage – saving ground preparation ahead of the lift.
The Manitowoc 31000 is operated by South Korea’s Chunjo Construction Co., one of the world’s largest crane fleet owners. The company was delighted to show, once again, how this unique crane can perform lifts far quicker and at a lower cost than conventional high capacity cranes, as Jang Hwan Chang, chairman at Chunjo, explains.
“Any other crane would have taken eight months to complete this lift but we did it in just three – no other crane would be able to come close to that timeframe,” he says. “Manitowoc’s flagship crawler crane overcomes the most challenging and costly lifts, and brings a fresh approach to construction challenges. We are delighted to see it perform. Each lift is getting bigger and we have more jobs lined up that will change the game in terms of what’s expected from high capacity cranes.”
As well as the Manitowoc 31000, the VPC system is standard on the 650 t (716 USt) capacity MLC650 and the 300 t (330 USt) capacity MLC300. These two cranes bring the same benefits of the unique moving counterweight innovation to a wider pool of users.
Using its Manitowoc 31000 at the refinery in Ulsan, Chunjo avoided a large amount of time-consuming and costly work. A conventional crane would have lifted the tower in two sections. Scaffolding would have been needed around the first half of the tower, to allow workers to attach the second, top section. In addition, the river to the rear of the job site would have needed to have been filled to carry the wheeled counterweight trolley required to perform the lift.
Chunjo’s 31000 was transported to the Ulsan petrochemical plant from a previous job at a thermoelectric power plant in Taean, 400 km away. Once on site, the crane was assembled in nine days and positioned in a 40 m wide gap between plant equipment and a creek. From there the 31000, together with a Manitowoc 18000 support crane, lifted the 670 t tower into place. The Manitowoc 31000 was rigged with a 120 m main boom and completed the lift in just a few hours.
The VPC system on the Manitowoc 31000 automatically positions the counterweight to fit the required lift and ranges from 8 m fully retracted to 29 m fully extended. The VPC system on the Manitowoc MLC650 and Manitowoc MLC300 does not require a fixed mast. It moves the standard crane counterweight along a rotating bed and is automatically positioned to fit the required lift. This reduces ground preparation, lowers ground-bearing pressure and requires less counterweight, without sacrificing capacity.
A capacity-enhancing VPC-MAX attachment is also available for both the MLC650 and MLC300 that increases capacity, and boom and jib combination lengths.
Established in 2009, Chunjo Construction Co. has fast become one of the largest construction companies in South Korea. The company has 110 in-house crane operators and runs a fleet of 115 Manitowoc cranes, including Manitowoc crawler cranes, Potain tower cranes and Grove mobile cranes. Chunjo develops projects across Asia, the Middle East, Africa and South America.